Understanding Air Compressor Duty Cycle Optimizes Performance
Duty cycle is a term that may come up when sizing an industrial air compressor. Although there is no standard definition used by air compressor manufacturers to rate air compressor duty cycle, understanding a unit’s duty cycle can go a long way toward ensuring that the compressor offers the correct size and performance for the application while also preventing premature failure of this essential piece of equipment.
This blog will explain duty cycle, discuss the ways in which duty cycle impacts performance and reliability and help users calculate their air compressor duty cycle requirements so that the most suitable industrial air compressor is selected.
Duty Cycle Meaning
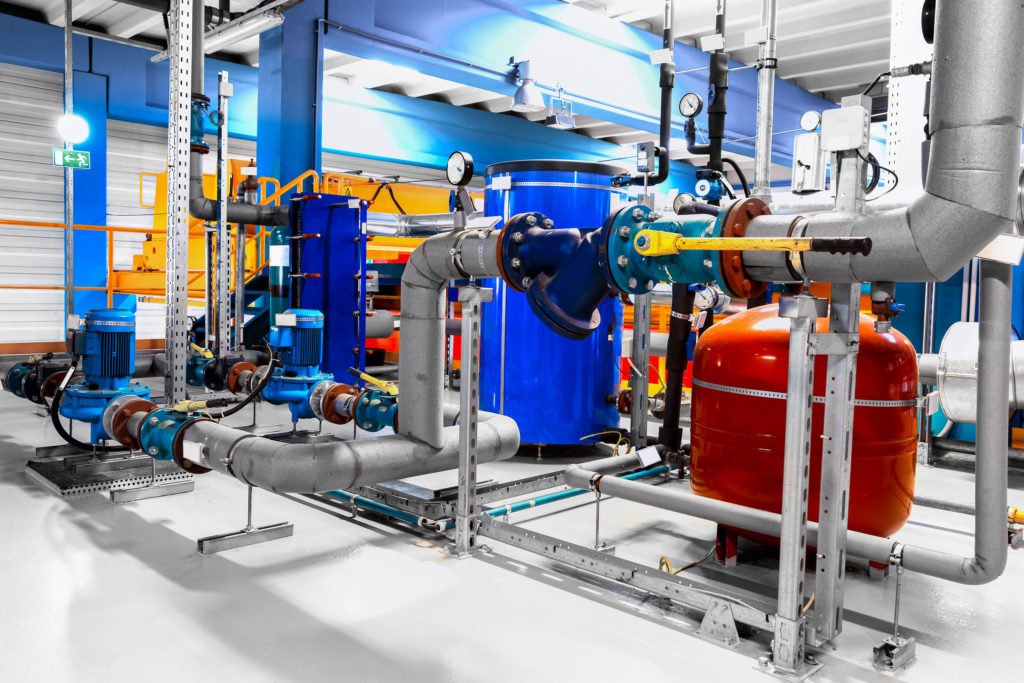
The simplest way to describe duty cycle is that it is the amount of time an air compressor spends making air compared to the amount of time that the unit must rest, meaning that an air compressor duty cycle is the amount of time the unit will deliver pressurized air within the total cycle time. Duty cycle is also sometimes referred to as load/unload time or run/rest time.
A more technically accurate way to define duty cycle is that it is the amount of time a compressor is able to provide consistent pressure (PSI) and flow (CFM) during a complete cycle. A complete cycle includes both running and resting time.
Air compressor duty cycle is often expressed as a percentage and, when presented as such, the duty cycle rating describes what percentage of the complete cycle the unit will be producing air at the PSI and CFM for which it is rated.
So, for example, a compressor that offers a 100% duty cycle at 25 CFM and 125 PSI will provide 25 CFM and 125 PSI 100% of the time. A compressor rated for 25 CFM and 125 PSI and a 50% duty cycle would provide consistent pressure and flow for half of its cycle (this means it will make air for half the total cycle time – for example 5 minutes of rest will be needed for every 5 minutes of active run time during a 10-minute cycle).
The Importance of Understanding Air Compressor Duty Cycle
As you can see by this example, although both compressors offer the same CFM and PSI ratings, one is a continuous run air compressor, meaning that it will deliver pressurized air for the duration of its cycle time, while the other will deliver pressurized air intermittently during a cycle, which has a significant impact on the way the unit will function in an application. This makes duty cycle a crucial consideration when sizing and selecting an industrial air compressor as it is critical to ensuring that the unit performs as required for the application.
For small shops that use tools periodically throughout the day, an intermittent air compressor – or one with a lower duty cycle – will likely provide an adequate performance. However, facilities that require a continuous supply of air, such as industrial facilities that power conveyors or manufacturing equipment via an industrial air compressor, will need a continuous run air compressor that offers a 100% duty cycle.
Choosing a unit with too low a duty cycle rating means it will wear out quickly, even if it meets the CFM and PSI requirements for the equipment it will run.
This is because compressors are designed for specific applications. For example, a 15hp splash lubricated reciprocating compressor with a 50% duty cycle rating will wear out very quickly if it has to run 100% of the time to maintain required flow and pressure, where an equivalent rotary screw compressor with a 100% duty cycle rating can run continuously with no ill affect.
Calculating Air Compressor Duty Cycle
Now that the importance of duty cycle is understood, we can next provide a way to calculate the duty cycle requirements for an industrial air compressor.
Start the process by determining the facility’s air demand requirements by logging the current tool usage per day during both average and peak demand times and taking note whether that usage is constant or intermittent.
And then use a duty cycle calculator or the general formula, shown below, to determine whether a compressor’s duty cycle will meet the needs of the facility.
Compressor time on/(compressor run time + rest time) = duty cycle percentage.
So, for an air compressor with a total cycle time of 10 minutes that must run for 5 minutes and rest for 5 minutes, the calculation would be as follows:
5 minutes/(5 minutes + 5 minutes) = 50% duty cycle.
Understanding duty cycle meaning and how to calculate duty cycle will help determine whether the application requires an intermittent or continuous run air compressor and ensure that the selected unit will deliver enough air without experiencing compressor short cycles, which are detrimental to the performance, efficiency and reliability of industrial air compressors. For help using a duty cycle calculator, determining if a compressor will meet your application’s duty cycle requirements or whether a continuous run air compressor or intermittent unit is most suitable, please contact the experts at JHFOSTER, a Tavoron Company.