Industrial Power Systems Best Practices for Automation
As manufacturing companies continue to add robotics and automation systems throughout their facilities, having a reliable industrial power system is becoming more and more critical to the success of electrical automation projects. This blog will discuss the importance of power quality for industrial automation and provide best practices for efficient and effective factory power systems.
The Importance of Reliable Power Quality in Robotics and Automation
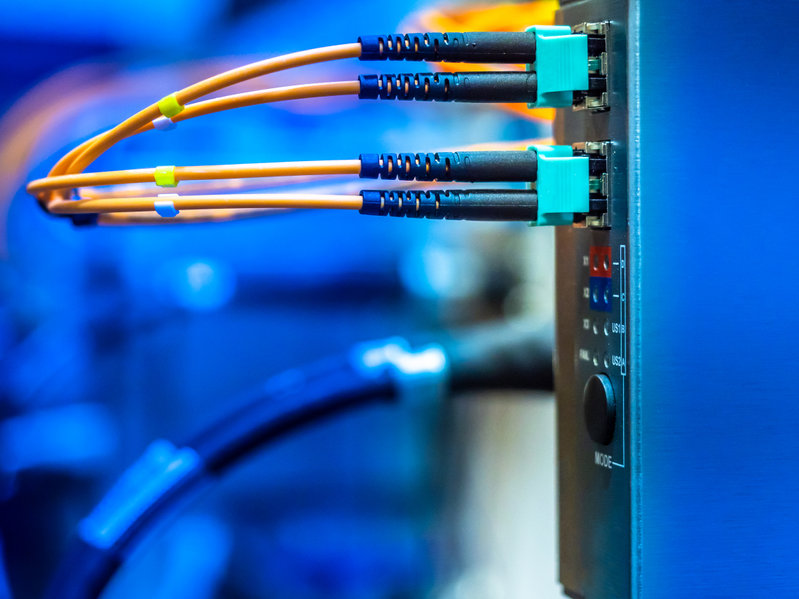
As the manufacturing industry adopts more robotics and automation and integrates Internet of Things (IoT), Artificial Intelligence (AI) and Machine Learning (ML) technologies into their electrical automation projects, the demand for reliable factory power solutions continues to grow.
Manufacturers that rely on electrical automation must maintain a stable factory power supply as even a momentary electrical issue can result in significant problems, such as equipment failures, production delays, data losses and safety hazards. And, while reliable power quality helps eliminate downtime and potential hazards caused by interrupted electrical service, there are other motives for ensuring that the factory has a system that, at the very least, meets the minimum power requirements.
As a matter of fact, having stable factory power helps:
Minimize downtime | Even a momentary glitch in power can cause automated equipment and robots to come to a sudden stop that results in costly downtime and productivity losses. Effective power quality minimizes downtime by providing an uninterrupted power source to critical electrical automation infrastructure. |
Extend equipment life | Frequent power fluctuations and sudden stoppages can result in wear and tear on robots, automated equipment and system components, so ensuring a stable supply of factory power helps prevent equipment damage and extends the life of plant assets. |
Prevent data loss | As the manufacturing industry embraces IoT technologies, control systems collect and manage large amounts of critical data. However, if there is a glitch in power delivery, sensitive data can be lost or corrupted. While maintaining data is important in all industries, it is especially important in highly regulated industries such as pharmaceutical and medical device manufacturing where data integrity is crucial for compliance. |
Increase safety | Sudden power glitches can result in the loss of safety systems and electrical safety devices such as light curtains and emergency stops. Ensuring a stable factory power supply is crucial to the safety of operators and other personnel. |
Enhance reliability | As industrial automation relies on a continuous source of power, any disruption in electrical delivery results in downtime and wear and tear on equipment. Having a stable industrial power system ensures reliability and functionality of equipment and the automation infrastructure, reducing the risks associated with power-related downtime, data losses and safety measures, boosting factory reliability and operational effectiveness. |
Criteria for Effective Industrial Power Systems
Having a steady and stable source of factory power ensures seamless operations, optimal performance and overall effectiveness of electrical automation equipment and robotics. Understanding the criteria for effective power quality, allows manufacturers to safeguard their operations, equipment, employees and overall profitability.
While the criteria for industrial power systems varies depending on the industry and electrical automation systems within a plant, there are some basic criteria for ensuring a reliable industrial power system.
The essential criteria for effective factory power include:
Power quality
The electrical supply should offer stable voltage levels that sufficiently meet the minimum requirement power supply for the facility.
Consistency and stability
The factory power source must provide consistent power output to all connected equipment and devices. Voltage level regulation and overload protection are critical components of a stable industrial power system.
Reliability
Industrial power systems must withstand challenging industrial environments so they reliably provide power without interruption.
Safety
Industrial power systems must comply with safety standards and government regulations to avoid safety and electrical hazards.
Efficiency
Efficient factory power systems reduce energy waste, offset the facility’s carbon footprint and minimize operational costs.
Scalability
As manufacturers continue to add more electrical automation to their plants, factory power systems must be scalable in order to manage the growing electrical demands.
Six Best Practices for Industrial Power Systems
There are some best practices to help ensure a consistent, stable, effective and efficient power supply that will help maximize the functionality and optimize operation of industrial robots and electrical automation equipment.
Industrial power system best practices include:
- Understand power requirements: Different facilities have different needs, so understanding the specifics of your factory power requirements will help ensure that the right equipment is selected and in place.
- Implement surge protection: Power surges can damage electrical automation equipment, sensitive devices and components. The installation of surge-protecting devices can help prevent downtime, reduce maintenance requirements and extend the life of assets by protecting them from sudden spikes in voltage levels and ensuring a stable flow of factory power.
- Install back-up power: Uninterruptible power supplies are systems that provide immediate power during outages. Back-up power supplies provide manufacturers with the necessary time to shut down equipment during an unplanned outage so it is not damaged and valuable data is not lost or corrupted.
- Select high-quality components: Investing in high-quality power supplies and components from trusted suppliers helps reduce the risk of failure, extends time between maintenance intervals and ensures optimal operation of the industrial power system.
- Testing and maintenance: A regular schedule of testing and maintenance of the electrical system will ensure that the factory power system and its components are operating properly and efficiently and will allow any minor issues to be identified and resolved before causing downtime or inefficiencies.
- Training: Operators and maintenance technicians should be properly trained in the layout of the electrical system, its maintenance schedule and emergency procedures.
High-speed and precise robots and automation systems demand a stable supply of electricity. Understanding the facility’s voltage level requirements and other electrical system criteria, following industrial power system best practices and purchasing high-quality components from a trusted supplier experienced in electrical automation systems will help safeguard the efficiency and effectiveness of factory automation. For more information on power supplies for industrial robots and automation systems or help determining your electrical requirements, please contact JHFOSTER, a Tavoron Company, experts today.