What Are the Components of a Compressed Air System?
When you first think of a compressed air system, you likely think of an air compressor first. However, there are many different components within a compressed air system that can make your applications more efficient and reliable. It’s not only important to select the right air compressor but to select the right parts and accessories for your system as well.
Another matter of importance is replacing and maintaining equipment routinely to ensure that your system does not experience downtime. In this article, we are going to dive into the basic parts and equipment within a compressed air system. To learn more about your compressed air system, read on.
Air Compressor
Air compressors pressurize and compress air for a variety of uses. From powering tools in manufacturing settings to creating medical air for ICU patients, air compressors power a variety of solutions in our everyday lives. There are three types of compressors commonly in use today: oil-lubricated, oil-less, and oil-free. Oil-lubricated compressors are used in environments where oil contamination isn’t of the utmost concern. Oil-less and oil-free compressors are used for applications where oil contamination is a great concern, often in industries such as food production and healthcare.
The longevity of an air compressor depends upon the type of compressor, application, and quality of maintenance. Working hours can range from 50,000 to over 200,000 hours depending on the aforementioned factors. To understand the point at which you may need to replace your air compressor, it is best to consult a user manual or a compressed air specialist.
Air Dryer
Air dryers solve a risky problem in compressed air systems. They remove water vapor from compressed air and reduce the dew point to a suitable level. While water doesn’t seem like a large problem, for compressed air systems, it is. Even a small amount of condensation over time can wreak havoc on other system parts including piping. Four types of air dryers exist, each with its own benefits: desiccant dryers, chemical dryers, refrigerated dryers, and finally, membrane dryers.
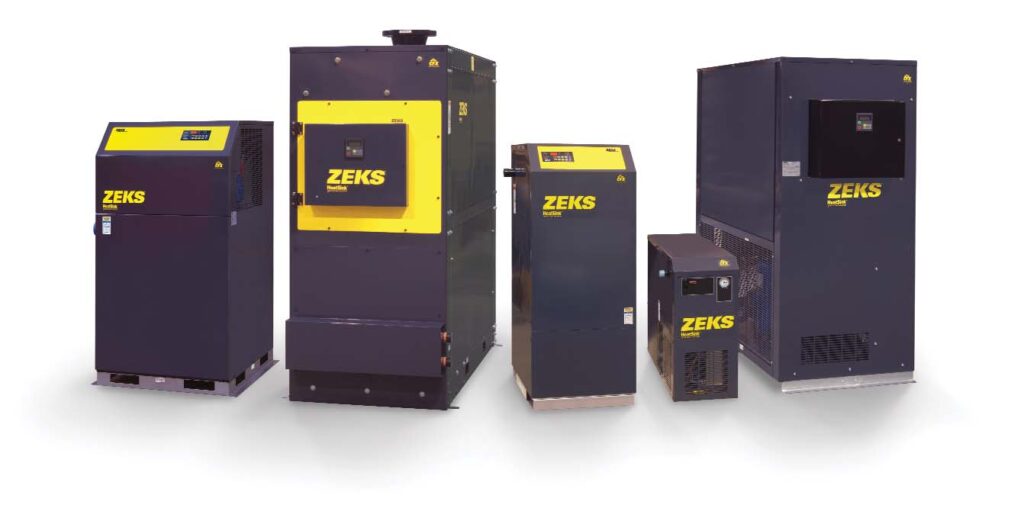
refrigerated dryers are designed to consume only the electrical energy
necessary to meet the actual demand for dry compressed air.
Air Receiver Tanks
When properly installed, air receiver tanks work as a buffer between compressor equipment and compressed air systems in the plant. This improves efficiency and reduces wear on the compressors. Air receiver tanks collect compressed air and retain said air under pressure. Air receiver tanks may also assist in condensing excess water. Air tanks have a life expectancy of several years if maintained properly. Ensure that your team is trained on proper care for your equipment.
Filters
Pre-filters and after-filters work together to keep compressed air free of contaminants. The pre-filter is usually a particulate type, located upstream from the dryer. They also have an added job of removing debris-like contaminants before they cause damage to other system parts. Whereas the after-filter is usually a coalescing/oil removal type, located downstream from the dryer. The combination of pre-filters and after-filters will present you with clean compressed air.
Generally, it is time to replace a filter if there is visible damage or there is extreme wear indicating that the filter has reached the end of its life. Regularly cleaning your air filter may extend its life.
Condensate Drains
Condensate drains are used to collect and drain the condensate removed by the compressor aftercooler, wet storage tank, filters and dryer. In many cases, energy efficient Zero air loss automatic condensate drains are recommended. As previously mentioned, condensate can create damage to other system parts if left to its own devices. As there are a variety of condensate drains and methods, it is best to consult with a compressed air specialist on the lifespan of your equipment.
Compressed Air Piping
Piping delivers compressed air to other locations within your facility where it is to be used. While there are many different types of piping used for this purpose, it is important to note that PVC piping should not be used within a compressed air system. PVC cannot withstand high pressures and may malfunction, even leading to injury of employees in certain situations.
Some compressed air piping is prone to corrosion such as steel. However, piping like aluminum and copper is resistant to corrosion and may offer you longevity.
Contact Us for Your Compressed Air System Needs
It is important to select the right compressed air equipment and accessories for your specific application. Specific industries and applications have standards and regulations associated with the use and maintenance of compressed air equipment. Ensure that your in-house or outsourced team of experts are up-to-date on such protocols.
If you need the help of compressed air specialists who understand the different intricacies of your applications, contact one of JHFOSTER’s team members. Our specialists have many years of experience in a variety of industries and can help find a tailored solution for your needs or perform maintenance to increase the efficiency of your compressed air system.