Best Practices: Commissioning PLC Controllers in Complex Manufacturing
Complex manufacturing involves the production of large quantities of finished goods in the most time- and cost-efficient manner and often requires the use of multiple automated systems and PLC controller brands. If individual PLC controllers are not integrated into a single SCADA system, there may be issues with plant operations as independent PLC controllers will not be coordinated or able to communicate with the others within the same manufacturing environment.
This is one reason, integration of PLC and a SCADA system are essential for successful plant operations in complex manufacturing environments. This blog will outline some of the best practices for these situations and provide a case history that highlights the benefits of this type of project.
The Importance of Integrated Control in Complex Manufacturing
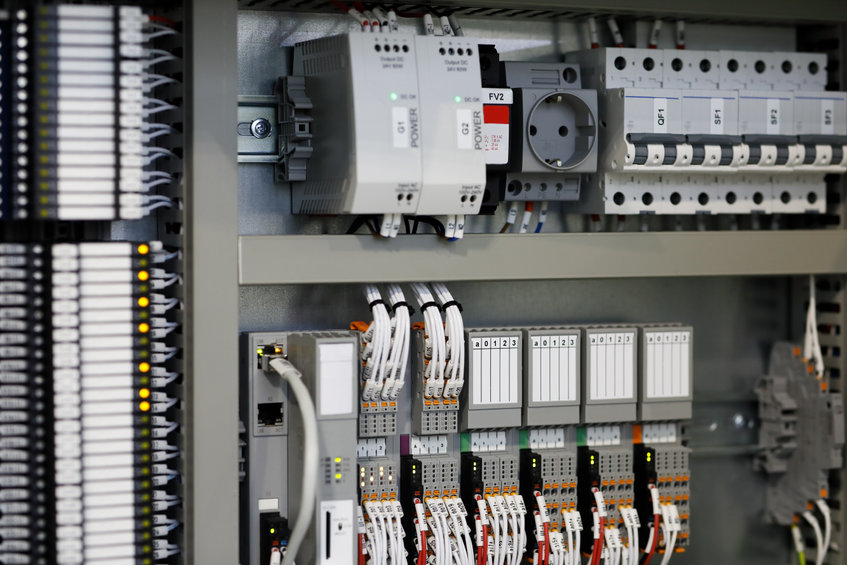
In traditional control systems, “islands of automation” were the norm. These disparate pockets of data were the result of independent PLC control panels that did not have the ability to communicate with other PLC controllers in the same manufacturing environment, creating a situation where collected data and information was not shared between equipment or technologies within the same facility.
However, as manufacturing complexity continues to grow as more automation is added, integrated control systems are becoming a necessity because they encourage the flow and exchange of operational and manufacturing data between equipment, technologies, networks and other sources, essentially synchronizing plant operations across the entire facility and business.
4 Steps to Commissioning Integrated PLC Control Systems in Complex Manufacturing
In an integrated system a well-designed network of PLC controllers replaces the previous islands of automation so that all data and information come together to provide a clear picture of plant operations. Although PLC controllers should be integrated in complex manufacturing environments, integration is not easy and the scope of the project will be guided by the business goals, the current plant operations, equipment and other factors. However, there are four best practices that will make any integration project go more smoothly, including:
- Identify the scope/goals of the project: A detailed understanding of the objectives of the integration project is imperative. This includes defining the functional and performance requirements of the integrated control system, the anticipated interfaces and communication methods between control systems and the overall goals and expectations of the integration project.
- Develop a plan: A commissioning plan should be developed by all key personnel, including plant owners, systems integrators and end users. The plan should outline the steps, tasks and schedule of the project, as well as test procedures that will verify and validate the newly integrated control system, ensuring that the integration successfully satisfies project objectives.
- Testing the control system: Once commissioning has occurred, testing allows validation of the performance of the system integration. Testing should be conducted on individual components, subsystems and the overall system functionality under various operational conditions. Issues should be identified, reported and corrected during the testing phase.
- Documentation: Records about the integrated control system should be maintained to provide historical information about the creation of the system, test results, functionality issues, etc. This type of documentation can be used for troubleshooting purposes and to provide guidance for future users of the integrated control system.
PLC Controller and SCADA System Integration Case Study
The following case study demonstrates the benefits of employing best practices when integrating PLC controllers in a complex manufacturing facility.
A large industrial bakery needed to bring together information including production data and plant functions such as HVAC, water and utilities, from multiple PLC controller brands to provide an overall view of the manufacturing environment that could be used to optimize plant operations.
The bakery hired CELCO to develop standards and integrate PLC from 35 different equipment manufacturers into a single SCADA system.
SCADA system includes recipe management, plant-wide alarming, a process historian and a operator graphical interface. The bakery owners required that the system monitor and display key operational metrics, equipment status, recipe progress and batch lot tracking and provided a direct data connection to its ERP system for reporting purposes.
The bakery also required programming and commissioning of the plant utility control system, followed by integration into the SCADA platform.
CELCO developed project standards for information exchange between multiple PLC platforms and the SCADA system, created interface maps to each PLC control panel and generated SCADA graphics. On-site verification and equipment commissioning was performed.
Celco supplied a standardized approach for the PLC to SCADA information exchange that the client could use when procuring new equipment and provided a single source for plant control information throught the SCADA system. A centralized process and equipment data repository was created with the ability to interface with other systems, such as the bakery’s ERP system, so that up-to-date information could be used for decision making.
The end result was a highly automated and fully functional food manufacturing facility that now has the ability to leverage its process and equipment data in a way that provides benefits to the business. Plant operations, automation philosophies, procedures and products have been streamlined and standardized. More detailed information on this and CELCO’s other integration projects can be found here.
Commissioning control systems in a complex manufacturing environment is crucial for optimization of plant performance, but it can be challenging and the assistance of an experienced systems integrator is essential. Experts at CELCO, a Tavoron company, are available to help guide and facilitate the project. Reach out today.