Troubleshooting Industrial Control Panels
SAFETY NOTES AND DISCLAIMERS:
- Industrial control panels use hazardous voltages! If handled improperly, serious injury or death may occur!
- Do not open their enclosures and do not attempt any of the troubleshooting procedures herein without first receiving an electrician certification and/or formal electrical training approved by your employer.
- Contact the manufacturers of your machinery and control systems to obtain all pertinent documentation and to receive technical support.
- Always follow their procedures and your employer’s procedures; especially lock-out tag-out procedures.
- Always wear the appropriate personal protective equipment.
- If a control panel malfunctions, it may allow or instigate abnormal hazards within machines and processes. Therefore, it is equally important to be formally trained in your machines and processes to be able to identify and resolve abnormal behaviors and dangerous conditions.
- JHFOSTER assumes no liability for the health and safety of individuals who are not employed by JHFOSTER or who are outside of JHFOSTER’s property.
- JHFOSTER assumes no liability for the safety of JHFOSTER machinery or control systems that have been functionally altered by anyone other than JHFOSTER personnel.
- By default, it is the end user’s responsibility to conduct risk assessments of machinery and control systems manufactured by JHFOSTER.
Resolving Four Common Malfunctions in Industrial Control Panels
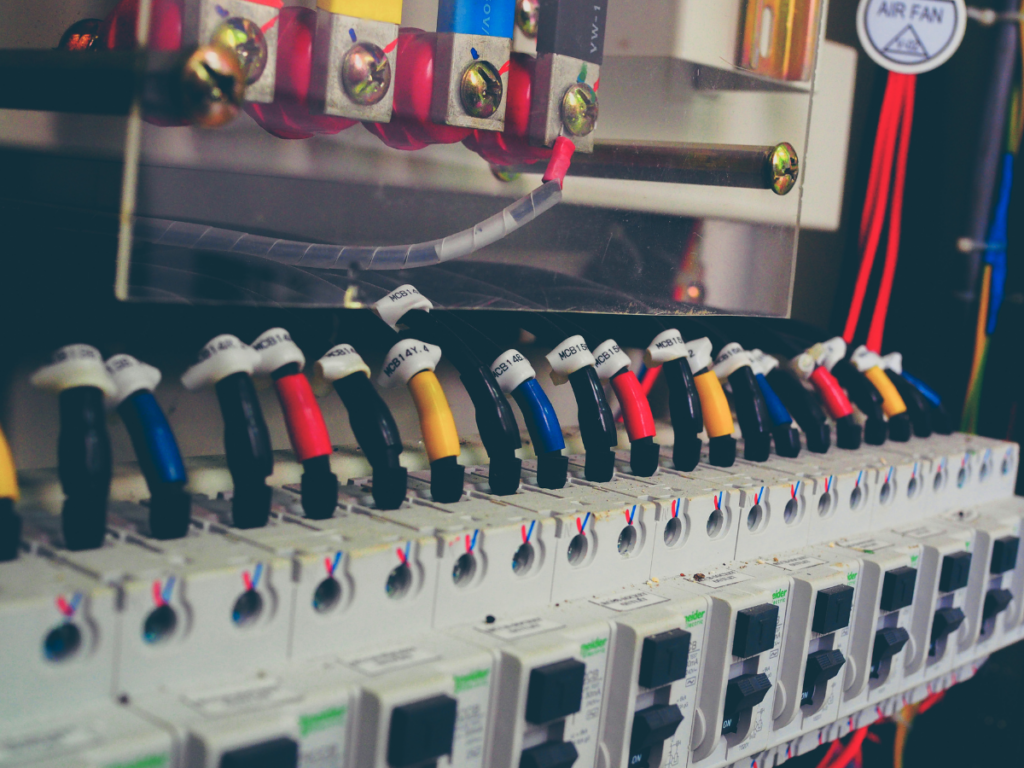
Control panels vary by application, but they should always possess protective devices (circuit breakers and/or fuses), disconnecting switches, means for locking-out power sources, and means for safely bleeding stored energy. Typically, they also contain transformers, AC-DC power converters, motor starters, variable frequency drives (VFDs), servo motor drives, motion controllers, safety controllers, control relays, programmable logic controllers (PLCs), human machine interfaces (HMIs), network switches, and various other
components, some of which may require an expert to repair or replace if they become damaged or worn out.
Power Issues | may present as voltage fluctuations, tripped circuit breakers, or blown fuses, and they may be caused by external power surges, external overloads, or internal faults. Confirm that the incoming voltage is consistently within tolerance according to the manufacturer’s documentation. Ensure that the control panel is properly grounded to prevent induction and static noise. If the issue persists, contact your power provider to resolve the issue. |
Overloads | occur when too much current flows through a circuit and causes circuit breakers to trip and/or fuses to blow. It is likely caused by using too many devices on a single circuit or devices that draw too much power. If an overload occurs, measure the continuity of the circuit and the resistance of the loads to determine if there is a short circuit. Confirm that the circuit breakers, fuses, and corresponding loads are correct according to the manufacturer’s documentation. If the issue persists, contact the manufacturer of the control system for technical support. |
Faulty Wiring | such as damaged/stretched/internally-broken cables, loose or insulated terminations, and improper routing/shielding can lead to intermittent faults, short circuits, and risk of injury. To rule out such issues, check the continuity between wired terminals (ensure they are not biting on insulation) and ensure the terminals are properly torqued. |
Components | such as mechanical relays, switches, motor contactors, etc. are more prone to failure than their solid-state counterparts. They are usually easy to discover because they no longer function, sometimes because their contacts have been slightly welded together during a prior overload event. Sensitive electronic components such as PLCs, motion controllers, HMIs, and others are prone to damage if they’re not protected from power surges, short circuits, static electricity, kinetic impacts, water/condensing humidity, high temperatures, etc. |
General Troubleshooting Procedure
- Fully Acquaint Yourself with the Symptoms: Gather as much information as possible about the symptoms and circumstances surrounding the failure. Question witnesses such as machine operators and maintenance personnel. Check surveillance systems, data historians, etc. to build a timeline of events and help narrow down the potential malfunction. A thorough visual inspection may reveal damage, loose wires, burn marks, or corroded components. There may be an acrid odor lingering around certain components. There may be abnormal noises from process equipment during operation. Some mechanical or electrical components may be overheating, so an infrared thermometer is handy too.
- Testing: Use proper multimeters with appropriately insulated leads and probes to help render a diagnosis. Before reapplying power, measure the continuity of the circuits and the resistance of the loads to determine if there are any short circuits. Also, confirm that the circuit breakers, fuses, and corresponding loads are undamaged and correct according to the manufacturer’s documentation. If all is well, then reapply power and begin confirming that the correct voltage is reaching each component, starting with the loads that are malfunctioning and working your way back. For example, if a motor is not running, and it’s not receiving any voltage, then check if its contactor is receiving voltage, and so on.
- Make the Repair: After identifying the root cause of the problem, the faulty component should be replaced or repaired following the proper procedures.
- Test and Verify: To confirm that you have corrected the problem, run the control panel through a normal cycle and monitor its performance. If there are still malfunctions, abnormal behaviors, or error codes, and you are at a loss, then contact the manufacturer for assistance.
Once the issue has been corrected, remember that performing preventive maintenance can help avoid future issues. Scheduling regular maintenance for machinery, installing surveillance cameras, and installing additional process instrumentation can help identify intermittent issues to expedite future troubleshooting efforts and minimize downtime.
For more information and automation products and services, please contact JHFOSTER