8 Questions to Ask When Choosing a Robotic Palletizer
Most manufacturing, warehousing and distribution centers must build pallets of products for storage or shipping. When done manually, the task can be time consuming and ergonomically challenging for employees and, when mixed pallets are part of the operation, figuring out the optimal stack configuration can be tricky. Exacerbating these issues is that it is becoming increasingly difficult to find and retain workers in palletizing positions because the work is both physically taxing and mundane.
For these reasons, many operations are considering purchasing a robotic palletizer, but selecting the one that best fits the parameters of the application can be rough. This blog will outline the basic types of robotic palletizers and provide a list of essential questions that will help whittle down the choices during the selection process.
Types of Robotic Palletizers
Robotic palletizers are available in several different types, each with many available configurations and features. The most common include:
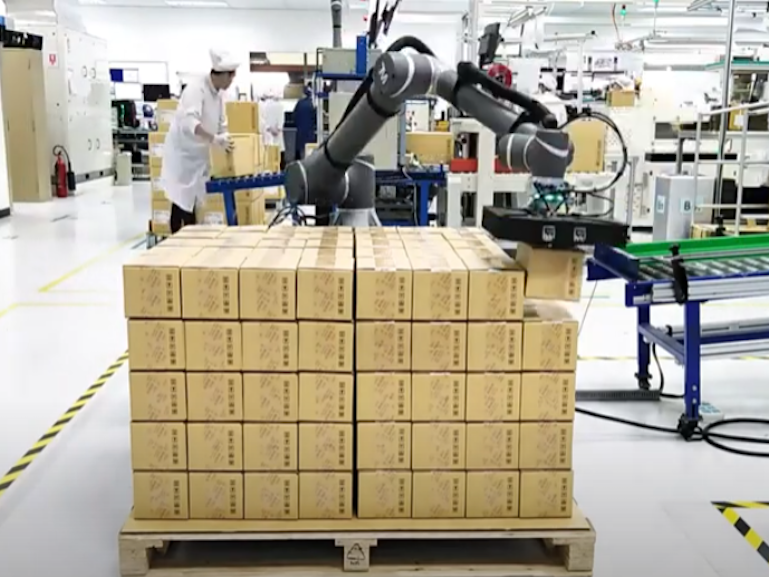
- In-Line Palletizers: The simplest type, in-line palletizers use articulated arms or gantry-style robots and specialized end of arm tooling to service one or more palletizing lines. While they consist of just a single robotic palletizer for the entire operation, some may feature the ability to place tier or slip sheets or dispense pallets.
- Palletizing/Depalletizing: Capable of performing all the functions of an in-line palletizer, these robotic palletizers can also perform depalletizing functions.
Please note that while the name suggests they can perform both functions, it really just means that the robotic palletizer can be programmed for use as a depalletizer.
- Layer-Forming Palletizers: These palletizers consist of an integrated system of multiple robots where each robot performs a single task. For example, one robot may layer products, while another stacks them. Because this greatly increases speed, layer-forming palletizers are ideal for high-throughput situations.
- Mixed-Configuration Palletizers: Ideal for pallet loads that contain a mix of products or container types, mixed-configuration palletizers can create stable, optimally organized layers from boxes and cases of varying sizes and shapes. They are available in a variety of configurations and capabilities. For example, a robot that is mounted to a track might move between a series of pallets, select a product and finally set it onto the receiving pallet, forming stable and efficient layers. Another mixed-configuration palletizer may involve a series of conveyors that feed product into a staging area where a robotic arm selects and orients the products, forming layers into a load that is guided to an end stop where it is finally lifted onto a pallet by a robot.
8 Questions to Ask When Choosing a Robotic Palletizer
While selecting the ideal robotic palletizing system from the many types and configurations can be confusing, answering these eight questions may help narrow down the choices. After selecting the robotic palletizer type or model that seems well suited to the application, talking to a reputable manufacturer or supplier can provide further assistance with choosing an appropriate model and the best accessories.
To start the selection process, consider gathering the information to answer the following questions:
- What types of products are being palletized? Noting the size, shape and material characteristics of the products being palletized, as well as the container type, dimensions and weight will help determine the required payload of the robot, as well as whether specialized end effectors will be needed.
- What are the current palletizing needs? In addition to knowing the required throughput, be sure to consider the expected configuration of each pallet, including number of layers, different layer arrangements, if you anticipate mixed pallets and whether slip or tier sheets are required.
- What type of speed and accuracy are required? The robotic palletizer must be able to provide the necessary throughput, so speed is an important consideration here. Be sure to look into palletizing rates and inquire about guarantees regarding those rates. Also, accuracy can be crucial to meeting quality standards, so it may be important to ask how accurately the robot can place product onto pallets while maintaining the required speed. In other words, you don’t want a robot that moves quickly, but doesn’t properly stack the pallet.
- Will there be variability in the products or pallet configurations? If the products change frequently or the pallet configurations may differ in the future, flexibility is important. In these cases, it’s best to seek out a robotic palletizer that can easily be reprogrammed or re-tooled to handle changes in product or pallet configurations without the need for costly downtime or major modifications.
- How many robots will be needed? If there is a complex product mix or pallet configuration or if it is a very high throughput application, several robotic palletizers may be required to handle the operation. Typically, robotic palletizers can be purchased individually or as part of a system that allows multiple palletizers to run simultaneously.
- What end of arm tooling is most appropriate? This is related to the type of product being palletized. There are many end effectors available that are designed to gently handle all sorts of products, boxes, bags, cases, containers, etc. Consider whether vacuum cups, compression plates or some type of gripper will be best suited to the application.
- Where will the robotic palletizer be located? It’s essential to know where the system will be located, as well as the location of the packaging or production equipment it will serve, to determine how the palletizer will be arranged, whether a robotic arm or gantry-style robot will best serve the application and what reach will be required. Robotic palletizers can take up significant space in a facility, so it’s important to determine how much area will be dedicated to the palletizing operation and to find a palletizer that meets these specifications. Also helpful: determine ahead of time that there is sufficient mechanical and electric support near the location.
- What type of safety systems are necessary? As with any piece of industrial equipment, safety should be a high-priority concern. It’s important to ensure that the robotic palletizer comes with or can be equipped with safety features such as pallet guards, light curtains and emergency stop mechanisms.
Taking the time to gather the information needed to answer these questions and discuss options with a supplier, such as JHFOSTER, will be worthwhile and ensure the selected robotic palletizer easily meets the throughput and quality requirements while also boosting the efficiency and safety of the palletizing operation.