7 Considerations for Choosing the Best Robot End of Arm Tooling
Automating with robots and cobots can greatly increase the efficiency of a manufacturing operation. And, when properly chosen, the right robot grippers or tooling can further improve the performance of automated systems because outfitting a robot with the most appropriate end of arm tooling (EOAT) allows for a more precise robotic grip and enables more accurate and careful handling and manipulation of components.
Here, we will take a deep dive into the available types of robot tooling, as well as key selection criteria to ensure that you are choosing the end of arm tooling that best matches the requirements of the application.
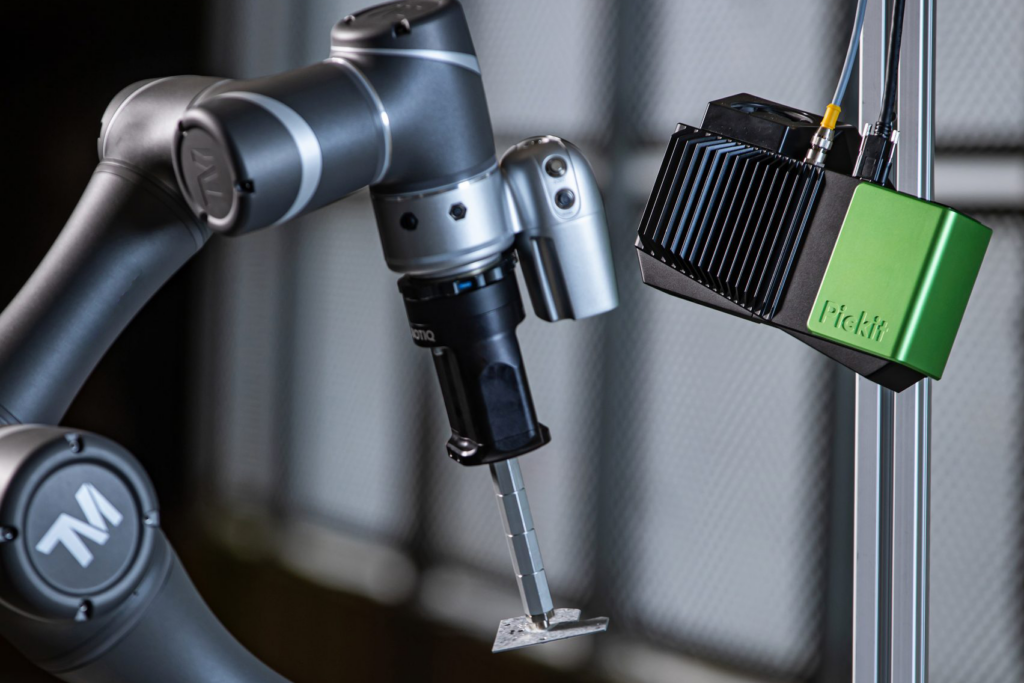
What is End of Arm Tooling?
End of arm tooling, or EOAT, devices are placed at the end of an industrial or collaborative robot arm, allowing it to grip, handle and manipulate components, parts and products during automated manufacturing processes.
Selecting the right type of robot tooling increases the efficiency of a process by allowing precise and accurate movement of components and increasing the flexibility of the robot so it may pick up and manipulate objects without damage.
Robot end of arm tooling can be used to complete and streamline tasks such as:
- Assembly
- Pick and place
- Machine tending
- Application of sealants and adhesives
- Welding
- Palletizing and depalletizing
- Laser cutting
- Inspection/quality control
For many tasks, robot grippers are the go-to type of EOAT because they are an effective way for a robot to pick up, manipulate and/or move or transport parts and components with precision and accuracy.
However, there are many different types of EOAT to suit a variety of applications, including:
Grippers | pick up, manipulate and transport objects on production lines. |
Magnets | use magnetic force to locate, pick up and move ferrous materials. |
Vacuum heads | lift and move non-porous surfaces and heavy parts and are often used in high-speed applications. |
Electrodes | precisely and efficiently manage spot welding of metal objects or components. |
Process tools | such as cutting tools, drills, brushes, screwdrivers, adhesive dispensers and paint spray guns, can be selected to match the specific process. |
Force-torque sensors | allow robots to handle delicate products without damage. |
Material removal tools | remove excess material from manufactured products. |
Lights and cameras | can be incorporated with EOAT to perform quality control and inspection activities and may be used to verify barcodes or identify colors or shapes. |
Sensors | can be combined with other tooling to detect changes in pressure, temperature, or other process conditions, for inspection processes or for safety compliance. |
Combinations of robot tooling | are also available so that robots may perform multiple duties such as picking up and inspecting products. |
Customized robot EOAT | is also an option when off-the-shelf robot grippers or tooling will not effectively manage the requirements of a task. |
7 Considerations for Selecting the Best End of Arm Tooling for a Robotic Application
While robot selection is often the focus of manufacturing automation projects, careful consideration of robot EOAT is equally important.
Proper selection of EOAT grippers and tooling will optimize robot performance and the entire manufacturing process by accelerating cycle times, improving product quality and maximizing safety and efficiency. Conversely, picking unsuitable end of arm tooling can slow down the process, cause product damage and/or require frequent human intervention.
To ensure that the end of arm tooling is the best match for the process, consider the following:
- The application: Consider the application requirements and specifications including the tasks the robot will be performing, such as picking, placing, assembling, palletizing, welding, painting, etc. It’s also important to ensure that robot tooling is compatible with the materials it will encounter. Other critical considerations include the required level of precision and accuracy, as well as any special needs of the application such as cleanroom designs or whether the EOAT will be exposed to harsh cleaning regimes found in the food processing industry.
- Part type and size: Determine whether the robot tooling will handle single item types or mixed items, for instance all objects of the same size or items of various sizes, shapes and orientations. If the objects are similar in size, weight, and material, a single EOAT device will suffice, but mixed items may require a gripper that is intended to vary its speed or gripping force.
- Weight and load capacity: Ensuring that the EOAT grippers or tooling can handle the weight of the components being manipulated, and the weight of the tooling itself, is essential to project success. Also, make sure that the combined weight of the robot tooling and the part it will handle does not exceed the payload capacity of the robot itself.
- Production environment: If there are extreme temperatures, humidity or exposure to chemicals or other caustic substances during the process or cleaning-in-place practices, be sure the robot and the robot end of arm tooling can safely operate in the location. Also, it is important to ensure that the robot and tooling meet all hygiene or safety standards of the application.
- Safety: If the end of arm tooling will be used on a collaborative robot that operates in close proximity to human workers, safety features may be needed for the robot and EOAT to ensure regulatory compliance.
- Durability: Robot end of arm tooling is often exposed to harsh industrial conditions and heavy-duty work, so be sure the EOAT is made from high-quality materials and is well constructed so that it withstands the environment, payload and tasks while remaining reliable and effective for years of operation.
- Compatibility with the robot: If the robot tooling is not compatible with the robot’s mounting interface or control system, it will not work properly, so it is critical during the selection process to verify this with the supplier.
The application specifications, as well as factors like payload capacity, workplace conditions, safety regulations and special requirements should guide the EOAT selection process to ensure that the best end of arm tooling is chosen for the application. The most appropriate robot tooling will streamline the process, boost efficiency and enhance product quality. For assistance with selecting robot EOAT or to inquire about customizing robot grippers or other tooling, please contact the automation experts at JHFOSTER, a Tavoron company.