Air Dryers: The Secret Weapon of the Compressed Air System
Air dryers are essential to removing moisture and humidity – byproducts of the air compression process – from the treated air. By doing so, they safeguard the compressed air system, pneumatically operated equipment and even finished products against contamination and corrosion, making air dryers the secret weapon of industrial facilities that rely on air compressors to power pneumatic machinery and tools. Because air dryers are indispensable to protecting equipment and product quality, the choice of dryer is a crucial one. This blog will discuss common air dryer technologies, as well as typical applications for each type.
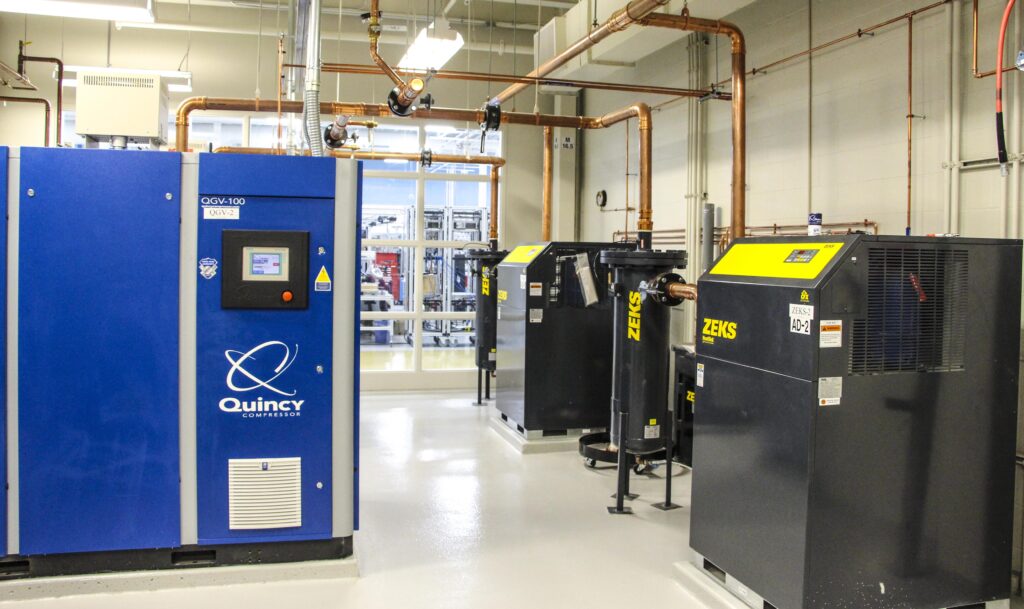
The Importance of Air Dryers
Since air compressors are compressing ambient, humid air while increasing its temperature during the process the compressed air becomes saturated with moisture.
While many air compressors offer basic integrated drying mechanisms, such as aftercoolers water separators and drains, these don’t effectively remove all the moisture that results from the air compression process, especially in operations located in very warm, humid climates. As a result a dryer will be necessary to protect the distribution piping, machines, tools and equipment used in manufacturing operations. Especially facilities that require the driest possible air, such as medical device, food processing, pharmaceutical, powder, cosmetics, electronics and painting applications.
In any industry, excessive moisture in compressed air can lead to:
Equipment Failures: Contaminants caused by moisture in the system can lead to extra maintenance requirements or premature failure of air compression system components and connected manufacturing equipment.
Poor Quality Products: Moisture and associated contamination from within the air compression system can be transferred to products as they are manufactured, which can severely alter the quality of finished goods. This is especially harmful in industries that must meet strict purity standards, such as food and beverage, medical devices, pharmaceuticals and electronics manufacturing.
Rust & Corrosion: Air compression system components and the associated production machinery and tools can corrode due to too much moisture in the system.
Compromised Control: Because pneumatic tools rely on the efficient passage of air throughout the system, rust, corrosion and contamination can cause blockages that negatively impact the operation and efficiency of pneumatic tools and equipment.
3 Common Air Dryer Types
Incorporating an air dryer into an air compressor system is essential to avoiding maintenance and product quality issues that result from the corrosion and contamination associated with moisture. Becoming knowledgeable about the different types of air dryers is fundamental to ensuring that the selected technology is the best option for an application. Here, we outline the most common types of industrial air dryers.
- Refrigerated Air Dryers: TThe most popular air dryer option, refrigerated dryers cool the compressed air using a heat exchanger, a refrigerant circuit and a compressor. Warm, saturated, incoming compressed air is chilled, which causes the moisture to condense and collect in a separator until it is drained out, then in most refrigerated dryers the chilled, dry, outgoing compressed air is reheated utilizing another heat exchanger used to pre-cool the warm incoming air from the compressor. Refrigerated air dryers are extremely energy efficient and shine in general manufacturing and auto shop type applications.
- Regenerative Dryers: This type of dryer commonly offers two “towers” filled with absorbent material called desiccant, a material that attracts moisture from the compressed air. The dryer cycles between the towers during operation, allowing the desiccant in the off-line saturated tower to regenerate and purge moisture while the other tower removes moisture providing very dry compressed air to the plant. Activated alumina desiccant is typically used but others are available. These types of dryers require little maintenance and can provide a very low dew point. Desiccant dryers are ideal when compressed air is needed in low-temperature environments and applications that demand the cleanest, driest air, such as medical, pharmaceutical, food & beverage processing and electronics production.
- Membrane Dryers: Using selective permeation and a multi-stage filtration system, membrane dryers are very effective at separating moisture from the compressed air. Following the initial separation, the membrane removes water vapor, resulting in clean, dry treated air at varying dew points depending on the dryer and application. They are compact and require almost no maintenance; however, regular inspections are necessary to ensure that there is no damage, fouling or clogging in the membrane. Membrane dryers can be used anywhere refrigerant and desiccant dryers are used, but are most often found in food and beverage processing, pharmaceutical production, chemical and petrochemical manufacturing and the healthcare industry.
Additional Precautions
In addition to selecting the most appropriate air dryer, there are a few additional precautions that must be taken to reduce moisture content so the air dryer doesn’t have to work as hard and to further ensure equipment health and product integrity.
Ensure System Drainage: Air compression systems, moisture separators, tanks, filters and refrigerated dryers contain drains where excess moisture and water content collect for removal. Draining units should be emptied frequently and inspected regularly to ensure functionality – drains that don’t open will result in condensate contamination in the system and drains that don’t close will reduce energy efficiency of the system.
Use an Air Filtration System: A moisture separator and air filtration system removes liquids, moisture, particles and pollutants from the compressed air. In most applications, filtration is required before and after the dryer and correct installation is critical. Filters should be inspected, cleaned and elements replaced on a regular basis to ensure optimized operation and energy efficiency.
Clean, dry air is essential to the healthy and efficient operation of the air compressor system, the equipment it powers and the quality of the finished product. Experts at JHFOSTER can help you select the most appropriate air dryer for your application so your compressed air system and products remain free from damaging moisture and contaminants.