Automation Enables Cost-Efficient Proactive Maintenance Strategies
Asset-heavy facilities often struggle to achieve a balance between keeping equipment running and managing costs; however, as machines become more connected thanks to automation and Industry 4.0, it’s becoming easier to cost effectively manage and maintain equipment in a more proactive way.
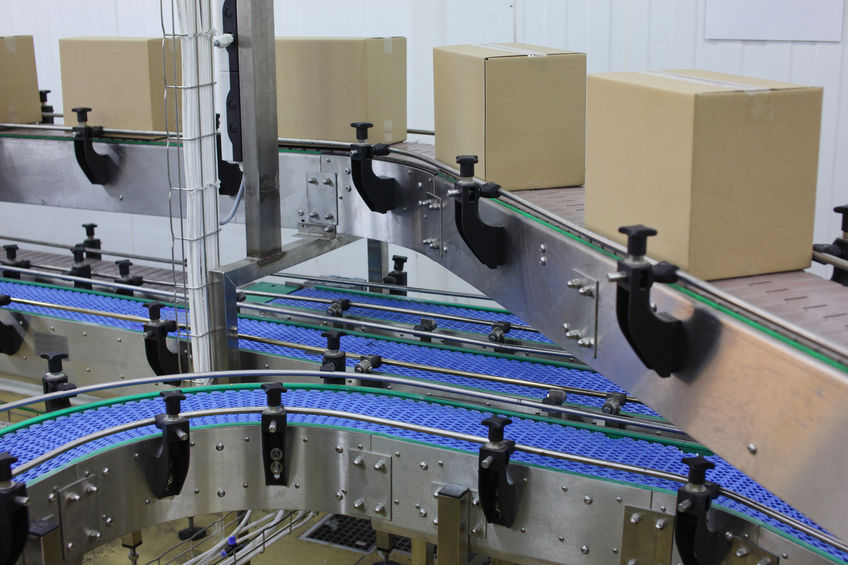
While many facilities rely on reactive maintenance, meaning equipment is repaired after a failure, this is not cost effective as downtime that reduces or stops productivity is startlingly expensive, with some statistics citing the cost of downtime at $250,000 or more per hour. For this reason, a move to a more proactive maintenance strategy, such as predictive maintenance (PDM), encourages early recognition and repair of faults before catastrophic failure.
Being proactive versus reactive not only saves money by preventing downtime, but also provides a host of additional benefits and is becoming easier to employ thanks to modern technologies, such as sensors, automation and data analytics, which collect information, analyze it and recognize abnormalities so that they can be attended to before failure occurs.
Sensors and Automation Support Proactive Maintenance
Proactive maintenance, such as PDM, relies on data collected from a variety of sensors on automated machinery that monitor the current state of an asset or the process. Depending on the connectivity of the sensors, they may send the data to a Computerized Maintenance Management System (CMMS), through an analytical software program that uses machine learning or artificial intelligence to identify trends or simply send an alert to a tech if something is out of programmed specifications. In a proactive maintenance environment, the trended data or alerts can be used to identify abnormal readings that predict future issues, allowing maintenance teams to schedule necessary tasks and order the required parts in an effort to prevent a catastrophic failure and extended downtime.
The Benefits of Proactive Maintenance Strategies
The data provided by sensors and automation, along with the increasing use of Industrial Internet of Things (IIoT) and Industry 4.0 technologies that allow more connectivity and faster data analysis, takes proactive and PDM strategies to the next level because they provide very detailed information, allowing technicians to make more informed and actionable decisions about what maintenance activities will need to be performed and when. While the biggest benefit is preventing failure, there are other advantages, as well, such as:
Prevention of lost production | Extended asset lifetime | Reduced maintenance costs |
Statistics show that predictive maintenance has the ability to reduce unplanned downtime between 9% and 20% in most facilities and that automating the process can further increase that percentage – with some statistics saying unscheduled downtime can be reduced by 50% and repair and overhaul time can be slashed up to 60%. | Automation-based proactive maintenance that enables the monitoring, maintenance and optimization of assets not only provides more availability of equipment but can also provide better insight into assets via real-time monitoring and the prediction of events before they occur, which enables maintenance crews to take immediate action on smaller repairs before they cause catastrophic failure, thereby extending the lifetime of the machine. | In addition to preventing downtime and equipment failure, the insight and visibility of automation-based proactive maintenance allows planning and prioritizing of maintenance tasks and the creation of optimal inspection routines based on the actual needs and usage of the equipment versus the suggested maintenance schedules based on calendar time. This not only keeps equipment in better condition and running longer, but it frees maintenance techs from doing routinely scheduled maintenance that may not actually be necessary, reducing costs associated with labor and spare parts. |
Increased productivity | Reduced spare parts inventory | |
While automation-based proactive maintenance certainly increases the productivity and throughput of the entire facility, it also helps increase productivity of the maintenance department as technicians will spend less time putting out fires and can be available for scheduled and critical tasks. In addition, when data is automatically collected and sent to a CMMS or software program for analysis, this means that technicians are no longer required to be in the field collecting data and returning to the department to manually log the data, reducing time spent in the field, as well as human recording errors. | When there is advanced knowledge of the tasks that need to be performed and when they will need to be done, it is possible to order replacement parts on a schedule that allows enough time for arrival before the repair is necessary. Depending on the level of automation, it may also be possible to have parts automatically ordered when a task is scheduled or a workorder is created. This allows facilities to reduce excessive stocking of replacement parts, while still ensuring that maintenance crews will have the necessary parts on hand when needed. |
Today’s connected facilities, automated equipment and advanced analytics allow more proactive maintenance strategies, which not only reduce costly downtime and extend asset lifecycles, but also enable facilities to reduce costs associated with labor and spare parts inventories, all of which benefit the bottom line.
For more information on sensors and automation technologies that can contribute to a proactive maintenance strategy, please contact JHFOSTER.