How to Determine the Cost of a Robotic Palletizer
Lifting and stacking heavy cases, boxes, sacks or other containers onto pallets is backbreaking, labor-intensive work for the employees charged with industrial palletizing. Not only is the task difficult on the human body, but it must be accomplished in a safe, efficient and consistent manner that prevents damage to the products, which is no easy feat. For these reasons – and many others – robotic palletizers are a good investment for companies with intensive palletizing operations or those who can’t find or retain capable workers; however, it can be difficult to determine the actual cost of robotic palletizer, as well as the anticipated return on investment (ROI). This blog will explore the advantages of robotic palletizers and provide information on accurately estimating the cost and ROI of the investment.
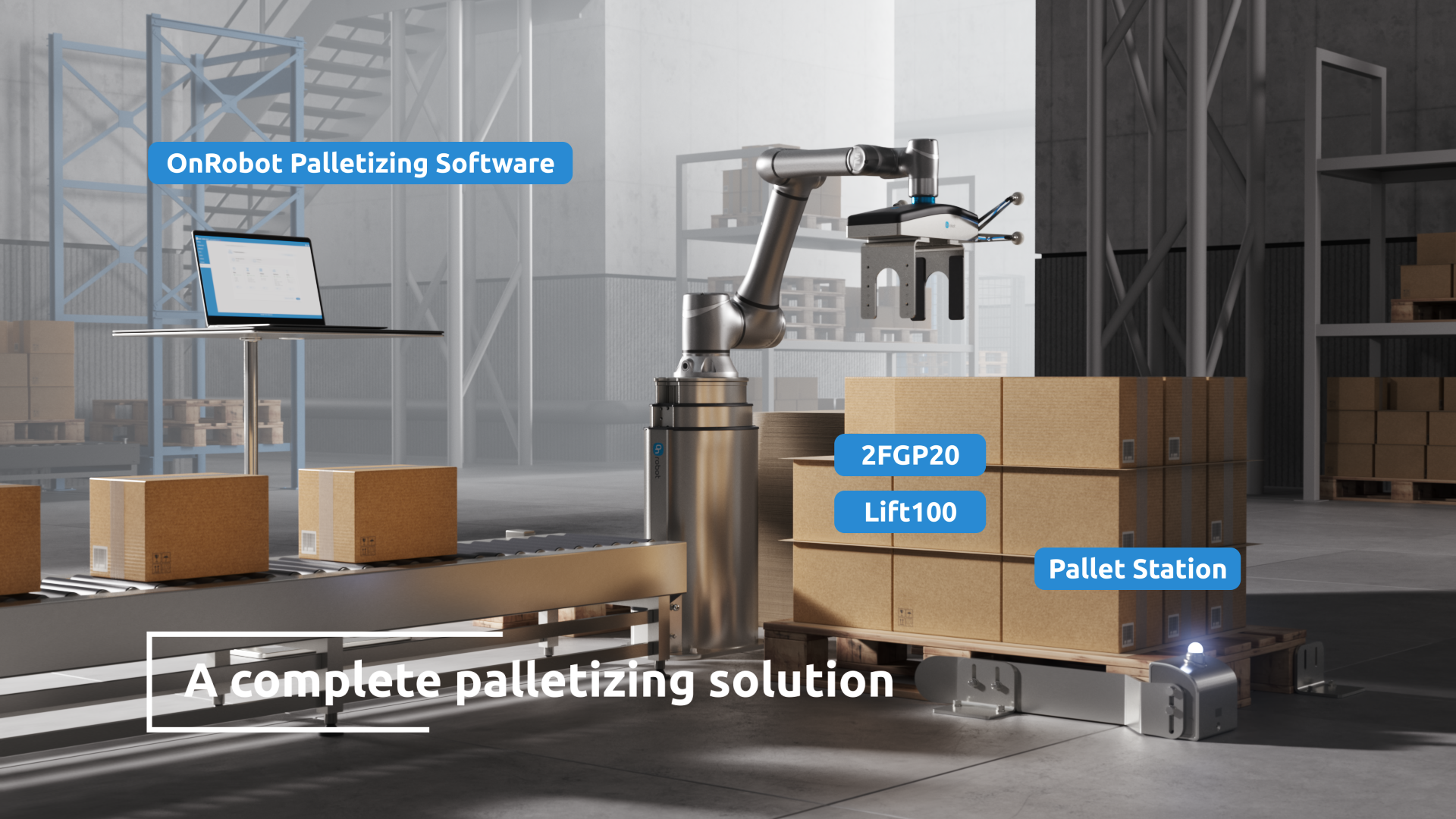
The Advantages of Robotic Palletizers
Products are palletized in nearly every industrial manufacturing or warehousing setting, but it is a repetitive and dangerous job for human workers…if you can find employees who are willing to take on and stay with the task. Because it’s getting more difficult to retain workers, many organizations are considering deploying a robotic palletizer, which provides an automated way to get the job done safely, efficiently and with less product damage. As a matter of fact, there are several reasons to invest in robotic palletizers, including:
Offsetting labor shortages | Because it is such labor-intensive work and because we are still in the midst of a labor shortage, robotic palletizers can help offset these workplace management challenges. In addition to providing a more efficient way to get the job done, the cost of a robotic palletizer often pays for itself quickly as it eliminates the costs of salary and insurance benefits of several paid employees. |
Increased safety | Even if you are able to source and retain workers, palletizing is a hazardous position as the repetitive lifting motions often result in back and musculoskeletal injuries. Robotic palletizers can reduce or eliminate these types of injuries and the associated expenses to the business. |
Increased efficiency | Robotic palletizers can do the job of lifting and stacking at a much faster pace and with 24/7 availability, unlike human workers who fatigue easily and require frequent breaks and shift changes. The increased speed and continuous availability will significantly boost throughput. In addition, human workers can be used to complete more complex tasks that provide value to the bottom line. |
Better quality | Human error is a part of the human workforce. They may make mistakes in selecting products/containers to be palletized. They may drop, damage or harm the products to be palletized. Or, they may be inconsistent in the way the items are loaded. Robotic palletizers, on the other hand, can be programmed to select the appropriate items, are not likely to drop or damage the product, can maintain consistency between containers and can properly distribute them on the pallets. All of these factors lead to gains in product quality and a reduction in scrap, waste, returns and re-work. |
Increased flexibility | As the manufacturing industry fluctuates, so do palletizing operations, which may have variability between pack formats or SKUs. A robotic palletizer can be easily reprogrammed to incorporate these changes and modern robots offer flexibility via adjustable end-of-arm tooling. In addition, flexible robotic palletizers can be programmed to pack multiple products on a single pallet. |
How Much Will a Robotic Palletizer Cost?
With all the potential advantages, it is easy to see why many industrial manufacturers are considering deploying a robotic palletizer. However, determining the true cost of the equipment is not always as simple as looking at the price tag of the robot. There may be extra costs that should be considered, including:
- The base cost of the robot: Obtaining a quote for the robot from a robot supplier is the first part of the equation, but it is not the only one.
- Necessary accessories: Common accessories for a palletizing robot may include end-of-arm tooling, sensors used to detect boxes and pallets, vision systems (depending on the operation), cable management systems and additional axes that may be needed to extend the robot’s reach or workspace. These may or may not be included in the price of the selected robot, so be sure to inquire about them.
- Software and controller: Some robots come with software and a controller and some do not. In addition, a palletizing application may require specialized software unless it is a cobot or robot specifically designed for palletizing. It is always best to determine whether software and controllers are part of the package.
- Additional components: If your palletizing situation is unique or you would like a turnkey system, additional equipment such as conveyors, safety fences and pallet dispensers may be required. Any additional components should be factored into the total cost of the project.
- Design and integration: Additional costs may be incurred if there is a need to design and integrate a robotic palletizing operation. However, it may be possible to acquire a palletizing application kit for the robot, which will be a much less expensive alternative to hiring an integrator.
Determining the ROI for a Palletizing Robot
While the actual cost of a palletizing robot and all its necessary accessories may be higher than anticipated, it may be surprising to see how quickly a palletizing robot can pay for itself. Once you’ve determined the total cost of the palletizing robot project, you can compare it with the anticipated savings associated with the typical costs of hiring, training and retaining employees, as well as paying salaries, insurance benefits, overtime, medical bills, vacation days and sick days. All of these costs should be calculated for each employee who works on the palletizing operation for one year.
In addition, as mentioned above, there will be gains in efficiency, capacity and throughput, as well as additional benefits to the bottom line that come from waste, scrap and rework reductions, as well as savings from the reduction of injuries. While these are less tangible figures, it is possible to roughly estimate the savings/gains that will result from a robotic palletizer after one year of use and include them in the ROI calculations.
Once you combine the cost of hiring, training and retaining employees and their salaries and benefits with the savings and gains from the increased efficiency, safety, consistency and quality over the course of one year, that sum should be divided into the total cost of the project to determine the ROI or how many years it will take the project to pay for itself.
While there are different variables for each situation, many manufacturers find that a robotic palletizer pays for itself in as little as two years and, after that initial payback period, the robotic palletizer will provide many years of value for the company.
For more information on selecting a robotic palletizer and determining the costs and ROI, please contact JHFOSTER.