Decoding Air Compressor CFM Calculations
An air compressor serves as the heart of most industrial facilities as it converts electricity into pressurized air that powers the pneumatic tools and equipment used for production. For this reason, it’s essential to understand the key specifications when selecting or operating an air compressor and one of the most misunderstood performance indicators is the CFM value. This blog will help decode CFM calculations and explain their significance to air compressor performance.
What is CFM and Why Does it Matter?
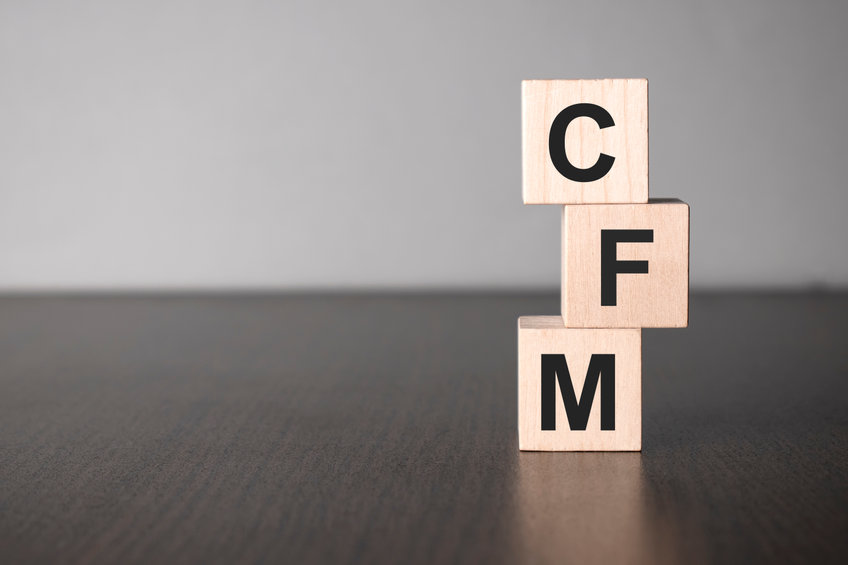
Positive displacement air compressors are rated according to the inlet volume of air they compress. Most manufacturers call this number CFM, but ACFM, ICFM and FAD are also commonly used. CFM values are determined by several factors, including the size of the compressor, the size of the motor and the design of the compressor.
The higher the CFM rating of the compressor, the more powerful it will be, so when selecting an air compressor, many people mistakenly assume that the higher the CFM value, the better the compressor. However, this is not necessarily true as the best compressor is the one that delivers the CFM that is appropriate for your facility.
If the CFM is too high, it will use more energy than is necessary, driving up electric bills. Conversely, choosing an air compressor with a CFM value that is too low also has negative consequences. If the CFM is insufficient, the compressor will not provide enough air to the tools to which it is connected, which will result in poor equipment performance. Additionally, if the CFM is too low, the air compressor will have to work harder to provide the air, which can result in premature wear and tear or overheating, causing damage to the compressor motor or other components.
How to Determine CFM for Your Facility
To ensure peak performance, energy efficiency and a long operating life from your air compressor, it is essential to determine the required CFM for the facility. Experts recommend the following calculation to establish the correct CFM requirement for your application:
Determine the CFM for each tool:
Because the air compressor will likely need to power several pneumatic tools and pieces of equipment at one time, the first step is to take note of the manufacturer’s CFM specification for each piece of equipment. If the CFM isn’t listed on the tool, check the product manual or contact the manufacturer for this information.
Calculate the total CFM requirement:
After noting the CFM for each tool, add together the CFM requirement for each tool and piece of equipment that will operate simultaneously. Once this number is determined, experts recommend multiplying that number by 1.5 to allow for brief surges of air upon startup.
Using this methodology, a sample CFM calculation would be: |
(CFM of all tools that will operate at the same time x 1.5) = Minimum CFM requirement For example, if you have three tools that will operate simultaneously and each has a CFM requirement of 10, the calculation would look like this: (10 CFM +10 CFM +10 CFM) x 1.5 = 45 CFM In this scenario an air compressor that has a CFM of 45 would be the MINIMUM CFM needed to power these three tools at the same time. It is sometimes recommended to boost the minimum CFM value by an additional 25% to allow for a margin of error, peak demand times when you may operate more tools at one time and for future growth. So, in this example, the recommended CFM would be roughly 56 CFM. |
Don’t Forget Pressure!
While the CFM calculation above serves as a guideline to help determine the required CFM, it should be noted that compressors are not just rated for a specific CFM. Rather, they are rated for a particular CFM at a specific PSI (or pounds per square inch), for example 100 CFM at 100 PSI.
An air compressor’s PSI rating indicates the amount of pressure produced by a compressor per square inch of area and impacts the compressor’s ability to provide the right amount of pressure, or force, needed for the job.
Therefore, it’s important for performance and efficiency purposes that the selected compressor is capable of producing the right CFM at the right pressure, or PSI. To determine the necessary PSI for your facility, you do not have to find the sum of all of the PSI values in the facility, instead simply use the PSI value of the tool that requires the greatest amount of pressure. Be sure to take pressure drop through the distribution system into consideration as the compressor will have to overcome that also when suppling the tool with its required pressure and flow.
To have an optimized air compression system, the compressor must be able to deliver the required CFM at the proper PSI. To ensure that this is the case, be sure to ask the air compressor supplier for the CFM rating (as mentioned earlier sometimes called the free air delivery FAD, ICFM or ACFM rating) at the required pressure or PSI.
Although it may seem time consuming and possibly confusing to determine the proper CFM for an air compressor, it is essential to do so in order to avoid over- or under-sizing an air compressor for your facility as the CFM will impact the performance of all the pneumatic tools and equipment, as well as the energy efficiency of the system and facility. It is always worthwhile to speak with a knowledgeable supplier of air compressors, such as JHFOSTER, to ensure that you are selecting the compressor with the proper CFM value for your facility’s needs.