The Importance of Automated Inspection Systems in Packaging Verification
Damaged or incorrect packaging results in unhappy customers and negative brand recognition in the least detrimental situations and product recalls and regulatory fines in the worst, making packaging verification extremely important in most industries, but especially critical in others, such as food and medical manufacturing, where damaged packaging or incorrect labeling can interfere with human health and safety and result in costly product recalls and non-compliance with regulatory agencies.
In the past, product and packaging inspection and verification relied heavily on manual labor, but this was time consuming and carried a high risk of introducing human error into the process due to factors such as fatigue, boredom and the limitations of human vision in detecting defects. Packaging mistakes are costly, not only because of dissatisfied customers and potential product recalls, but also because oversights often culminate in product waste, additional production costs and re-work. However, thanks to advances in automation technologies, today’s automated packaging verification and inspection systems can help ensure product and package integrity.
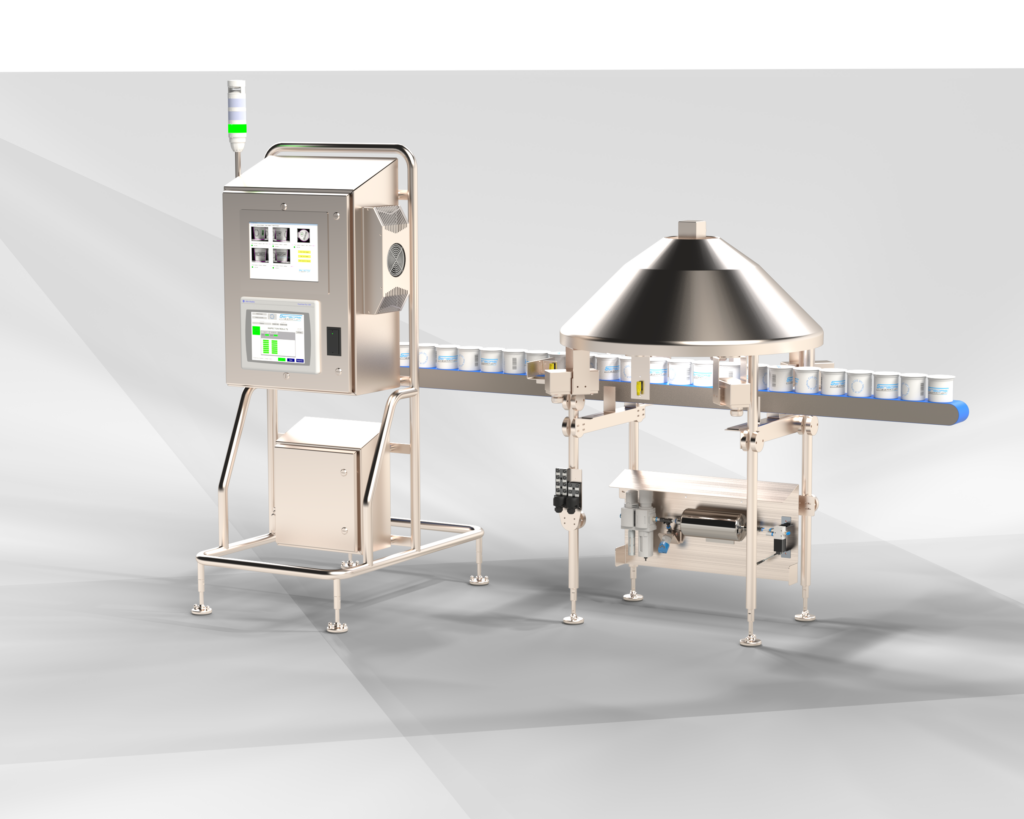
The Importance of Automated Packaging Verification
Aside from the obvious issues of customer dissatisfaction and product recalls, damaged or mislabeled packages can create expensive problems for manufacturers, such as production downtime, product returns, and chargebacks. However, reliable automated inspection and verification of packaging eliminates many of these issues because it employs advanced cameras and machine vision systems that provide high levels of accuracy and consistency with significantly fewer errors, which offers several significant financial benefits, including:
- Improved Quality Control: Reliably identifying defects and ensuring the integrity of packaging and proper labeling improves quality and reduces the chances of product returns, packaging waste, product waste, disgruntled customers, product recalls and regulatory fines. While improved quality control is important in all industries, it is of the highest concern in food and medical products as these items directly impact health and human safety.
- Ensuring Product Integrity: Verifying that products are safely packaged according to specifications and regulatory mandates (regarding food and medical products) helps ensure that products will remain intact and free from contamination, damage and spoilage every step of the way from transport to storage to store shelves to consumer homes.
- Minimized Product Loss: Products that are packaged according to specification are less likely to be damaged or lost during transport, reducing the costs associated with replacement and recalls. Automated packaging verification is critical to minimizing product loss as it easily finds and removes defective packaging.
- Reduced Chargebacks: When major retailers receive products that are not properly packaged, labeled or bar coded, they will reject materials. This results in costly rework and penalties that cut deeply into profits. Ensuring proper packaging and labeling through rigorous, accurate and reliable automated inspection and verification reduces the risk of rejected products and chargebacks.
- Strengthening Brand Image: When consumers receive products with open packages, damaged contents or incorrect labeling, it can have a negative impact on a business or brand. Ensuring that none of these incidents occur through the use of automated inspection and verification demonstrates that a company provides high-quality products, which positively influences brand image.
- Better Customer Satisfaction: Ensuring high-quality packaging and labeling through the use of automated packaging verification systems safeguards products from damage, ensures products are labeled and used correctly and creates a positive experience for the customer. Often this leads to repeat purchases and brand loyalty. In the food and medical industry, it also ensures that products will reach the consumer without damage or spoilage and be used safely and according to labeling instructions for consumption.
- Reducing Recalls and Ensuring Compliance: In regulated industries such as food and beverage and medical device or pharmaceutical manufacturing, regulatory compliance with packaging guidelines and labeling requirements is a must. Damaged packages and products, as well as labeling errors, can result in costly product recalls, which can ruin brand image. Further, if found to be in non-compliance with regulatory mandates, there can be fines and potential production shutdowns. For these reasons, reliable and accurate automated packaging verification and inspection are crucial.
Automated Systems for Packaging Verification and Inspection
To ensure that packaging – especially of critical products such as food/beverage and medical items – are safe, secure and properly labeled, it is essential to automate the inspection and verification process. This will not only eliminate missed defects related to human error, but it will help alleviate costs associated with labor hours and rework and will dramatically boost the speed and efficiency of the inspection and verification process, while increasing reliability and accuracy so packagers can rest assured that they are delivering high-quality, safe, secure and compliant packages to retailers and consumers.
The Control Reliable Inspection System, dubbed the CRIS System, from Sensors Integration is a product and packaging verification system designed to handle the demands of inspecting round, touching and randomly oriented products. The CRIS uses Sensors Integration’s fail-to-safe methodology to ensure that flawed items are rejected from the line by assuming that all products should be rejected until positively verified to ensure safety and accuracy.
Additionally, multiple cameras provide 360-degree product validation so that packages in any orientation will be correctly identified using barcode or pattern and then validated or rejected by the CRIS 360. This system is ideally suited for high-speed image processing for applications where patterns may be the only available aspect of the label to read (no code). This CRIS version uses the new Datalogic processor and E series cameras.
Another option, the Cognex CRIS, enables users to take advantage of fail-to-safe, control reliable product package inspection while utilizing Cognex components including imagers such as the Dataman and Insight, in addition to Cognex displays such as the VisionView.
Additionally, the Sick CRIS employs Sick laser scanners such as the CLVs and imagers such as the Lector series to provide fail-to-safe, control reliable product package inspection. Sick’s laser scanners are easy to set up and can read linear codes easily, even when damaged or when obscured by shrink wrap. For 2D codes, the Sick Lector series imagers are compact and easy to install.
CRIS systems offer logo integrity, pattern and color recognition, as well as time and date event recording, which allows users to track errors and changes in the system.
To learn more about how automated packaging verification and inspection with the Sensors Integration Control Reliable Inspection System can help ensure the quality and safety of a product’s packaging, while improving brand reputation, customer satisfaction, reducing costs and ensuring safety and regulatory compliance in food and medical product packaging, as well as other industries, please contact Sensors Integrated, a JHFOSTER company, today.