Using Manufacturing Analytics to Unlock Operational Insights
Smart sensors and devices associated with the Industrial Internet of Things (IIoT) and Industry 4.0 allow automated manufacturing equipment to communicate with specialized software and applications, providing visibility into machinery and processes. Savvy manufacturers are using this deeper understanding to unlock operational insights and make informed, real-time decisions that boost efficiency and throughput, enhance quality and cut costs to optimize production.
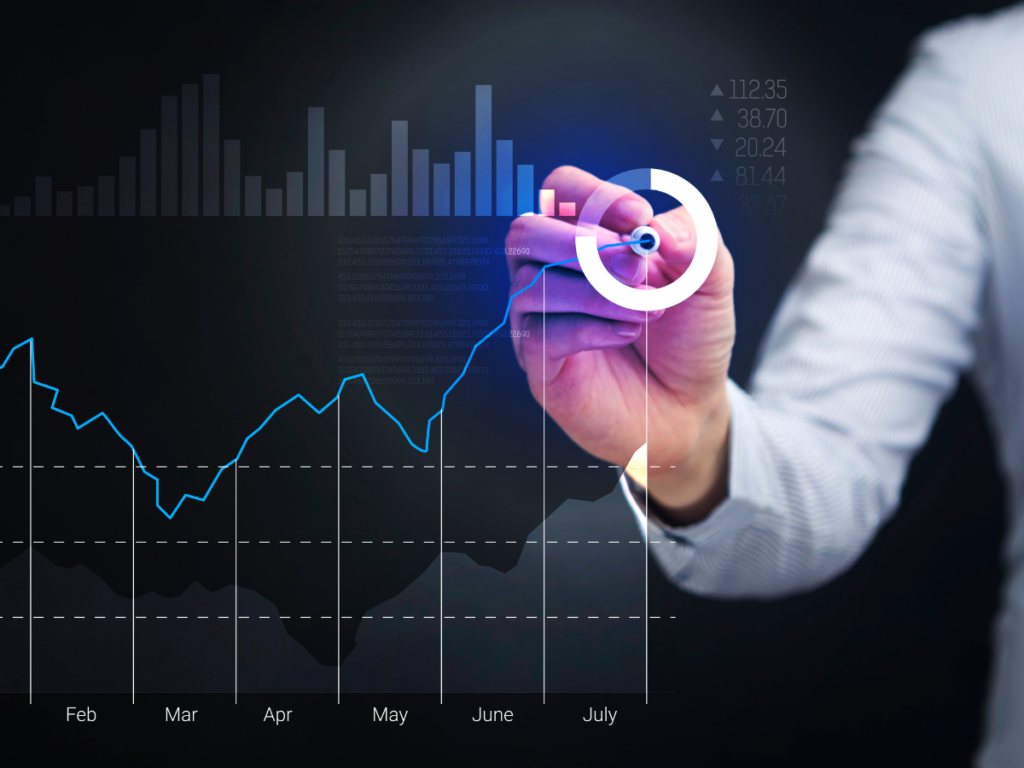
What is Manufacturing Analytics?
In order to make real-time, informed decisions, manufacturers need to gather data and information about the equipment and process. Traditionally, this has been done using paper and pencil to record data, fill out forms and create histories for operational and maintenance activities that were keyed into databases and analyzed at a later date. The trouble with this manual method was that it was time consuming, subject to human error and could only provide historical data, which did not promote visibility into current operations or provide of-the-minute actionable information.
However, today’s IIoT and Industry 4.0 technologies, such as intelligent sensors, smart devices and analytical software, nearly eliminate the labor-intensive human element and use advanced analytics to provide real-time insight into current operations. Typically this involves using smart sensors and edge devices mounted on equipment or internal to the process that capture real-time data and feed it into platforms that use advanced analytics and algorithms and then return the most crucial information to the operators who may then use this knowledge to quickly adjust the process or equipment to increase efficiency, return production to proper parameters, request work orders or take other actions that will optimize the manufacturing process.
5 Ways to Use Manufacturing Analytics
While manufacturing analytics can provide deeper understanding and a wealth of critical information, many manufacturers don’t know exactly how or where to apply the acquired knowledge. Below we outline five use cases for manufacturing analytics that can help optimize production.
Predictive Maintenance | One of the most common applications for manufacturing analytics is using the information to monitor critical production equipment so that any abnormal behaviors may be addressed before they become bigger issues that lead to downtime. Analytical software can quickly examine and analyze equipment data to detect faults, vibrations, upsets, electrical or other issues that may predict an upcoming failure so that operators can alert technicians that maintenance will soon be needed. It is also possible that advanced predictive analytics can help technicians troubleshoot the issue to determine the root cause, reducing time spent investigating faults. Predicting maintenance needs in this way allows technicians to order parts in advance, further decreasing downtime hours. Since the average cost of downtime in a manufacturing facility is estimated to be over $200,000 an hour, reducing or eliminating unplanned outages can be an effective way to cut costs and increase efficiency and throughput. |
Demand Forecasting | As consumer tastes change, so too does demand for products. To stay ahead of the game, smart manufacturers rely on data analytics to forecast customer demand and future trends based on information regarding fluctuations in customer orders, seasonal trends and market changes. Using this knowledge, manufacturers can adjust their output and production schedules so they aren’t producing too much or too little of a product at any given time. In addition, the information can be used to manage inventory, the raw material supply chain, production schedules and labor hours, helping to control costs and ensure sufficient throughput on an as-needed basis. |
Process Control and Management | Manufacturing data analytics can be used to track the production process and send alerts to operators when a process variable goes astray. By providing real-time information and alerts when the process moves out of spec – such as a too-high or too-low process temperature – operators can quickly adjust equipment or process controls to return to the proper operating conditions, preventing a bad batch. Using manufacturing analytics in this way improves product quality, reduces waste, increases efficiency and throughput and slashes material and labor costs for re-work. |
Maximize Throughput | Manufacturing analytics can be applied to study yield and throughput to ensure that production equipment is being used in the most efficient way. Analyzed data can be studied to detect bottlenecks, inefficiencies and recurring downtime within the process that may be limiting throughput. Advanced analytics can help operators identify where production tweaks can be made to optimize throughput. This can help squeeze every ounce of efficiency out of existing equipment without adding a new line or an additional shift. |
Improving Product Quality | Manufacturers can apply data analytics to product quality to ensure that they are producing the highest quality product possible at all times, reducing scrap and waste and promoting customer satisfaction. Analyzing product quality and inspection data in real-time allows manufacturers to detect any quality issues downstream so that upstream operators can be alerted and adjust processes or production parameters to ensure products meet quality standards. |
Using manufacturing data analytics to optimize production can help manufacturers remain competitive. Contact an expert at JHFOSTER for more information on IIoT technologies and data analytics that can unlock insights and help your operation cut costs, improve product quality, reduce unplanned downtime, gain efficiency and maximize throughput.