How the Degrees of Freedom of a Robot Define Its Capabilities
Industrial robots are reshaping the manufacturing industry because they maximize quality, efficiency, speed and throughput while reducing costs and helping to manage the ongoing labor shortage. So, as more manufacturers consider robotics for their operations, they may encounter the terms “number of axes” and “degrees of freedom” and find the terminology confusing. However, it is an essential specification during the robot selection process, as the number of axes and degrees of freedom of a robot define its capabilities.
Simply put, more degrees of freedom in robotics mean the equipment has a greater range of motion, while fewer degrees of freedom of a robot mean there is less flexibility and dexterity. While it may seem like a case of “more is better,” that’s not necessarily accurate.
The “right” degree of freedom in robotics is highly dependent upon the needs of the application. Without enough movement, a robot will be unable to complete the necessary motions of the application, while too many degrees of freedom in a robot may add too much complexity, making the robot unnecessarily complicated to control and program.
For this reason, it is important to understand how many degrees of freedom are required for an application during the selection process. To make things clearer, this blog will explore the definition of degrees of freedom, discuss the impact the degree of freedom in robotics has on capabilities and provide general guidelines as to how many axes and degrees of freedom each kind of robot is likely to offer.
What is Degree of Freedom in Robotics?
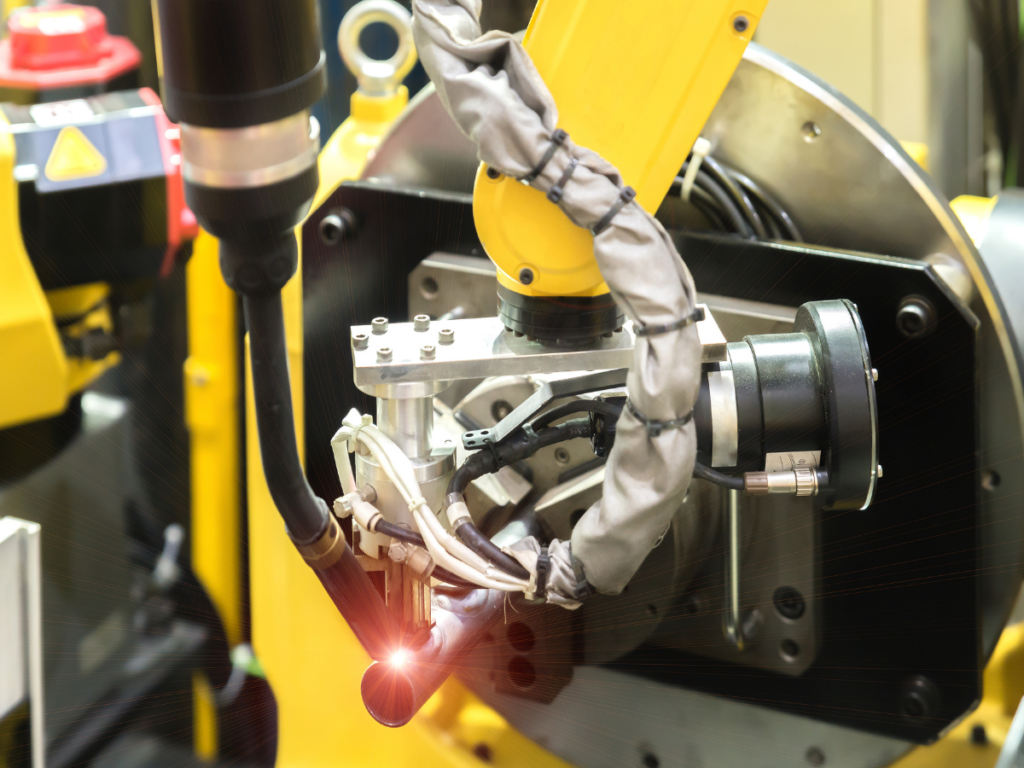
The simplest definition for degrees of freedom of a robot is the number of independent movements the robotic arm can make. Degrees of freedom are related to the number of axes the robot offers because robot axes operate on an X-Y-Z Cartesian plane. For example, a 3-axis robot can move (in a linear direction) up and down, left and right and forward and back, giving it three degrees of freedom.
And a 6-axis robot, which is considered fully articulated by industrial robotic standards, offers six degrees of freedom as it can perform the same three linear movements as a 3-axis robot, but can also complete three rotational movements including twisting, tilting and rotating the entire arm. Adding additional joints results in additional degrees of freedom and more flexibility. So, adding a wrist joint to a 3-axis robot would give it four degrees of freedom and adding an additional joint or joints on a 6-axis robot would provide seven or more degrees of freedom.
For a better understanding, here are the basic movements possible according to the degrees of freedom of a robot:
- One degree of freedom means the robot can move in one direction along a linear path, such as opening and closing a gripper or moving up and down.
- Two degrees of freedom in robotics indicates that the robot joint has two independent motions, such as moving up and down along one axis and rotating left and right around a second axis.
- Three degrees of freedom supplies three independent motions, such as forward and back, left and right and up and down on a linear path.
- Four degrees of freedom allow forward and back, left and right and up and down along a linear path, but with the addition of a wrist or other joint, it can twist or rotate at that joint for a fourth motion, such as tilting or twisting.
- Five degrees of freedom deliver the same three motions as a 3-axis robot, but the addition of a more complex joint allows twisting and tilting for more precision than a robot with just three or four degrees of freedom.
- Six degrees of freedom make available the same three linear movements of a 3-axis robot but additional joints enable twisting, rotating and tilting movements of the arm itself. These are usually 6-axis robots.
To put that information into a different perspective, various types of robots offer different degrees of freedom, for example:
SCARA robots | Provide three degrees of freedom as they have two rotational joints on a horizontal plane and one vertical joint. This makes them suitable for tasks such as assembly and pick and place. |
Cartesian robots | Have three degrees of freedom because the three linear joints allow them to move up and down, left and right and in and out, making them useful for pick-and-place and stacking or palletizing applications. |
6-axis robots | Six rotational joints deliver six degrees of freedom as they have the dexterity to move up and down, left and right and in and out but can also offer twisting, tilting and rotation. They can be used in applications such as welding, machine tending and delicate assembly, which require more precision and dexterity. |
Delta robots | Supply between three and four degrees of freedom, so their functionality would be similar to a 3-axis robot, but with an additional wrist joint they can be used in applications where a gripper is needed to manipulate objects for pick-and-place or packaging tasks or to handle a screwdriver for assembly. |
When selecting a robot for a particular application it is crucial that the robot has the appropriate degree of freedom for the task because, although it may seem that having more degrees of freedom in a robot is beneficial, that is only true when additional degrees of freedom are needed to grant more precision or dexterity to the application.
In less complex applications, more degrees of freedom will require more complex control and programming, as well as more maintenance, and may hinder the project or create additional capital and operational costs. Too many degrees of freedom in a simple application can also create issues with path planning, collisions and joint coordination. In these cases, the old adage “less is more” is apt.
A robot’s degree of freedom defines the physical motions and capabilities of the robot, including its range and reach, repeatability, performance and efficiency, so choosing a robot within the “sweet spot” of degrees of freedom for a particular application will allow it to perform the necessary range of motion with the least amount of complexity and cost. JHFOSTER has the experience and personnel to help determine the appropriate degrees of freedom for your application. Please consult your local JHFOSTER Sales Representative for more information or contact Automation & Robotics Solutions, A Tavoron Company.