Are You Using Robots for Machine Tending Yet?
Manufacturers are always looking for advantages that will help them remain competitive. As a result, many have been using robots for machine tending tasks, which tend to be dull, dirty, and/or dangerous for human workers to perform.
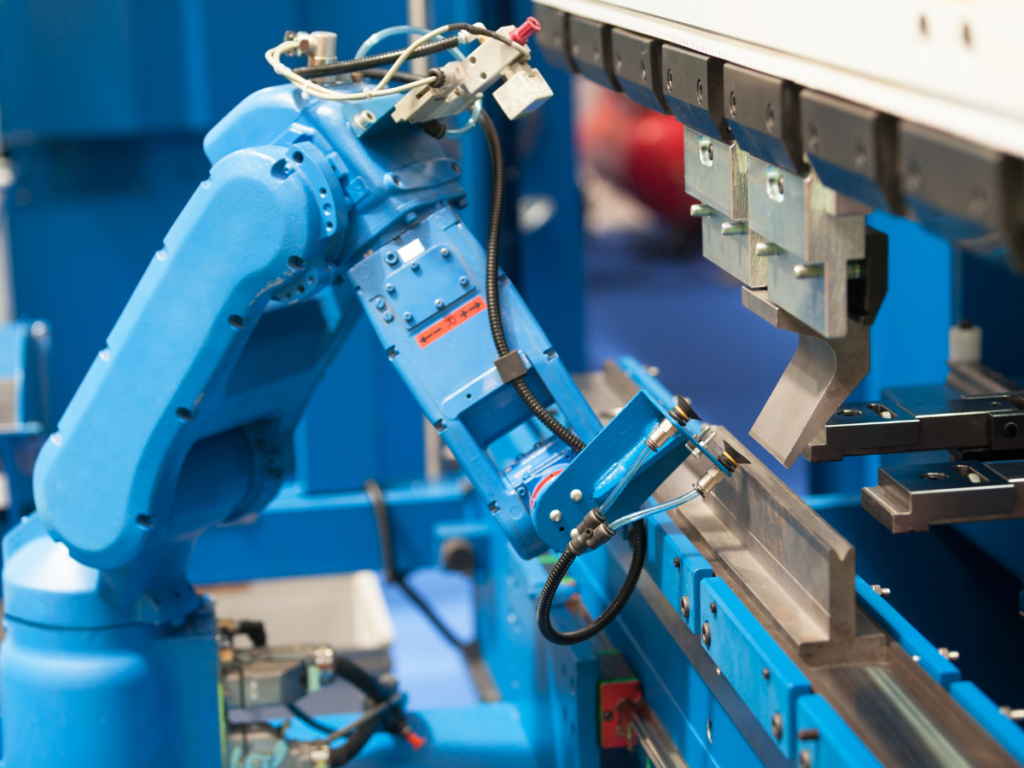
Why is Robotic Machine Tending so popular?
Using robots for machine tending frees up human employees to perform more complex tasks while reducing the risk of injuries caused by the lifting, bending and twisting motions associated with machine tending.
Robots are used to load and unload CNC machines, lathes, mills and presses. They are also used for grinding, injection or compression molding, welding, etching, raw or scrap material handling, stamping, punching, trimming, forging, hazardous material handling, quality control and inspection, furnace tending, and upstream and downstream assembly operations.
Humans | Robots |
Work 8 hours per day, 5 days per week, and need breaks, holidays, and vacations | Work up to 24 hours per day, 7 days per week |
Inefficient, inaccurate motions | Efficient, accurate motions |
Can only move as fast as they are comfortable and confident | Can move as fast as the physics will allow |
Easily bored, forgetful, and make mistakes | Never distracted, and always do exactly what you tell them to do |
Difficult to hire and retain | Available for purchase |
Require wages, insurance, and benefits | Require electricity and come with a warranty and customer support |
Easily injured | Built to survive |
Sometimes sick | Sometimes need maintenance |
Have creative minds that should be used for creative problem solving and decision making, such as programming CNC machines and their robotic tenders | Do not have creative minds, and should be used for dull, dirty, and/or dangerous tasks such as loading, unloading, cleaning, inspecting, assembling, and packaging parts |
What Type of Robot is Commonly Used for Machine Tending?
6-Axis industrial robots and collaborative robots (“cobots”) are commonly used for machine tending because of their versatility and the wide range of end effectors available which gives them excellent dexterity. Cobots are the robot of choice in many machine tending applications
because they are designed to meet stringent ISO safety requirements for human-robot cooperation, sometimes without the need for physical guarding, depending upon the specific risk assessment. Cobots offer faster deployment, simplified programming, smaller footprints, and greater flexibility than industrial robots.
What’s Inside a Robotic Machine Tending Cell?
- The process equipment (i.e., CNC machine, mill, lathe, press, etc.).
- A holding area or conveyor for raw materials.
- The raw materials/parts that will be processed.
- The robot/cobot controller.
- The robot/cobot arm.
- End-effector (a.k.a., “End of Arm Tooling”), which serves as the “hand” of the robot and is sometimes custom-built for the application.
- An area for the finished parts to be placed or conveyed away.
- Etc.
Essential Criteria for Machine Tending Robot Selection
Specifications that should be prioritized when choosing a robot for machine tending:
- Application Details: Knowing what you want the robot to do and where it will be placed is critical when selecting a machine tending robot. It’s important to clarify each individual step in the process so that the robot meets all the criteria of the application.
- Robot Payload: This is the maximum load that the robot can handle in the working space. The payload includes the part the robot will handle, as well as the end-effectors.
- Reach: It is important to ensure that the robot offers enough reach.
- Repeatability: The ability of the robot to reach the same position each time it completes a routine. Because most machine tending applications require precision and accuracy, high repeatability is essential.
- Space and Footprint: The robot must be able fit and function properly within the designated footprint and avoid obstacles therein.
- End-effectors: Ensure that the gripper offers enough stroke to handle the largest part it will be picking up and the payload of the heaviest materials. Adaptive grippers with force-torque sensing are available to handle a variety of shapes and materials.
- Environment: In many robotic machine tending applications the operating environment plays a significant role in determining the proper equipment selection.
- Integration: Determine the requirements for integrating the robot to the machine for safe and efficient operation.
- Safety: A risk assessment should be performed to ensure safety standards and requirements are met.
With proper robot selection, robotic machine tending provides accuracy, high efficiency, and optimized throughput, and alleviates concerns about worker safety and retention, providing a competitive advantage for today’s manufacturers. To find the robot that is best suited for your machine tending operation, please contact JHFOSTER.