Choosing the Right Compressed Air Tubing for Pneumatic Applications
Compressed air is used in thousands of applications in industry. And, while much focus is placed on the big-ticket components within pneumatic systems, compressed air tubing isn’t something that gets much attention. Despite this, it is an essential part of pneumatic systems because it delivers air from the main compressed air distribution system to where it is needed, thus enabling efficient and effective operation of air-driven equipment and tools.
This blog will explore different types of plastic tubing for pneumatic systems, the advantages and disadvantages of each and provide guidance on how to select the best pneumatic tubing for an application.
The Role of Compressed Air Tubing in Pneumatic Systems
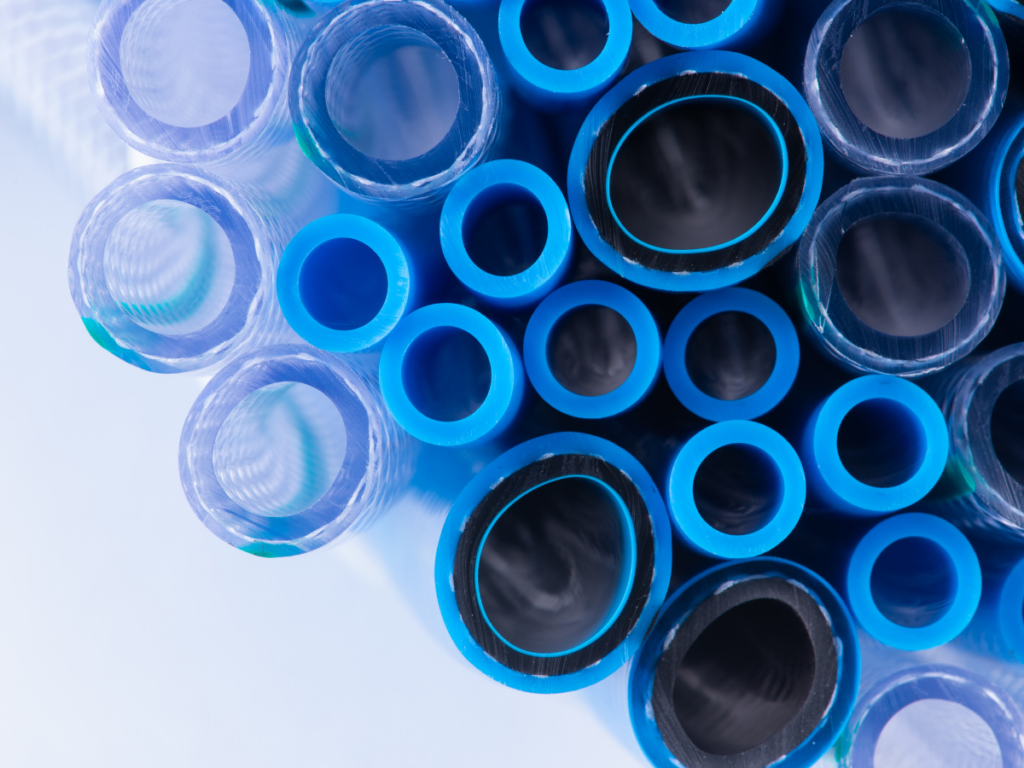
Compressed air tubing is generally used to distribute compressed air throughout pneumatic systems within machines, tools, and other point of use applications. Pneumatic tubing connects to system components via fittings that are designed for secure and leak-free delivery of compressed air.
The efficiency of a pneumatic system can be improved or impaired by the type and size of compressed air tubing that is selected because it is key to how effectively the compressed air can move through the system to the actuators, valves, tools and equipment used in the application.
A Look at Plastic Tubing Types
Because there are so many different pneumatic systems, there are different types of tubing for compressed air and each material has advantages and disadvantages that make it more or less suitable for an application.
While most pneumatic tubing is essentially plastic tubing, the specifications of the application should determine which type of plastic material will provide the highest level of air delivery efficiency. Here, we will explore a variety of plastic tubing types, including poly tubing, PVC tubing and nylon tubing, as well as the pros and cons of each.
The advantages and disadvantages of the three most commonly used types of plastic tubing are as follows:
Poly tubing | Among the choices in poly tubing are polyethylene and polyurethane. Polyethylene tubing is an economical choice and is suitable for low-pressure applications. It is non-corrosive, easy to install and well suited for most push-in type pneumatic fittings. However, it is prone to kinking and has a limited temperature range. Polyurethane tubing is strong, flexible, durable and resistant to kinks. Durometer must be considered when determining compatibility with the type of fittings being used and as with polyethylene, maximum operating pressure is directly related to temperature. |
PVC tubing | While PVC piping is generally rigid, PVC tubing is flexible (though not as flexible as poly tubing types) and kink resistant. It offers a wide temperature and pressure range. It is also easy to sterilize, so it’s a good choice for sanitary applications. |
Nylon tubing | Lightweight and better than other materials for higher pressures and temperatures, nylon tubing is durable and tough. However, nylon tubing is not as flexible as PVC tubing and polyurethane tubing and prone to kinking. |
Because compressed air tubing impacts the efficiency of pneumatic systems and because it can present a safety hazard if it is not properly rated for the pressures, temperatures and potential exposure to chemicals present in the system, it is critical to purchase plastic tubing from a reputable supplier, such as Freelin Wade, who makes clear the temperature ranges, pressure ranges, chemical resistance and other pertinent information.
Selection Criteria for Compressed air Tubing
In addition to determining which tubing material is the most suitable for the pneumatic application, it’s also important to know that plastic tubing for compressed air is specified by the outside diameter (OD), and inside diameter (ID). The size should be large enough to handle the flow rate of air to promote efficiency and prevent pressure drop. However, going with too large an ID may create bulk and slow response within the pneumatic system, so be sure to find the sweet spot for the application.
Aside from material type OD and ID, there are some other guidelines for choosing the best plastic tubing for safe, effective and efficient air delivery.
Note the following application requirements when choosing plastic tubing:
- System operating pressure: It’s important to know the operating pressure of the pneumatic system and ensure that the selected tubing material can handle the pressure because each type of plastic tubing – even tubing made of the same material – can have different pressure ratings. Choosing compressed air tubing that can’t withstand the operating pressure may result in system failure, as well as safety issues.
- Application temperature range: Pay attention to the temperature range in which the pneumatic system operates. Not all plastic tubing can handle extreme temperatures. Some materials may crack at low temperatures, while others will soften at high temperatures. Selecting an inappropriate tubing material may cause system failure.
- Location and environment: If chemicals, UV light or extreme pressures or temperatures are present, it’s important to take note and ensure that the compressed air tubing is resistant to the existing conditions. Choosing inadequate plastic tubing may result in system failure.
- Safety and other standards: In some applications, pneumatic tubing must meet specific industry standards to ensure that it doesn’t pose safety hazards or contamination issues. Standards may apply to compressed air tubing used in food, drug and medical device manufacturing. Fire hazards and chemical resistance standards may also apply in certain applications. Also of note is that compressed air tubing should include a safety-factor rating that relates to the burst pressure of the tubing.
Compressed air is an essential utility in industry, but it can be powerful, so it is important that compressed air tubing can withstand the operating pressure and temperature range of the pneumatic system and that it can resist any chemical or environmental conditions that may be present to avoid safety hazards. It is also wise to choose the plastic tubing type and size that is most suitable for the application itself to ensure the most efficient and effective operation. The experts at JHFOSTER and Freelin Wade are ready to help you find the best plastic tubing for your pneumatic application.