Optimize Compressor Health with an Air Compressor Monitoring System
Compressed air is often cited as the fourth utility for businesses that rely on the resource for daily operations, so experiencing air compressor downtime can create a costly problem for manufacturers. However, a good air compressor monitoring system gives users the power of remote equipment monitoring and provides visibility into the compressor room, allowing optimization of compressor health and efficiency. This blog will explore the benefits of remote compressor control and highlight a Quincy air compressor remote equipment monitoring system, called ECONTROL+.
What is an Air Compressor Monitoring System?
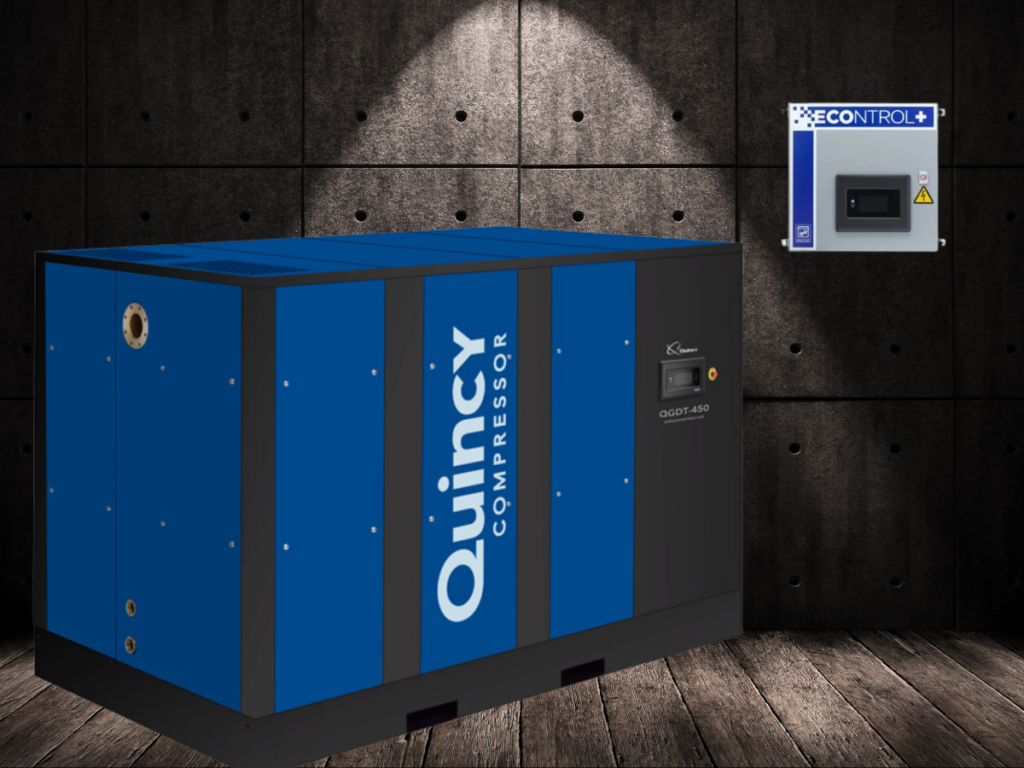
An air compressor monitoring system employs sensors and Internet of Things (IoT) technologies to remotely monitor the performance and health of the air compression system and provide real-time data and visibility into the compressor room.
Availability of this data allows manufacturers and other businesses to ensure that their compressor or compressors are operating safely, identify issues such as leaks and clogged filters and optimize performance of the air compression system to increase efficiency.
These remote equipment monitoring systems are typically used to measure a variety of points, including:
Pressure levels | Because optimal pressure is necessary for the best operation of equipment and is directly related to efficiency, many users opt to measure pressure at the compressors output and/or end points. Identifying pressure drops can indicate that there is a leak in the system or clogged filters that require attention, helping to keep efficiency at its highest and connected equipment running smoothly. |
Temperatures | Measuring the temperature of compressed air is another critical data point, as off-spec temperatures may indicate that a compressor is either overworking or underperforming, causing equipment wear and tear and/or reducing efficiency and effectiveness of the system. |
Power consumption | Efficient operation of air compressors is a constant battle. By monitoring power consumption of the air compressor, users can optimize its efficiency. Spikes in power consumption can also be used to identify potential mechanical issues within the air compressor. |
Oil levels | In oiled air compressors, monitoring oil levels is critical as low oil can damage the air compressor and result in downtime or catastrophic failure of the unit or its components. |
Vibration | Monitoring vibration on an air compressor can provide valuable insight on the status and condition of the bearings. Potentially alerting the user that an overhaul is needed prior to an unexpected failure. |
What are the Benefits of Remote Equipment Monitoring?
Air compressor monitoring systems allow visibility and insight into the compressor control room so that users are alerted to readings that are out of spec so they can spot potential maintenance and power consumption issues before they result in equipment failure, helping to reduce unplanned downtime and associated expenses. This type of manufacturing monitoring system continuously tracks the performance of connected compressors from one central air compressor controller to maximize uptime and efficiency.
The top five benefits of air compressor monitoring systems include:
- Centralized control: Users can remotely monitor air compressor performance from one centralized air compressor controller screen, simplifying the monitoring of machine status and reducing time spent in the field performing inspections.
- Increased efficiency: Continuous remote monitoring of the air compressor and access to insightful data helps users identify issues, such as rapid cycling and out-of-spec readings that may be limiting system performance and causing the air compression system to consume excess power. Early identification via air compressor monitoring systems allows technicians to troubleshoot and address these issues to help lower energy costs.
- Proactive maintenance: This type of manufacturing monitoring system can send alerts and notifications regarding irregularities in measured data points, as well as when the system is over or underperforming. Actionable data such as this allows users to be proactive rather than reactive to potential issues, so that maintenance can be scheduled before small issues become costly failures. This type of proactive maintenance maximizes uptime and productivity, as well as efficiency.
- Optimize performance: With access to the data provided by an air compressor monitoring system, users can use the collected data to tweak compressor control settings so that equipment runs under optimal conditions, saving energy and providing enhanced performance of the system.
- Increase equipment lifespan: Because the remote equipment monitoring system alerts users to problems such as rapid cycling, excessive power consumption and oil levels, technicians can attend to these issues before they cause serious damage, ensuring a longer lifespan for the air compressor.
Quincy Air Compressor Remote Equipment Monitoring
The new ECONTROL+ air compressor monitoring system from Quincy Compressor is a central air compressor controller that allows users to monitor up to ten compressors, regardless of brand. System capabilities expand beyond the compressors to include ancillary equipment such as dryers, PDP sensors, flow meter and inline filters to provide full visibility of the air compressor control room. ECONTROL+ is also embedded with Quincy’s ICONS, which provides remote monitoring of the health of all connected equipment to help maximize uptime and productivity, while minimizing unplanned downtime and associated expenses.
Proven benefits of the Quincy Air Compressor ECONTROL+ remote equipment monitoring system include:
- Synchronized preventive maintenance visits help reduce the number of service interventions, minimizing maintenance costs.
- Lower energy costs as reduced pressure bands minimize energy consumption.
- Reactiveness to breakdowns because compressors can adapt to make sure there is no downtime.
- Ease of use as the status of all machines can be monitored from one compressor control screen.
For more information on the benefits of air compressor monitoring systems or to learn more about the Quincy air compressor ECONTROL+ system, please contact JHFOSTER, a Tavoron Company, today.