Get the Most from Your Automatic Palletizer with Customization
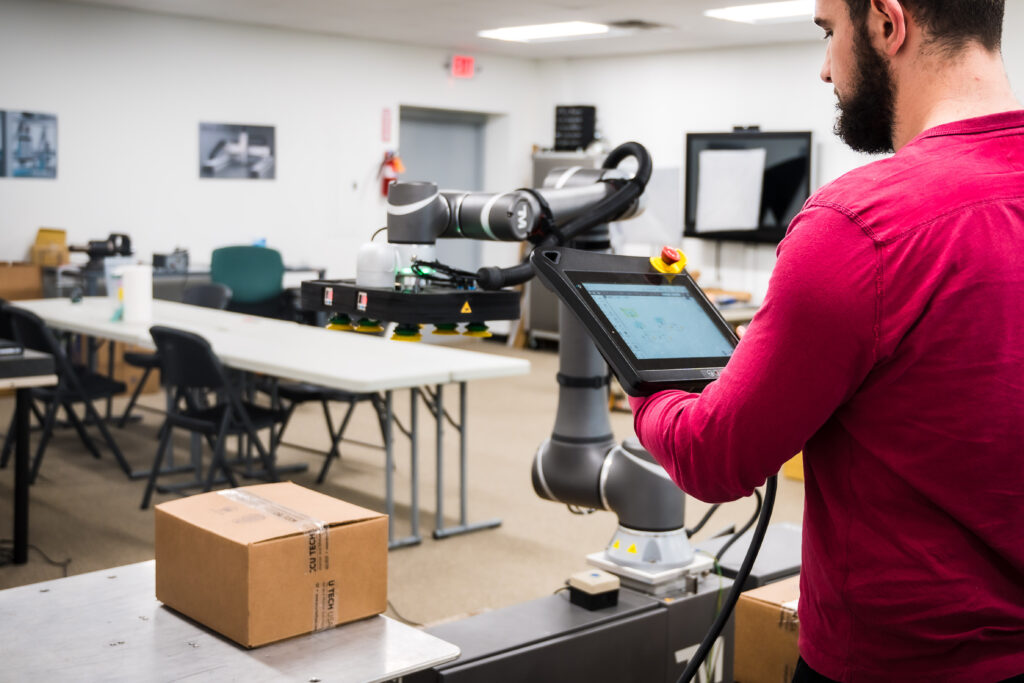
For manufacturers and packagers struggling to increase efficiencies to offset rising costs and supply chain challenges, automatic palletizing can be a great solution as it can significantly boost throughput and reduce costs. However, an automatic palletizer must be well implemented and suitable for the individual operation to provide the most benefits – of which there are plenty. We’ll take a look at the benefits of automatic palletizing and how customizing a solution to meet specific application requirements can further enhance business efficiency in this blog.
What is Automatic Palletizing?
While manual palletizing involves stacking bags, boxes, cases or other items onto a pallet by hand, automatic palletizing is an automated solution used to stack and organize these items onto a pallet with greater efficiency and speed. The automated palletizing process can work in different ways. In some cases, machines with mechanical arms move items from a line or staging area to the pallet where it positions them according to programmed settings. Other automatic palletizing solutions physically push the objects into stacks and then lift the stacks onto the pallet. In either case, automatic palletizers are programmed to perform the task according to defined patterns and to do so with greater efficiency, higher speeds and better accuracy than manual palletizing processes.
Advantages of Automatic Palletizers
In industries where loading pallets is a routine task, it can be time consuming and repetitive and often causes bottlenecks and results in injuries if handled by manual laborers. However, automating the palletizing process offers many benefits including:
Enhanced throughput: Automatic palletizers are more efficient and capable of lifting heavier loads than their human counterparts and can operate 24/7, reducing bottlenecks, injuries and inefficiencies in the process. Due to the programming, automated palletizing systems are also often able to get more product into less pallet space, as well.
Higher levels of accuracy: Because automatic palletizers are programmed to select and stack products according to a pre-set configuration, they do not make mistakes when selecting products or layering them, which reduces the incidence of incorrect products being placed on a pallet.
Improved safety: Replacing manual laborers with an automatic palletizing system reduces or eliminates the occurrence of repetitive motion injuries associated with bending, lifting, twisting and stacking, as well as those associated with crushing hazards, in manual laborers.
Reduced labor costs: Automated palletizing systems can work 24/7, do not require breaks and stack pallets faster than the human workforce, so the cost per hour for palletizing operations is much lower when using automatic palletizers versus manual laborers.
Types of Automatic Palletizers
Several different types of automatic palletizers are available to suit a variety of needs and application requirements, but they fall into three basic categories: robotic palletizers, conventional palletizers and hybrid models.
- Robotic palletizers: These compact solutions use a fast-moving robotic arm to move objects onto pallets in a pre-programmed pattern. Paired with end of arm tooling, they can stack a variety of products, bags, boxes or crates from one or more infeed locations or conveyors and build layered stacks that are then moved to a highly organized, space-efficient pallet.
- Conventional palletizers: Conventional palletizers form partial layers of product onto a “squaring plate.” Once the layer is complete, the doors beneath the plate open, allowing the completed layer to drop onto the pallet below. They are available in high- and low-level models. High-level palletizers are faster than low-level models. Conventional palletizers are known for creating very compact pallets.
- Hybrid-robotic palletizers: These palletizers combine a robotic arm with the features of conventional palletizers in a single solution. The robotic arm is equipped with specialized end of arm tools that can pick up and place objects, including bags and odd-shaped objects, but they layer them as a conventional palletizer would to create a compact pallet.
Customizing Automatic Palletizing Solutions
While the availability of different types of palletizers suits the majority of applications, organizations seeking the most efficiency from the operation may want to consider customizing an automatic palletizer to fulfill the unique needs of the application. For example, some businesses may need to stack different sizes of products or a mix of bags and boxes, while others handle delicate materials and must pack them in a way that prevents damage during the palletizing operation and during transport and still others may need the palletizer to stand up to washdown routines. To ensure that the automatic palletizing solution does indeed provide the
most benefits and efficiency to the organization, it’s important to consider several factors when customizing a solution, such as:
Product to be handled | What type of products will be handled? Will it be bags, boxes, cases, trays, jugs, bottles, pails, drums, bundles, etc.? Are they delicate, fragile or sensitive? Are there a variety of SKUs involved? What are the dimensions and weight? What case rate is expected? How will the product enter and leave the automatic palletizer? |
Pallet information | In order to achieve a desired or unique pallet configuration, it’s important to determine how many different pallet patterns are needed, if slip or tier sheets will be used, the type of pallets that will be used and the weight and dimensions of the pallets. |
Stacking formation | Does the application require individual cases, rows or entire layers? Will the columns be stacked, interlocked, pin-wheel configured, mixed loads or variable patterns? |
Built-in capabilities | Is automatic pallet dispensing a necessity? Will you require integrated stretch wrappers, pallet labelers or other accessories or additional equipment? |
Application-specific needs | Is this an atypical application or is the product delicate or specialized in any way that will require customized end of arm tooling to guarantee product quality and pallet stability? Is a vision system needed for multi-SKU palletizing or quality control purposes? Do you require integration of third-party barcode scanners, printers and labelers? Does the application require stainless steel components to meet sanitary needs or washdown requirements? Any of these requirements lend themselves to customization. |
Production environment | Are there physical obstructions that may interfere with the operation of the palletizer? Can the ceiling height and concrete floor accommodate and support the palletizer in action? Are there special requirements for safety, guarding, heating or cooling, etc.? Many palletizers can be customized to accommodate smaller footprints, use in freezers or special safety requirements. |
Choosing the right automatic palletizer and customizing it to meet specific application requirements is the best way to ensure the most efficient and reliable operation. When selected, customized and installed properly, automatic palletizers can significantly boost business efficiency by providing higher throughput, increasing safety, reducing labor costs and ensuring accuracy. Contact JHFOSTER today to learn more about customizing automatic palletizers.