How IOT and Industry 4.0 Boost Compressed Air Systems
In factories, processing plants and elsewhere, if compressed air stops flowing everything stops. Actuators and pneumatic tools won’t work, conveyors don’t move powder, sprayers can’t apply coatings and so on. That puts the person responsible for the compressed air system at the center of the action, which is usually not much fun.
The IOT and Industry 4.0 should help. They should also help lower energy costs and manage maintenance more effectively. Here’s their relevance to air compressor installation.
Understanding the IOT and Industry 4.0
The IOT is about deploying “smart” sensors that can communicate the data they’re collecting. At home there are “smart” thermostats and doorbells. In the factory, “smart” flow meters and temperature sensors measure and report. There are also “smart” actuators and controls that take action in response to signals or requests. “How the Industrial Internet of Things Enhances Compressed Air Systems,” provides an overview.
Industry 4.0, which is shorthand for the fourth Industrial Revolution, adds advanced analysis tools that make sense of the data being gathered. These tools run on small computers on the devices being monitored, on desktop PC’s, and for massive computing power they use servers “in the cloud.”
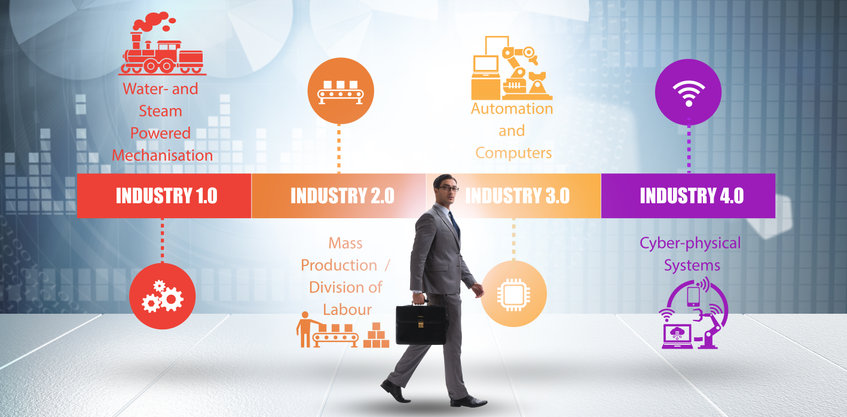
The Challenge of Managing Compressed Air Systems
Producing and distributing compressed air is complicated. Many things can change on both the input and demand side. Ambient air temperature and humidity can vary throughout the day. Dust and pollen can affect filtration efficiency. Even the voltage supplied can fluctuate between limits.
Air consumption is rarely constant either. Demand rises and falls with changes in production schedules. Staffing levels influence which equipment runs. Breaks, shift changeovers and other stoppages can cause sudden drops in demand.
In addition, compressed air equipment needs frequent inspection and regular maintenance. Drain traps must be emptied, filters changed and belts replaced. Skip any of these and the likelihood of breakdowns increases dramatically.
To address these challenges, in recent years new air compressor installations have gained a lot of instrumentation. Pressure, flow, dew points, electrical power, dryer operation and drain traps are just some of the parameters being measured or examples of equipment being monitored.
This improves reliability and availability. Warnings signal when attention is needed and compressors can shut off before any damage occurs. Variable frequency drives improve compressor efficiency and flow metering identifies leaks and other problems. In fact it’s fair to say the modern compressed air system is more reliable and efficient than it’s even been. So what can the IOT and Industry 4.0 contribute?
Applying the IOT and Industry 4.0 to Your Air Compressor Installation
There are benefits in four areas:
- Remote monitoring and control
- Data capture
- Predictive maintenance
- Optimized energy consumption
Once compressed air system information is available over the internet those responsible for running the system no longer have to be on site. They can receive alerts by text or email, log in on a tablet or laptop to see what’s happening, and send commands through the same interface.
Improvement starts with measurement, but historically users have had very little information about how their compressed air systems are running. IOT devices can create comprehensive histories on every aspect of system operation, from pressure drops across filters to motor temperatures. It’s data like this that’s key to effective decision-making.
Predictive maintenance replaces scheduled maintenance, which may include doing the wrong things, or doing things more often than needed, with a kind of “as required” maintenance. In predictive maintenance, software monitors the age, running hours and condition of every component in the system. When changes are detected, trends are reviewed to determine when replacement or overhaul is needed. This way, rather than scheduling shutdowns and still reacting to breakdowns, work is planned to minimize costs and production impacts.
The fourth area of benefits is optimized energy consumption. When demand for compressed air is constant it’s relatively straightforward to minimize energy consumption. In situations of fluctuating demand this becomes much harder, but it’s a good task for a “smart” controller.
Combining knowledge of historical patterns with information on immediate demand, a “smart” compressed air system controller can make decisions about whether to store air in a receiver or turn on or off or throttle back air compressors. (Humans could make these decisions too, but not at the same speed as an automated system, and it would be a full time job.) The result is truly optimized energy efficiency.
Take the Load Off
Even when compressors are running smoothly and every user is getting the air they need, there’s still pressure to do better. Energy costs are always too high and too much is being spent on maintenance.
Applying IOT and Industry 4.0 technologies to your air compressor installation helps meet these challenges. More data plus better analysis capabilities leads to faster and better decision-making. It’s how industry leaders are improving compressed air availability and quality while spending less on maintenance and lowering their energy bills. If this sounds interesting, talk to JHFOSTER. We’ll explain what’s available to help and what you need to do.