Long Live Your Air Compressor
Air compressors serve as the heart of the compressed air system in many industrial facilities where they likely power everything from air-operated tools to valves to automated equipment. While proper preventive maintenance can go a long way toward keeping the heart of your operation beating for years to come, air compressors will eventually need repair and/or replacement. This blog will look at the life expectancy of air compressors, provide tips on how to increase their lifespan and discuss the pros and cons of repair versus replacement.
Air Compressor Life Expectancy
While air compressors are long-term investments, even a well-maintained compressor will eventually wear out. However, the true life expectancy depends heavily on the type of air compressor, how many running hours it is used in the facility and how well it has been serviced.
Keeping in mind that air compressor lifespan is measured in operating, or running, hours versus years, as some facilities operate the equipment 24/7, while others may only use it 8 hours a day, rough estimates for common air compressor types range widely from 50,000 to 250,000 hours, as follows:
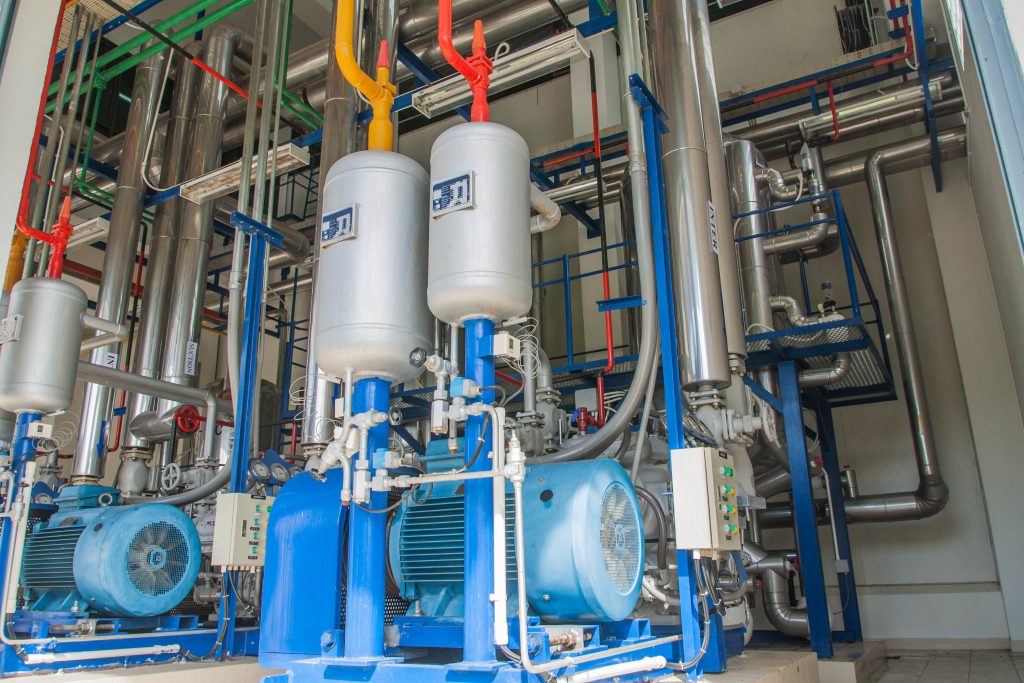
- Reciprocating air compressors average about 50,000 hours of life.
- Oil-free rotary screw compressors will likely achieve 70,000 hours.
- Traditional rotary screw air compressors can last 100,000 or more hours.
- Centrifugal air compressors may run as many as 250,000 hours over the lifespan.
That said, industry figures suggest that the average industrial facility replaces its air compressor about every 10 years.
5 Ways to Increase Air Compressor Life Expectancy
Regardless of air compressor type, performing regular maintenance is the best way to ensure the longest possible operational life. Here’s what you must do in order to achieve the fullest service life:
1. Regularly Change Filters. The components of the air compressor are protected from dirt and debris contamination by filters, as a result they can become clogged if they aren’t changed often enough. This will cause the compressor to work harder to operate, decreasing the efficiency of the system, raising electric bills and, ultimately, resulting in wear and tear on the air compressor and its components. Frequent filter changes can help prevent costly energy consumption while also extending the operating life of the air compressor.
2. Maintain Proper Oil Levels. air compressors must be properly lubricated to function. If not, friction and wear will likely result, reducing the life of the air compressor, making checking oil levels essential to proper operation. Experts suggest checking oil levels daily and, if the oil level is below the halfway mark, top up the oil before running the compressor to avoid damage.
3. Check for Leaks. Common to air compression systems, air leaks can shorten the lifespan of an air compressor because leaks force the compressor to work harder to maintain air pressure levels, which leads to premature wear and tear. Regular inspections can help you find leaks, which should be addressed immediately to ensure proper operation. As an added bonus, tending to leaks will also make the system more energy efficient.
4. Provide Adequate Ventilation. Air compressors generate a lot of heat during normal operation and, if not properly ventilated, the compressor can overheat, resulting in equipment damage and reducing operating life. To prevent premature failure due to overheating, be sure to check the coolers regularly and clean them as needed, ensure that the room housing the air compressor is properly ventilated with ducts or fans and that there is enough clearance around the air compressor to allow air to circulate. If possible, monitor the compressor room temperature to be sure it is between 50°F and 85°F – the ideal temperature range for operation.
5. Don’t Neglect Repairs and follow the manufacturers recommended maintenance schedule. No matter how small a leak or minor a problem, promptly servicing the air compressor will prevent downtime and unnecessary wear and tear on the air compressor and proper maintenance will go a long way to increasing the overall life expectancy of the equipment. So, if you notice an issue with the compressor, address it as soon as possible because even minor problems will lead to bigger, more expensive ones down the road, including complete failure and replacement.
Repair or Replace?
Deciding whether to repair or replace an industrial air compressor can be a complex decision, so it should include an in-depth analysis of the cost of each option, the pros and cons of repair versus replacement and the criticality of the equipment to the facility’s overall operation. Generally speaking, repair is likely the less expensive option and may be the quickest solution if the goal is to be up and running as soon as possible. Repair will also not require any changes to the compressed air system or its components.
However, if the air compressor is old or near the end of its anticipated operational life, the equipment may continue to experience breakdowns and failure, incurring frequent repairs and service, making replacement the better option. Especially if the air compression system is critical to operations, replacement may provide peace of mind and ensure trouble-free operation going forward. An added bonus is that newer air compressors have modern technology, which may help increase efficiency and reduce electricity costs.
Keep in mind that replacement will be a more costly option, may take longer to install and may require modification of the existing system layout or components as some may be incompatible with the new air compressor model.
JHFOSTER representatives can help you decide whether it’s time to repair or replace your air compressor and are available to provide assistance with maintenance programs, as well as air compressor selection.