Human Machine Collaboration Optimizes Productivity
If you’ve ever asked Siri for the weather, ordered vitamins through Alexa or turned on the lights at home via your smartphone, you’ve collaborated with a smart machine to complete a task in the most efficient manner. Similarly, human machine collaboration is making possible a new era in the manufacturing industry where there are more interactions between humans and automated machinery, which is helping manufacturers streamline processes, optimize productivity and gain efficiency.
What Exactly is Human Machine Collaboration?
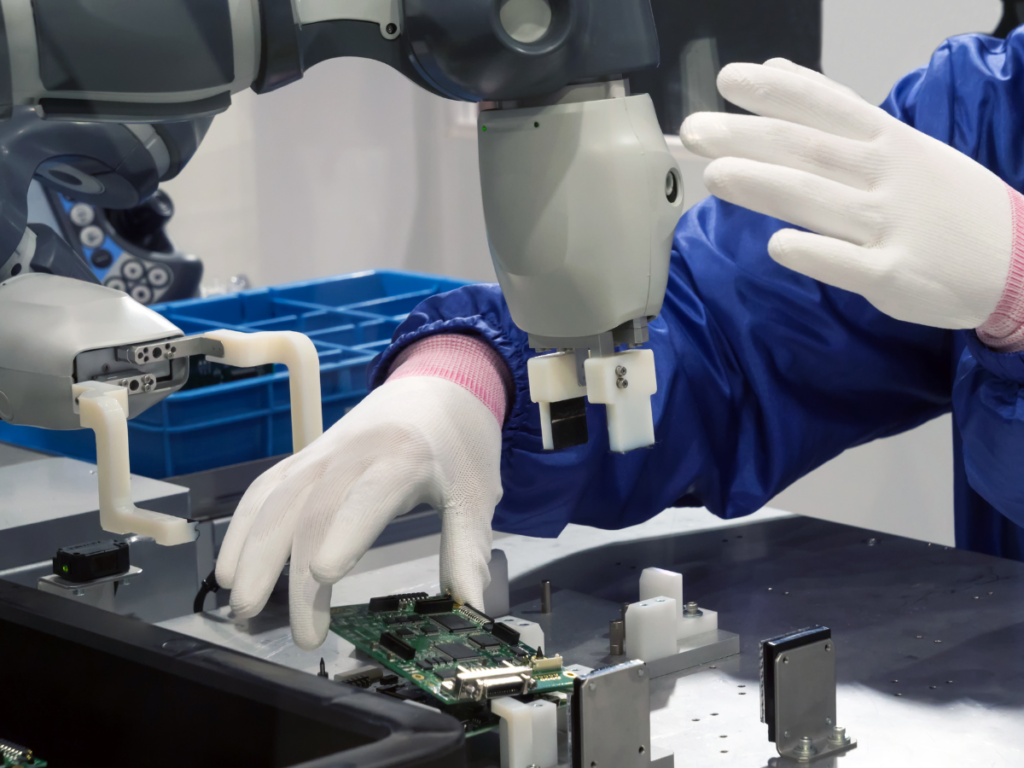
Human machine collaboration is the integration of the human workforce and automated equipment that is intended to help increase efficiency. In its simplest form, human machine collaboration involves a human machine interface on automated machinery that allows operators to easily read information about the health of the machine and process or to more easily and intuitively control the machine or process.
A more sophisticated form of human machine collaboration would involve a work cell where a human employee works side-by-side with a collaborative robot to complete a task together. Taking it a step further, automated equipment or robots equipped with machine vision, machine learning, artificial intelligence and/or advanced analytics can perform a task and provide data or information in real time, enabling the human operator to make informed and proactive decisions that positively impact the manufacturing process.
Human Machine Collaboration Enhances Manufacturing
The idea behind human machine collaboration is to augment the speed and efficiency of sensor– or smart technology-enhanced automated equipment and the data it offers with the problem-solving and creative-thinking skills that are unique to the human workforce to provide unsurpassed levels of productivity, efficiency, safety and quality on the factory floor.
As a matter of fact, human machine collaboration enhances manufacturing operations in the following ways:
Increase Efficiency and Productivity | Enhance Product Quality |
Robots and other automated equipment boost productivity and efficiency simply because they are faster than manual laborers and do not fatigue. With the addition of intelligence and advanced analytics, automated equipment can also inform human operators about issues with equipment health, when the process or product quality goes off spec or if there are bottlenecks, maintenance issues or other problems that need to be addressed. Armed with this information in real time, human workers can use their problem-solving skills to ensure efficient use of assets and resources, streamline or correct the process, request a work order, minimize errors and waste and increase cycle times and throughput, which results in an optimized process with decreased downtime and vastly improved efficiency and productivity. | Combining human experience, creativity and expertise with automated equipment that provides real-time monitoring and useful data that identifies potential deviations in the process or product quality ensures the production of higher quality products. Leveraging the ability of machine vision-enhanced automated inspection equipment also boosts quality control as automated inspection systems are more likely to detect defective products than the human eye. Human workers can then use human machine interfaces to stop or correct the process to avoid further issues with quality, reducing scrap and eliminating the chance of producing an entire batch of defective products. |
Improve Safety | Maximize Flexibility |
By automating repetitive tasks or those that require heavy lifting, bending or twisting motions, facility safety will be improved. The ability of robots and automated equipment to perform flawlessly in hazardous environments reduces risks to human workers who require protective gear and other safety measures to perform operations in these areas. Further, the use of collaborative robots that are equipped with internal safety systems that prevent injuries if there is an impact with objects or human workers permit safer automated work environments and reduce the risk of accidents or injuries. | Because collaborative robots are easily reprogrammed and can be relocated to other operations where experienced human operators can train them using hand guiding and work alongside them in a variety of work cells and operations, they contribute flexibility to the manufacturing process, allowing for product variations or changing product lines |
6 Applications for Human Machine Collaboration
There are many ways in which human machine collaboration can be applied in an industrial facility or manufacturing operation – some may already be in place on your factory floor. Here, we highlight six applications for human machine collaboration.
- Warehouse Robots: One of the most well-known applications of human machine collaboration is in warehouses where collaborative pick-and-place robots utilizing autonomous mobile robot technology efficiently travel throughout the warehouse, select the correct items and bring them to human workers who then pack and label them for distribution. This increases efficiency of the process as the robots move much faster and are more likely to correctly pick items than human workers.
- Assembly Lines: Many of today’s collaborative robots can be equipped with delicate end-of-arm tooling that allows them to manipulate and assemble parts and products quickly, consistently and precisely. Because collaborative robots are equipped with safety sensors and mechanisms that allow them to work alongside humans, manual laborers can share the workspace and rely on the robots for support with aspects of the assembly process that may cause injuries, be ergonomically unfriendly or monotonous. Alternatively, manual workers may manage tasks that the robot is not programmed or properly equipped to complete or that require problem solving or creative thinking.
- Material Handling: Automated equipment and robots can lift, carry and move objects that are too heavy or cumbersome for human operators to manipulate. In many cases, smart equipment can more accurately measure, weigh and count materials that must be accurately distributed into the process, which enhances quality and reduces waste. Human operators can use their skills and experience to run and control the material handling operation without the risk of injury from lifting, twisting and bending.
- Machine Tending: Machine tending operations, including the loading and unloading of parts, are often repetitive and boring, yet also complex operations. Collaborative robots can share the machine tending cell with manual workers and perform many of the more repetitive or unergonomic tasks for human co-workers who can then use their experience and expertise to tend to other more value-added operations in the cell.
- Positioning: When parts or products need to be properly positioned, collaborative robots can manage this faster and more accurately than human workers. However, manual laborers can share space in the same work cell and complete other more value-added production tasks to increase productivity.
- Inspections: Smart automation that is equipped with machine vision can more accurately find and separate defective products from the production line. Human workers may be informed of any issues and proactively address the problem, preventing more defects or errors from occurring.
Human machine collaboration is about applying the advantages of smart automated technologies in a way that enhances the creative-thinking and problem-solving skills that are unique to humans to boost productivity and efficiency, improve product quality and optimize operations. To learn more about how collaborative robots or other automated equipment can successfully collaborate with your existing workforce, please reach out to the experts at JHFOSTER.