Automated Inspection Systems Reliably Catch Packaging Defects
In the highly competitive packaging industry, damaged or defective packages can be a major drain on a packager’s profits and can result in lost customers. While there are any number of potential packaging defects, today’s automated inspection systems can help identify and prevent these problems, helping to ensure an error-free and more profitable packaging operation.
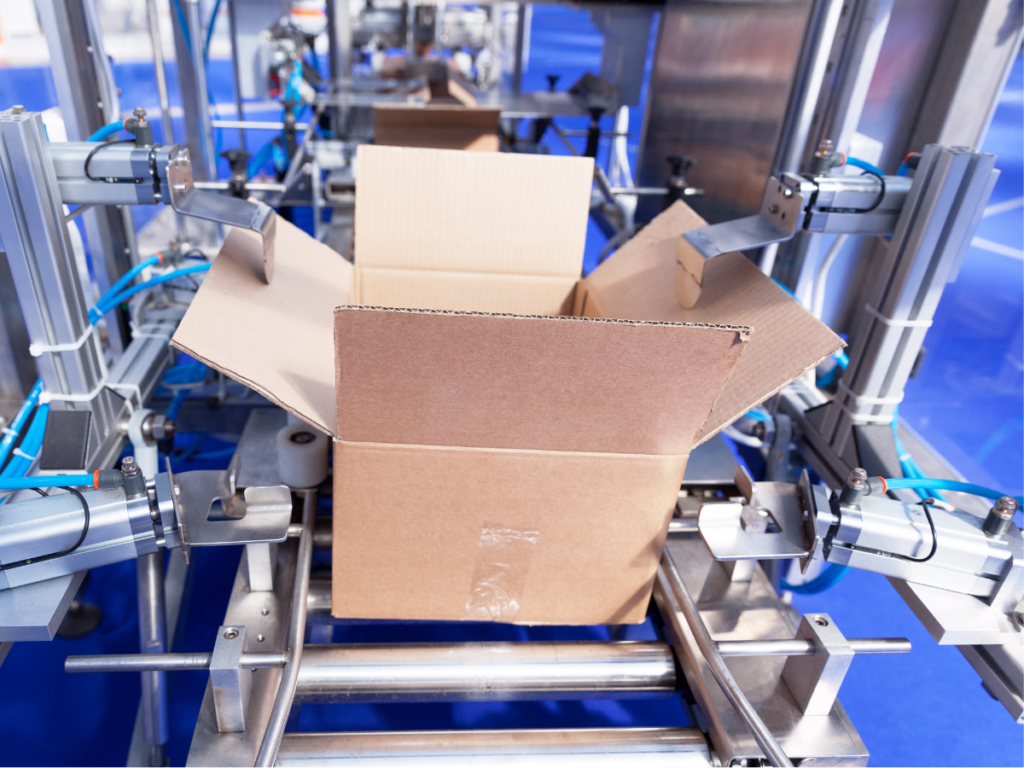
The Importance of Defect-Free Packaging
The rising demand for quality from consumers has led manufacturers to become increasingly quality conscious regarding their products and the associated packaging. This is especially true in the food, pharmaceutical and healthcare product space where ensuring the safety and integrity of goods is essential and strictly regulated regarding proper labeling and the prevention of contamination and tampering.
Packaging defects can not only turn consumers away from a product or brand, but damaged or mis-labeled products result in waste and rework or, worse, product recalls – a costly and reputation-damaging endeavor for the manufacturer and packager. For these reasons, there is mounting pressure to provide quality assurance, safety and regulatory compliance throughout the packaging process.
Traditionally, manual inspections were employed to help catch packaging defects, including broken seals, torn packaging, evidence of contamination, mislabeled products, incorrect barcodes and printing errors, but manual inspections are slow and defects often go unnoticed. Fortunately, the development of automated inspection systems can help packaging operations avoid these common, but costly problems with greater efficiency and accuracy.
Common Packaging Defects
Depending on the product being packaged, there could be any number of defects, such as:
- Smeared printing or other printing errors
- Torn, punctured or otherwise damaged packaging
- Incorrect assortments of products or missing components
- Use of the wrong packing materials
- Mislabeled products
- Incorrect or missing barcodes
These and other packaging defects are classified according to the severity of how they impact the ability to sell the product, as follows:
Critical Defects result in packaging and products that are unsafe for the user. There is zero tolerance for packaging with critical defects and these will be returned for rework or recalled if the errors are not caught before hitting the store shelves. Examples might include mislabeled medications or food products with pest infestations
Major Defects impact the product’s performance or appearance and will likely result in rework. Examples include torn or damaged packaging, incorrect labeling, missing components or incorrect assortments.
Minor Defects include anything that does not meet specifications, such as scratches on the package, smeared ink or incorrectly aligned labels.
How Vision Inspection Systems Prevent Packaging Defects
Today’s automated packaging vision systems feature cameras, sensors and analytic software to identify product or defects, inconsistencies and mistakes in packaging, labels, barcodes and assortments. Automated vision inspection systems work as follows:
As each product or package moves along the packaging line, sensors detect its presence and signal a camera to capture high-resolution images of each item as it passes.
The images are sent to a software system, which extracts relevant data and information and compares captured images with pre-programmed quality specifications. Analytics allow irregularities, defects, damage or other inconsistencies, such as missing labels, misprints, missing components, damaged packages and incorrect assortments, to be identified.
If a defect or inconsistency is verified, the inspection system triggers an automated sorting system that separates the defective package so it does not continue along the line with the products that do meet quality specifications. Alerts may be sent to inform operators that there are defects so they may proactively manage the issue, preventing further quality issues and ensuring that quality standards are upheld.
The Advantages of Automated Inspection Systems
Automated inspection systems offer many advantages when compared to manual inspections, which rely on human workers who may grow tired or bored and miss defects. The benefits of using an automated inspection system include:
- Greater Efficiency: Automated inspection systems inspect packages at high speeds, which increases throughput, decreases bottlenecks and reduces labor costs.
- Greater Accuracy: Because manual inspections rely on employees, they are prone to human error, which results in inconsistencies in quality and unidentified defects. Meanwhile automated systems are programmed to detect defects and do so reliably, precisely and without fatigue. Because they are capable of recognizing even the smallest flaw, the chance of a faulty package reaching consumers is minimized.
- Greater Flexibility: Automated inspection systems are easily re-programmed to manage the inspection of a variety of products, packages, packaging formats and assortments, which means they can be adapted to various lines and packaging configurations.
- Cost Savings: In addition to reducing labor costs for manual inspections, the use of automated inspection systems often results in decreased waste and rework, which is a significant cost savings for packaging operations. In addition, the high-speed inspection increases throughput for the packaging line, allowing more product to move through the facility, boosting profitability. And, finally, because packages are inspected with higher levels of accuracy and consistency, the occurrences of expensive rework, refunds and product recalls are greatly minimized.
Automated inspection systems not only provide packaging operations with assurance that packages will meet the highest quality standards, but also help maintain customer satisfaction and ensure that the operation is profitable. Representatives from JHFOSTER can provide additional information about automated inspection systems and how they can efficiently and accurately identify and prevent defects in the packaging process.