Pneumatic Systems: A Perfect Fit for Industrial Applications
Pneumatic, or compressed air-driven, systems have been used to achieve mechanical motion in industrial machinery for over 100 years and, in more recent times, pneumatic systems have advanced, expanding the range of pneumatic applications to include robotics, automated industrial equipment, processes and motion control in a variety of industries. The popularity of pneumatics stems from the many advantages and adaptability it brings to the table in a variety of uses and industrial applications.
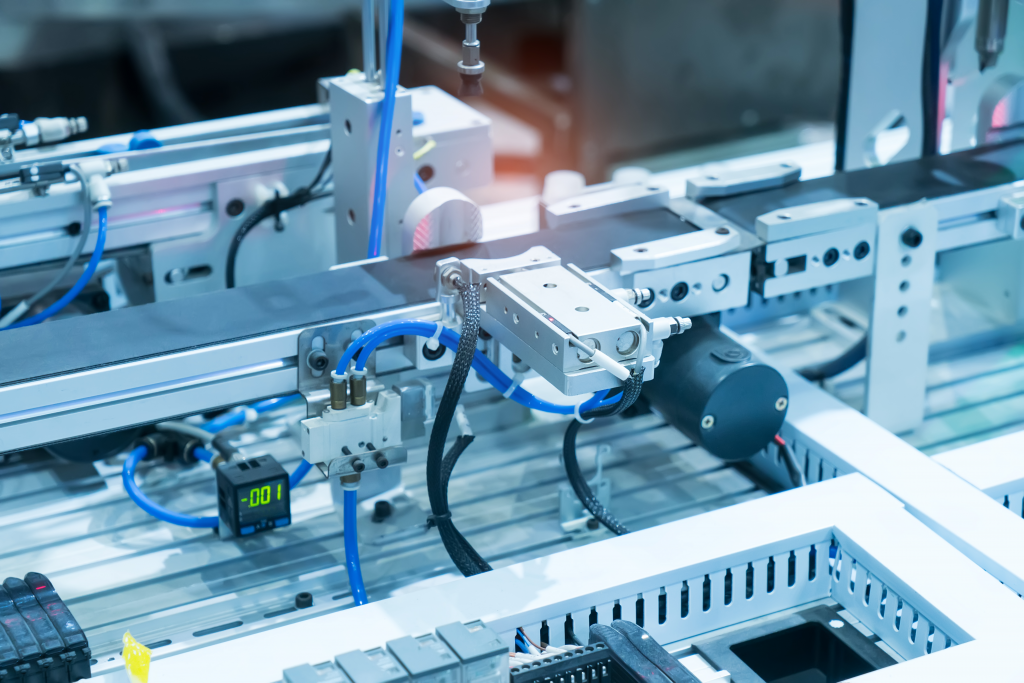
What is a Pneumatic System?
Simply put, pneumatic systems provide an uncomplicated, economical and reliable way to make things move. Using compressed air, pneumatic systems move cylinders, motors or other parts on all types of automated machinery, including:
- Fabrication equipment
- Packing machinery
- Paint spraying equipment
- Filling equipment
- Robotic end of arm tooling
- Material handling machines
- Presses
- Air-powered tools
- Many other applications in a wide range of industries.
Pneumatic systems use compressed, pressurized air to create a force that, in turn, moves a load. Depending on the equipment and applications to which pneumatics are being applied, typical motions might include pushing, pulling, lifting or holding. While the operating principle of a pneumatic system is simple, the consistency and quality of the supplied air are often crucial to the performance of the equipment and machines being powered by the pneumatic system. For this reason, it’s important that the system is designed properly with all the essential components.
The Advantages of Pneumatic Systems
Pneumatic systems provide many advantages in industrial settings as they are suitable for applications that require high force, high speed and accuracy. Pneumatic systems are also very cost-effective as they rely on a supply of free atmospheric air and reasonably priced components. Pneumatic systems are also relatively simple to design, install and maintain. The components used in pneumatic systems are durable, which lends reliability to the system and reduces maintenance requirements. Finally, pneumatic systems function well in challenging industrial environments, including those that are dirty and dusty, as well as those that feature high process temperatures. And, because they are air operated, they can be safe for use in hazardous locations where electric shock, fire or explosion are potential issues.
Applications for Pneumatic Systems
Because pneumatic systems provide many advantages in industrial settings, along with precise motion control, high speeds and force, they can effectively be used as both a working and control medium to facilitate a variety of rotational, linear or direction-changing movements at high speeds in a multitude of applications across a wide variety of industries, such as food and chemical processing, industry/manufacturing, material handling, packaging and filling. Let’s take a look at some of the most common pneumatically driven equipment and applications within each industry.
Food and Chemical Processing | Because food and chemicals often require clean, dry, pure air during manufacturing, pneumatically driven equipment is often preferred in these industries. Some common applications include: |
Cutting: Compressed air-driven tools such as knives and rotary blades are used to cut, slice, dice and grate food products. | |
Mixing: Food and chemical processors rely on pneumatics to agitate, aerate and mix ingredients in large- and small-scale mixers and blenders. | |
Dispensing: Chemical and food manufacturing relies on moving powders, liquids and grains through pipe systems. This is often achieved via air-driven systems that provide vacuum pressure and operate motion-controlled valves to dispense these ingredients. | |
Shaping: Pneumatic presses are used to mince, pulp and shape soft materials such as cheese and bread. |
Industry/Manufacturing | Pneumatic systems are used in almost every industrial and manufacturing setting, such as: |
Automotive manufacturing: Here, compressed air is used to fill tires, paint vehicles, operate robot end of arm tooling on assembly lines and operate plasma cutting and welding equipment. | |
Construction: Many types of construction equipment rely on pneumatics, including jackhammers, drills, heavy-duty machinery and air powered tools, such as nail guns. | |
General manufacturing: Pneumatics often power conveyors; stamping, drilling and punching equipment; assembly systems and plastics machinery |
Material Handling | Pneumatics can be used to move bulk goods from the point of origin to a destination point in a variety of ways. |
Conveying systems: Pneumatic conveying systems can provide the force to move, sort and transport nearly any type of material or product from point A to point B. | |
Handling sensitive or free-flowing materials: Many products and materials can’t be moved via open-air or exposed conveying systems for sanitary or other reasons, so pneumatics can be used to move materials such as dry powders and granules through enclosed piping using vacuum pressure. This is also useful for ingredients where material loss associated with exposed conveying equipment is an issue. |
Packaging and Filling | Pneumatic systems are ideal for the operation of packaging and filling equipment as they provide precise and accurate motion. |
Packaging: Compressed air and vacuum is suitable for cleaning, filling and sealing packages. | |
Pallet loading/unloading: Pneumatic cylinders and systems are used to operate pallet-loading machines, unloading stations and other automated packing equipment. | |
Ingredient dispensing: Pneumatic filling systems are used to dispense free-flowing materials or products such as grains, weigh them and discharge them into packaging or process equipment. | |
Filling: Pneumatic filling stations use compressed air to inject food products, beverages, chemicals, pharmaceuticals and cosmetics into bottles or containers. |
Pneumatic systems are widely used in these and many other applications because they provide a reliable, effective, precise, safe and clean source power capable of moving much of the automated machinery and equipment that makes industry go ‘round. For more information on designing or installing a pneumatic system for your application, please contact JHFOSTER.