5 Benefits of Real-Time Analytics and Smart Manufacturing
When a manufacturing facility is running smoothly at full capacity, it can produce thousands of products per day…until a critical piece of equipment fails and production comes to a screeching halt, costing thousands of dollars per hour in downtime, lost productivity and repairs. No manufacturer wants to experience this scenario, but thanks to real-time analytics and smart manufacturing, such catastrophic failures can be avoided.
The Importance of Real-Time Analytics
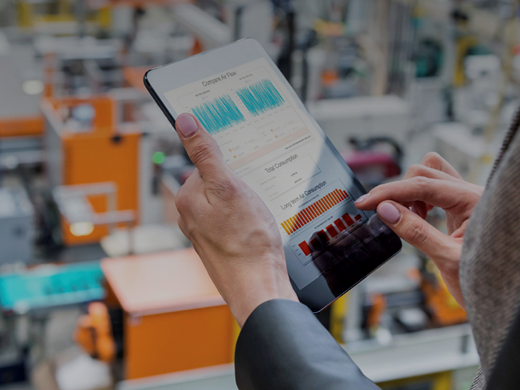
Data analytics uses various sensors and devices to constantly collect machine and process data, analyze it and present, in real-time, the most relevant parameters in an easy-to-understand display or report so that it may be used to make decisions that improve equipment performance, increase throughput, maintain product quality and decrease costs associated with downtime.
As a matter of fact, research from analytic database firm Exasol has found that without data analytics, 75% of manufacturer’s operational decision making would be completely or significantly disrupted. Why? Because combining real-time analytics with smart manufacturing enables manufacturers to shift from gathering thousands of points of meaningless data after an event has occurred to making decisions for process optimization based on current data as events unfold.
This ability to see current data about the functionality of equipment and the process gives operators more visibility into what is happening on the factory floor. And, this visibility, provided by real-time data analytics, can be used to make decisions regarding equipment health, bottlenecks, asset utilization and other critical operational factors, on the fly, preventing downtime and increasing throughput.
Operators and maintenance technicians can use the real-time analytics to answer questions such as:
- Why does this event keep happening?
- What is likely to happen in the future?
- How can I act upon this information to prevent problems and optimize production?
4 Ways Real-Time Data Analytics is Used in Manufacturing
Visibility provided by real-time data analytics is used by manufacturers in four ways, as follows:
- Descriptive Analytics: The simplest type of data analytics is descriptive analysis, which answers the question, “What happened?” Descriptive analytics allows users to collect and study data to detect trends and understand what went wrong so that it may be applied in the future to find a better approach to similar issues.
- Diagnostic Analytics: Diagnostic analytics studies the root causes of maintenance issues and helps operators and techs understand why a piece of equipment failed and what factors contributed to a bottleneck or other issue. Diagnostic analytics can be used to investigate specifications like temperature settings, vibrations, lubrication schedules, maintenance activities or performance indicators to determine why an event took place. This allows maintenance teams to identify and address underlying issues, which helps prevent the problem from occurring in the future.
- Predictive Analytics: Here, data analysis and machine learning algorithms can be used to predict when equipment is likely to fail or process upsets are likely to occur, allowing for proactive decisions to be made. When operators or maintenance technicians receive alerts, they can look at the current data and determine when breakdown is likely to occur and schedule proactive maintenance activities prior to failure, avoiding a catastrophic situation and preventing costly downtime.
- Prescriptive Analytics: Prescriptive analytics takes predictive analytics a step further to provide guidance and suggest maintenance activities that can be used to improve maintenance strategies such as repair or replacement that are intended to prevent failure altogether to fully optimize production and throughput.
5 Benefits of Real-Time Analytics and Smart Manufacturing
Using a real-time, data-driven approach in manufacturing in any combination of these ways can lead to process optimization and cost savings. The following are the biggest benefits manufacturers are likely to see when employing real-time analytics and smart, connected manufacturing for proactive decision making:
- Reduced Downtime: Rather than reacting after the fact, monitoring and analyzing real-time data collected from sensors mounted on critical equipment helps identify issues and anomalies before failure occurs so that corrective action can be taken. Predictive maintenance encourages a proactive approach so maintenance can be scheduled early enough to avoid unplanned downtime and emergency repair, saving thousands of dollars an hour in lost productivity and labor hours.
- Higher Productivity: Real-time data analytics can be used to help identify bottlenecks, inefficiencies and other areas that impede productivity. Armed with this knowledge, decisions can be made about how to correct inefficiencies to achieve the highest throughput.
- Reaching Energy Efficiency/Sustainability Goals: Data analytics can help monitor energy consumption and identify opportunities for saving energy, while reducing costs and carbon footprints.
- Prolonged Equipment Lifespan: Data analytics can be used to study and track equipment utilization and condition, as well as usage patterns. Knowing how critical equipment is run and maintained will allow manufacturers to prolong its life by redistributing workloads, ensuring routine maintenance is performed according to schedule and intervening before catastrophic failure occurs, prolonging the useful lifetime.
- Reduced Costs: The use of data analytics is likely to provide an excellent return on investment (ROI). By preventing catastrophic failure through enabling predictive maintenance and preventing costly downtime, reducing energy consumption, increasing asset utilization and prolonging the lifespan of critical equipment, manufacturers can save hundreds of thousands of dollars a year. In addition to reducing costs, data analytics can also help optimize operations and increase throughput and productivity without adding additional lines, which will increase revenue and boost the bottom line.
Embracing the power of real-time analytics and smart manufacturing fosters continuous improvement, proactive decision making, increased productivity and cost savings. In today’s competitive manufacturing industry, the use of real-time data analytics is essential for success. Find out how JHFOSTER can help you harness real-time analytics to save money and boost the bottom line.