Achieving ISO 8573-1 Compliance for Compressed Air Quality
Compressed air is a staple in industry and is used for everything from powering air-operated tools and equipment to processing and packaging food and other products. While many facilities are concerned about the energy efficiency and performance of their compressed air system as it directly impacts the bottom line and productivity of the plant, compressed air quality is often overlooked.
Unfortunately, contaminants, such as water, oil and solid particles, can inadvertently enter the compressed air stream and cause a host of issues from equipment damage to diminished product quality, so paying attention to compressed air quality — especially in industries like food processing, pharmaceutical production and medical device manufacturing – is crucial. Compliance with ISO 8573-1 ensures the generation of high-quality compressed air, helping your facility avoid problems such as contaminated product and unplanned downtime that can result from oil, water and particulate contamination in treated air.
This blog will explain ISO 8753, as well as how properly selected equipment and regular monitoring can help manufacturers reach and maintain compliance with the standard in order to achieve the highest quality compressed air.
ISO 8573-1 Explained
The International Standards Organization (ISO) established standard 8573 for compressed air quality to assist with compressed air system component selection, design and testing to ensure that adequate compressed air quality is achieved for certain types of applications.
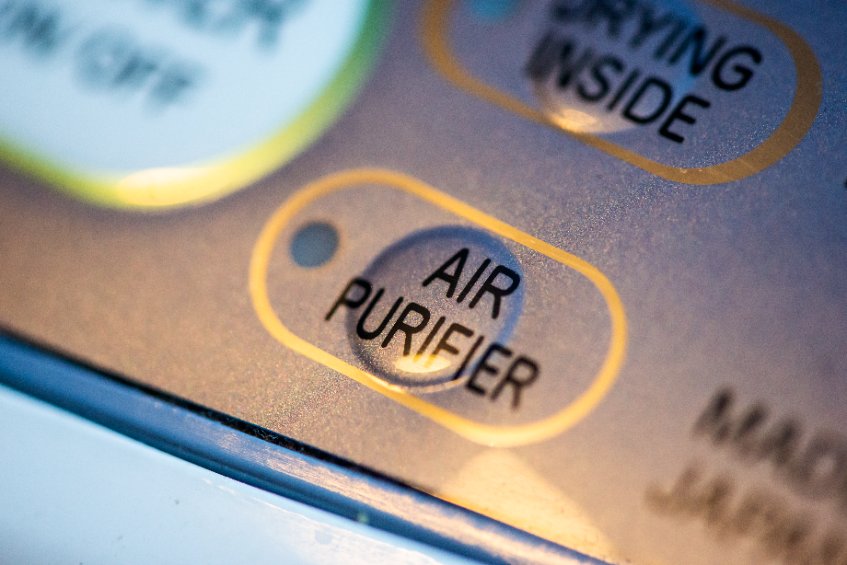
The multi-part standard consists of nine parts, with Part 1 classifying contaminant type, including solid particulate, water and oil, and establishing air quality levels, or classes, for each contaminant type for certain industries, including general manufacturing, food and beverage production, medical device manufacturing and others. Parts 2 through 9 of the 8573 standard outline testing methods for measuring contaminants.
Under ISO 8573, the three major contaminants, solid particles, water and oil, are categorized by compressed air purity classes. Further, the compressed air purity classes group the concentrations of each of the contaminants into ranges, with each range given its own purity class index. According to the Air Quality Classes Chart, available within ISO 8573, Class 1 measures solid particles, by micron size. Class 2 measures the maximum allowable amount of water in liquid and vapor form. Class 3 measures the total permissible oil content, including aerosol, liquid and vapor.
According to the standard, certain industries must meet specific compressed air quality levels. When specifying the air purity requirement for an industry, the standard (ISO 8573-1:2010) is referenced first, followed by the purity class for each contaminant: solid particulate, water and total oil (always in that order).
For example, general industry falls under ISO 8573-1: 2010 Class 1.4.2. The three digits following the standard refer to the purity classifications needed for solid particulate, water and total oil, precisely in that order. So, selecting an air purity class of 1.4.2 for general industry means:
- Class 1 air levels are needed for particulate. Therefore, in each cubic meter of compressed air, the particulate count should not exceed 20,000 particles in the 0.1-to-0.5-micron size range, 400 particles in the 0.5-to-1 micron size range and 10 particles in the 1-to-5 micron size range.
- Class 4 levels are needed for water, meaning a pressure dewpoint of 37.4°F or better is required and no water or liquid vapor is allowed.
- Class 2 levels are required for oil, meaning in each cubic meter of compressed air, not more than a total of 0.1 mg of oil, including liquid, aerosol and vapor, is permitted.
Industries such as food and beverage processing where compressed air will contact products for consumption have tougher guidelines and fall under ISO 8573-1:2010 Class 1.2.1, meaning:
- Class 1 air levels are needed for particulate. Therefore, in each cubic meter of compressed air, the particulate count should not exceed 20,000 particles in the 0.1-to-0.5-micron size range, 400 particles in the 0.5-to-1 micron size range and 10 particles in the 1-to-5 micron size range.
- Class 2 levels for water must achieve a pressure dewpoint of -40°F or better and no liquid water is allowed.
- Class 1 levels for oil means that food and beverage processors must maintain levels of no more than a total of 0.01 mg of liquid oil, oil aerosol and oil vapor.
Class 0 applies to industries such as medical device manufacturing. This does not mean zero contamination, rather Class 0 requires the user and the equipment manufacturer to agree to contamination levels as part of a written specification. Those levels should be within the measurement capabilities of the test equipment and testing methods discussed in Parts 2 through 9 of the standard.
Meeting ISO 8573-1 purity class for a particular industry or application requires the use of a testing method, as specified in Parts 2-9 of the standard. Testing includes point testing for solid particulate, dew point/water and oil using a variety of testing methodologies and analysis.
Compressed air quality testing must be conducted to establish that the compressed air user is achieving the compressed air quality levels that are required by ISO 8573-1 for the application.
Choosing the Right Equipment to Achieve ISO 8573-1
Employing certain types of equipment, such as the correct type of air compressor, air dryer and filter, can help ensure that a facility and/or application achieves and maintains the proper purity class as determined by ISO 8573.
Industries such as food processing, pharmaceutical production, medical device manufacturing and others that need to achieve Class 0 or Class 1 air for oils should consider the installation of an oil-free air compressor that does not require oil for lubrication.
Air dryers are available in a variety of styles and sizes and can help achieve even the most stringent compressed air quality classifications for dew point/water contaminants. When selecting an air dryer for the system, ensure that it is properly sized, as air dryers consume a lot of electricity and over-drying the air will be costly in the long run. Meanwhile, if the dryer is undersized, it will be difficult to achieve and maintain the proper classification for dew point/water.
Finally, filters should be used to remove both oils and solid particles from the compressed air. However, to ensure that the correct classification for oils and particulates is maintained, filters must be inspected, cleaned and replaced regularly or the compressed air quality will decline over time.
Monitoring Helps Maintain ISO 8573 Compressed Air Quality Levels
While proper selection of the air compression system components is the best way to achieve the necessary compressed air quality class for the application, regular compressed air quality testing and monitoring is the only way to ensure that the system maintains that compressed air quality level.
A solid compressed air quality monitoring program involves:
Documentation of the compressed air system and its components, such as compressor type, dryer and filtration systems for oil, water and particulate. The manufacturer, model and part number for each component, as well as other relevant documentation, should be recorded. |
Documentation of maintenance activities should be kept to provide a historical view of filter changes, compressor repairs and preventive maintenance activities, dryer installation and piping additions or changes. |
Air quality testing for particles, dew point/water and oil, using the appropriate methods as explained in ISO 8573-1 Parts 2-9, should be conducted on a regular basis to ensure that air quality is being maintained at the proper level for the industry and application. Testing and sampling should be conducted at various points of use several times throughout the year to achieve an accurate representation of the true quality of the compressed air. A variety of air testing kits and laboratory services are available to assist with this essential activity. |
Documentation of air quality testing and the results for particles, water and oil should be recorded and used for trend analysis and reporting. |
Because high-quality compressed air is essential to maintaining product purity specifications and preventing equipment failure, ISO 8573-1 should be well understood and air quality classification levels should be achieved through the use of properly selected air compression system components. Appropriate testing and monitoring activities should also occur on a regular basis to ensure that the compressed air quality levels are being maintained. To learn more about these critical steps to achieving and maintaining ISO 8573-1 compliance, please contact JHFOSTER today.