How Robotics Can Assist the 3D Printing Revolution
3D printing, also called additive manufacturing, is a method of creating an object, product or part by adding layers of material, which differs from traditional manufacturing techniques that take away material through grinding, drilling, machining or casting in a mold. More manufacturers are exploring the use of 3D printing for prototyping and small-scale production because it provides considerable advantages. And, using robotic technologies for tending the 3D printing process can make a good thing even better.
The 3D Printing Revolution
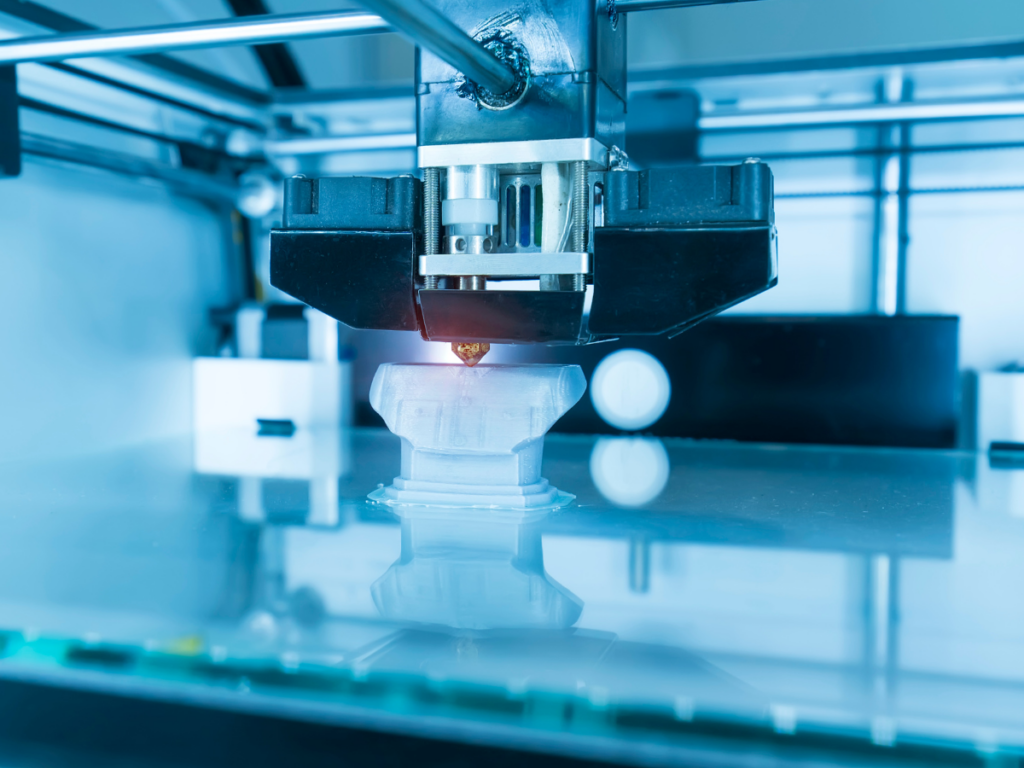
Though it has been around since the 1980s, 3D printing is currently growing in popularity because it quickly fabricates high-quality, detailed parts that, when produced on a smaller scale, are cost effective. The process of 3D printing isn’t complex. It begins with a digital 3D model or Computer Aided Design (CAD) model of the object, which is “sliced” into multiple layers. The 3D printer interprets the sliced model as instructions for creating the object.
Materials such as plastic or metal are deposited layer-by-layer until the final object is formed. This process can take as little as a few minutes to build a small part or several hours for larger objects.
In comparison, traditional manufacturing processes are subtractive in that they produce objects by removing material from a block of raw material using costly, time consuming techniques such as drilling, grinding and machining. This process is usually cost effective when mass manufacturing parts and objects, but can become cost prohibitive when prototyping parts or for small-scale production runs.
As today’s manufacturers realize that speed to market can make or break a new product and that customization and changing consumer demands are leading to increasingly smaller and frequently changing production runs, 3D printing is becoming a fast-growing segment of the manufacturing industry as it provides significant time and cost advantages for prototyping parts and small-scale manufacturing.
3D Printing Speeds Up Prototyping and Small Batch Production
Product prototyping is a stage in product development when engineers design and test multiple iterations of the object they want to produce and make any adjustments before actual production begins. During the prototyping stage, speed is generally of the essence as the faster a product can get into production and hit the market, the better, and 3D printing provides the necessary agility, making it an attractive option for today’s product designers. Compared to traditional manufacturing, where prototyping can take weeks or months, 3D printing can produce a simple prototype in hours or a more complex one in just a few days because it eliminates the time spent tooling equipment or making molds for each prototype as is necessary with traditional manufacturing methods during product prototyping.
As mentioned earlier, traditional subtractive manufacturing methods are well suited for mass production, but small-scale production has been a challenge because setting it up is labor intensive and requires costly equipment. But, as some segments of the manufacturing industry are moving toward customization and frequently changing products, small-scale production is a growing trend and is being supported by the speed and cost effectiveness of 3D printing.
As 3D printing does not require tooling or molds, it eliminates the need for multiple steps in the production process, making it faster, more accessible and more affordable for small production runs, while also allowing products to get to market faster.
Robots Further Enhance 3D Printing Efficiency
Although more manufacturers have adopted 3D printing for its speed and productivity, there are still some hurdles, such as the need to further increase efficiency and quality and robotic technologies can help. Especially Collaborative robots due to their ease of programming and built in safety features.
Manufacturers are beginning to integrate machine tending robots with 3D printing to automate the loading and unloading tasks. Robots can be programmed to automatically dispense raw materials into the 3D printer if they are equipped with end of arm tooling designed to dispense the metals or plastics that will be used to create the products. Automated technologies are not only faster and more efficient at performing this task, but their accuracy, precision and repeatability reduce waste and enhance product quality because only the exact amount of material is dispensed each and every time. Employing robots in this capacity is especially helpful when 3D printing is used to create large structures as material dispensing can be time consuming in these applications and must otherwise be supervised by human operators.
Another way robots can be integrated into the 3D printing process is to program them to remove finished parts post production. Machine tending robots can help reduce bottlenecks at the end of the process because they consolidate the workflow steps associated with 3D printing, further enhancing efficiency of the process. Robots can also be used to place new build plates so that the process can continue without using manual labor, increasing efficiency, saving on labor hours and encouraging “lights out” manufacturing. Robots may also perform pick and place and finishing tasks such as washing, curing, sanding or removing “flash” from the finished parts to create higher quality products in a more efficient way.
Applying automation can help manufacturers further enhance the efficiency and quality provided by 3D printing since robots are capable of operating at faster speeds with greater precision and consistency than manual machine tending. To learn more about how robots can make a positive impact on the 3D printing process, please contact JHFOSTER.