Top Five Advantages of Industrial Automation
Automation has become a vital tool for industrial facilities that need to improve productivity in the workplace. But did you know there are other advantages as well? For those manufacturers who are slow to adopt automation, this blog will explain the ways in which automation helps manufacturers and other industrial businesses streamline production, enhance quality, reduce waste, manage labor shortages and improve safety in the facility, all of which present significant financial benefits that will help provide a speedy return on investment.
What is Industrial Automation?
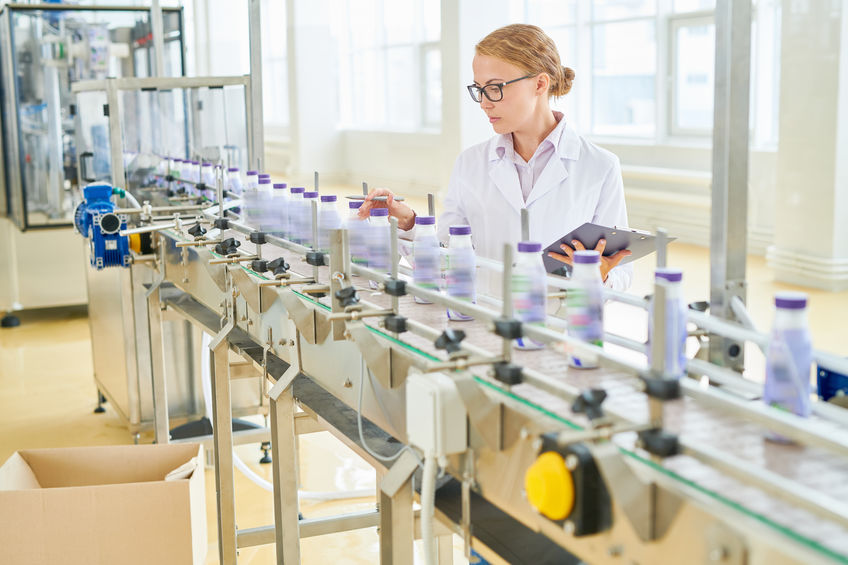
Automation of industrial processes is intended to help organizations achieve higher levels of efficiency, productivity, quality and – above all else – profitability. Automated equipment, systems and processes are designed to reduce the amount of human intervention in assembly, processing, inspection, packaging, palletizing, material handling and other industrial operations.
In addition, automated equipment is designed and programmed to perform these functions in a swift fashion with great accuracy and repeatability and can typically do so around the clock, if desired. There are automated systems available for nearly every type of industrial operation and task.
Fortunately, today’s automation technologies are becoming more and more refined and capable while, at the same time, programming has been simplified, installation is becoming easier and many automation providers are developing more affordable options allowing even small and mid-sized manufacturers to reap the benefits – of which there are plenty to be had.
Top 5 Advantages of Automation
To make it easier to understand how automation can benefit any industrial business from small to large, we’ve compiled a list of the top five advantages of automation, as follows:
- Increased production rates: Automated equipment and robots can perform tasks faster and with more efficiency, consistency and accuracy than human workers. Automated machines can perform around the clock until they are programmed to stop, they run out of raw material or maintenance is required. All of this amounts to more productivity and throughput, allowing manufacturers to beat previous production levels, meet growing productivity goals and reduce lead times, providing a competitive advantage over other participants in the same industry.
- Overcome labor shortages: Because automation makes it possible to run equipment without human intervention, the installation of automated equipment will help alleviate the challenges associated with the labor shortage. Current employees will appreciate being assigned to more complex, less repetitive tasks and the business will see more profit when paying salaries to employees who perform strategic or intricate tasks that provide more value to the organization. In addition, it is also often less costly to install automated equipment than it is to train, retain and pay human employees over time.
- Improved quality: Because robots are designed to be accurate and consistent and can perform the same task over and over again, reliably, without becoming bored or tired, it eliminates human errors that often lead to faulty products, thus enhancing the quality of finished products. This also helps eliminate scrap and rework, which can become a financial burden on a business. In addition, the reduction of waste and scrap will reduce environmental impact and help businesses reach their sustainability goals and expectations by consumers leading to a competitive advantage.
- Enhanced facility safety: There are multiple ways in which automation can improve the safety of the facility. Automated safety equipment can be used to prevent employees from entering dangerous, hazardous and restricted areas by providing a barrier that is activated upon entry. In addition, because automated equipment and robots can be used in hazardous areas, it will also prevent injuries that might be sustained by human workers who previously operated manual equipment in these areas. In addition, using automation to accomplish repetitive tasks such as the lifting, bending and twisting motions associated with material handling, palletizing, machine tending and other operations, will reduce the occurrence of repetitive motion and musculoskeletal injuries among staff. All of these safety enhancements allow for a workplace with fewer injuries and will reduce the costs associated with them.
- Increased versatility: As consumers desire more choices and trends come and go faster than ever before, versatility and flexibility are increasingly important to manufacturers who wish to remain competitive. Because today’s automated equipment and robots are easier to program than past iterations, it is possible to quickly reprogram them to adapt to other tasks. Additionally, many robots can be moved to other locations and outfitted with a variety of end-of-arm tooling, allowing them to be moved around the facility to handle new tasks when production needs fluctuate.
It is easy to see that automation provides industrial facilities and manufacturers with more efficient operation, greater throughput, enhanced quality, greater flexibility and fewer safety incidents, which helps reduce operating costs and boosts the bottom line, providing a fast return on investment and the competitive advantage that is necessary in today’s challenging industrial environment.
For more information on how automation can help improve your manufacturing process, please reach out to JHFOSTER.