The Importance of Expert Service and Repair for Air Compressors
An air compressor is one of the hardest working pieces of equipment in most industrial facilities as it powers essential tools and machinery. So, when an air compressor is not running in optimal condition or – worse – at all, it can result in excessive costs for a manufacturer, including higher energy bills, shorter equipment lifespans, expensive repairs and, in the worst-case scenario, unexpected downtime and loss of production that can quickly escalate into tens of thousands of dollars.
Because industrial facilities already struggle to remain productive and minimize costs, it’s essential to have an air compressor service and repair plan in place to prevent the occurrence of these and other costly compressed air system outages.
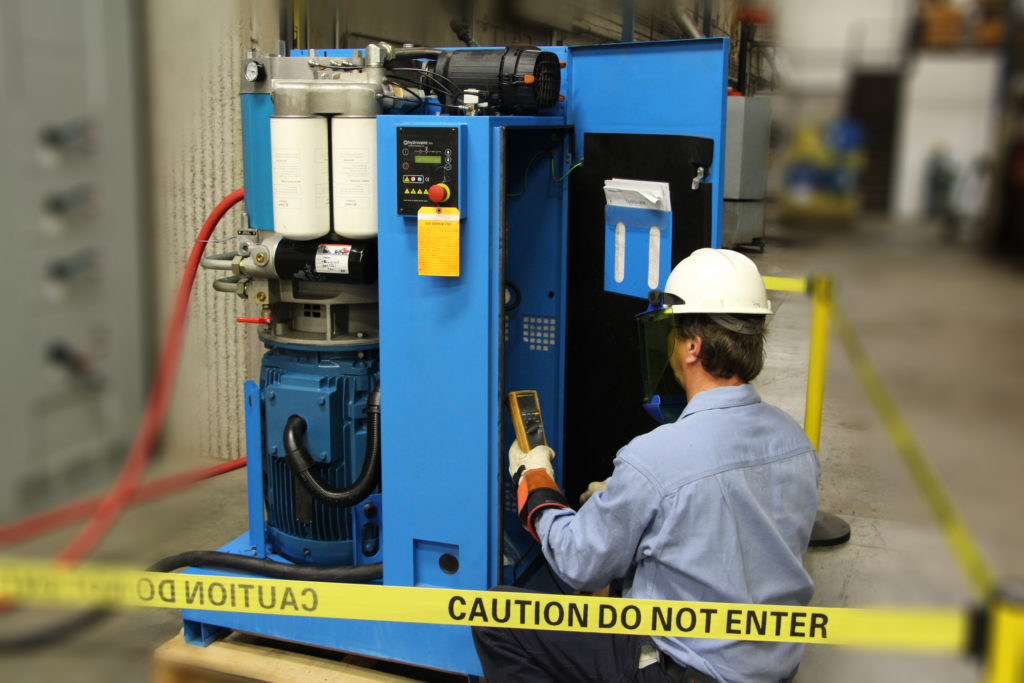
The Importance of Compressed Air System Maintenance
One of the best ways to thwart unexpected downtime is to ensure that preventive maintenance activities are being performed. Changing air filters, ensuring oil is changed, separator elements and oil filters are replaced, inspecting for component wear, checking for proper lubrication of, bearings and moving parts, inspecting drive couplings or belts for wear and proper alignment and tension levels, cleaning coolers and ensuring pressure relief valves and drains are in working order are just a few of the preventive maintenance tasks that should be performed on a regular basis.
Even with preventive maintenance, minor problems, such as pressure drop, can arise and often spell trouble for a facility in the form of higher electric bills, equipment that does not perform well and additional strain on system components. Finding and fixing the root cause of a pressure drop or other system issue in a timely manner is crucial to restoring air compression system performance, ensuring productivity and minimizing the chances of equipment failure and/or excessive electric bills.
Occasionally, more complex problems arise, such as moisture in the lines, a motor that’s not working properly, excessive heat or vibration or a cycling compressor. Addressing these more complicated repairs as they happen will help avoid the most serious mechanical breakdown of all – a non-functional air compressor.
4 Advantages of a Compressed Air System Service Provider
Often, on-staff maintenance techs can handle inspections and minor tasks, such as changing filters or inspecting system components, but as in-house technicians are generally not experts in compressed air system maintenance, they may miss telltale signs of trouble during inspections or may be stumped by issues in the air compressor system. For this reason – and others – smart manufacturers are turning over the responsibility of compressed air system maintenance to a certified compressed air system service and repair provider.
The trend toward outsourcing air compression system maintenance is growing due to advantages such as:
- Expertise and Specialization: Facility technicians tend to be jacks of all trades, but often do not have the focused experience of the certified specialists associated with professional service providers. Certified air compression repair specialists have the knowledge and expertise needed to identify a range of air compressor component and system issues and quickly and properly perform the repairs.
- Reduced Downtime: Because professional air compression system repair services are available 24/7 and have access to specialized inventory, they can respond quickly to maintain, repair or replace equipment in an effort to get a facility up and running as swiftly as possible. In addition, their knowledge makes the troubleshooting process faster and because they’ve likely handled the same problem numerous times, they are experts at performing the repair in the fastest possible manner. Further, service providers usually have access to specialized parts, allowing them to perform the repair in the most efficient and effective way, ensuring that productivity is not hampered and drastically minimizing downtime.
- Focus on Core Business: Manufacturers have one job – to produce their product. While air compression maintenance activities are a necessary pit stop on that journey, they are certainly not the core focus of the business. Hiring a professional service provider for air compression system inspections, maintenance and repairs frees up resources – and ensures optimal running conditions – so that the company can focus on doing what it does best – generating profits by producing product.
- Access to Advanced Tools and Technology: Expert service providers usually have access to the latest tools, equipment and diagnostic technologies needed to perform any repairs and maintenance on air compression system components. The ability to use advanced diagnostics and equipment will likely result in correcting smaller issues before they result in downtime and lost productivity. In addition, service companies can often provide expert advice about whether to repair or replace a component or system based on knowledge and professional calculations.
The experienced experts at JHFOSTER offer remote and on-site service and repair for your air compression system to help identify any equipment issues, as well as the ability to test and repair individual components or perform a complete equipment overhaul. The JHFOSTER Rapid Response team of experts offers on-demand assistance for a wide range of industrial equipment, including compressed air systems and filters, vacuum pumps, air dryers, blowers and other related equipment. The team maintains an extensive inventory of parts so any repairs to mission-critical equipment can be handled swiftly, ensuring productivity and keeping downtime to a minimum. Company specialists are trained to assure all repairs meet manufacturer specifications.
Compressed air and industrial equipment solutions from JHFOSTER’s Rapid Response Team include:
- Service and maintenance agreements and programs customized to meet your needs
- 24-hour emergency service
- Protection plans intended to keep equipment in good working condition and minimize risk of unplanned downtime
- Repair-versus-replacement recommendations
- Full service and repair on most brands
- In-house equipment overhauls on most brands
- New system application designs or existing system upgrade recommendations
- Complete turnkey installations
To take the hassle out of compressed air system maintenance and repair, ensure optimal running conditions and put the focus back on your core business, contact JHFOSTER for more information about our air compression system service agreements and repair services.