Versatile Pick and Place Robots Provide Speed and Consistency
Modern industrial facilities rely on robots of all kinds to gain efficiency, increase throughput and improve safety. One of the most employed types of automation, pick and place robots speed up the process of picking up parts and placing them in other locations, helping to increase production rates, reduce bottlenecks and spare human workers from repetitive motion injuries while allowing them to focus on more interesting or complex tasks. This category of robots includes several types and offers a range of benefits for manufacturing, warehousing and other industries. Here, we will explain how pick and place robots work, outline the benefits users can expect to achieve with pick and place automation, as well as the applications and industries where they are commonly used.
How Pick and Place Robots Work
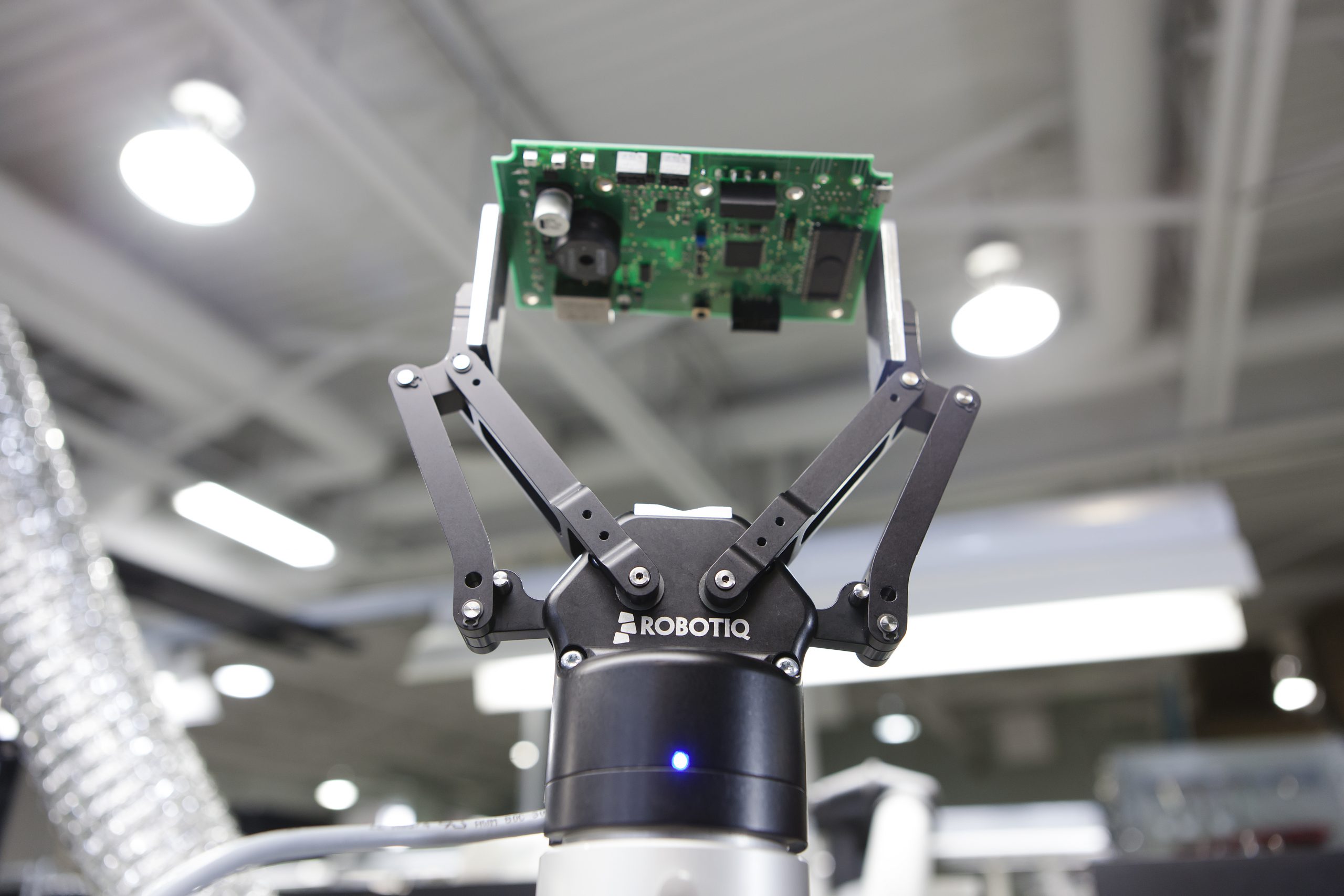
How Pick and Place Robots Work
Pick and place robots are usually mounted on a stable surface from which they can reach different areas within the work zone to perform the necessary task of picking up parts, objects or products and placing them in another location. A variety of end-of-arm tooling options, such as manipulators and grippers, allow pick and place robots to perform tasks such as assembly, packaging or bin picking. With the addition of advanced vision systems, pick and place robots can identify, grasp, move and inspect these objects, allowing them complete mundane tasks such as picking objects from an assembly line and moving them to the next location or retrieving objects and packing them in a box.
Benefits of Pick and Place Robots
Pick and place robots bring speed and consistency to the table, which allows pick and place automation to reduce bottlenecks and increase throughput and accuracy, while also reducing on-the-job injuries in human employees. Some of the major benefits include:
- Speed of operation is one of the best reasons to employ pick and place robots as they can lift and move many more objects over a shorter period of time than human workers. robots Some are capable of performing dozens of picks per minute, depending on the payload and distance.
- High productivity is possible due to the high operating speed of pick and place robots. The high speed allows modern industrial users to increase production rates and throughput. In addition, pick and place robots can work without breaks, shift changes or interruptions, allowing even more productivity as compared to human workers.
- Consistent operation is possible with pick and place robots as they are programmed to do the job over and over again without the mistakes that may occur with human error.
- Safer workspaces are possible when using pick and place robots because it eliminates injuries such as repetitive motion injuries, back injuries or crushing injuries (if objects being reached for fall) in human workers when they perform the same lifting and moving tasks.
- Flexibility is another perk of pick and place robots. Thanks to the ease of programming and the availability of various end-of-arm tooling options they can handle a variety of products in various settings.
- Reduced contamination is also a plus if the pick and place robot is used in food, pharmaceutical, electronics or medical device manufacturing where contamination can be introduced by human workers handling sensitive or regulated products.
Applications for Pick and Place Robots
Pick and place robots are most often used for handling and placing objects on a production line, packaging line or in a warehouse and are usually employed in high-volume environments where they can quickly, safely and accurately place products onto conveyor belts, production equipment or packages. However, pick and place robots are versatile machines that can be used in a variety of industries and settings, including:
Manufacturing | Packaging | Bin picking |
Pick and place robots are used to pick up and place parts, objects or products onto conveyor belts or other production equipment with speed and accuracy. | Pick and place automation can be used to pick up finished product and place it into boxes or bags. Other pick and place robots may be used to place boxed items onto pallets for shipping. | Assembly lines usually involve selecting components from bins and placing them in other locations for assembly or packaging, pick and place robots can handle these tasks with speed, accuracy and consistency. Those equipped with vision systems can even pick by color, sizes and shapes. |
Inspection | Kitting | Sorting |
Pick and place robots with advanced vision systems can grasp products off a moving line and inspect them for defects or flaws, then place them back on the line if they pass inspection or place them into a bin if they do not. | Pick and place automation can assemble kits of parts or products at high rates with accuracy and consistency. | Pick and place technology can be programmed to pick up and sort products by size, shape, color or other specifications. |
Types of Pick and Place Robots
There are several types of pick and place robots available for every need, including:
Robotic arms are the most common type of pick and place robot. Five-axis robots are often used for standard pick and place applications, while 6-axis robots are needed for more complex applications that require turning or rotating of objects. |
Cartesian robots move in three orthogonal axes and offer great positioning accuracy. |
Delta robots, which usually have at least three arms and a vision system, are often used where the pick and place robot will need to pick items in groups and place them in assembly patterns. |
Fast-pick robots are well suited for use in medium- to high-volume applications with many SKUs. These are often used where the picking process needs to be fully automated. |
Collaborative robots, which include advanced safety features so they may be used alongside human workers, can be used to “walk” with human employees to pick sites to create optimal routes and minimize transporting time. |
With so much versatility, speed and consistency, it’s easy to see why pick and place robots are widely used throughout the manufacturing, packaging and warehousing industries. For assistance finding the right robot for your pick and place application, please contact JHFOSTER.