7 Questions to Ask When Choosing an Electric Actuator
Actuators are hidden within all types of machines and devices from industrial robots to automatic doors to cell phones. Because the function of an actuator is to enable movement by converting energy and signals into a mechanical force that pushes, pulls, lifts or otherwise moves parts of equipment and gadgets, actuators are an integral component in many motion control and automation systems.
Actuators are available in hydraulic, pneumatic and electric versions, with the main difference being how they are powered. Hydraulic actuators are driven by fluids, pneumatic actuators are energized by air and electric actuators are powered by electricity. Previously, electric actuators were often bypassed because they were more expensive, but as they have become more cost competitive, electric actuators are becoming a preferred method of actuation, allowing more applications to benefit from their distinct advantages.
Because they are driven by electricity, electric actuators are more environmentally friendly, efficient and cost effective in their operations. They also offer the ability to integrate power and control into one compact motion control unit, making them essential in small, complex applications. Many of today’s electric actuators also provide feedback directly from the motor and can automatically adjust and correct performance variations according to this feedback, resulting in greater accuracy and repeatability.
For these reasons, electric actuators are being selected for motion control applications with growing frequency, but deciding on the right electric actuator requires careful consideration. This blog will provide guidance on electric actuator selection to help ensure that the most suitable one is chosen for the application.
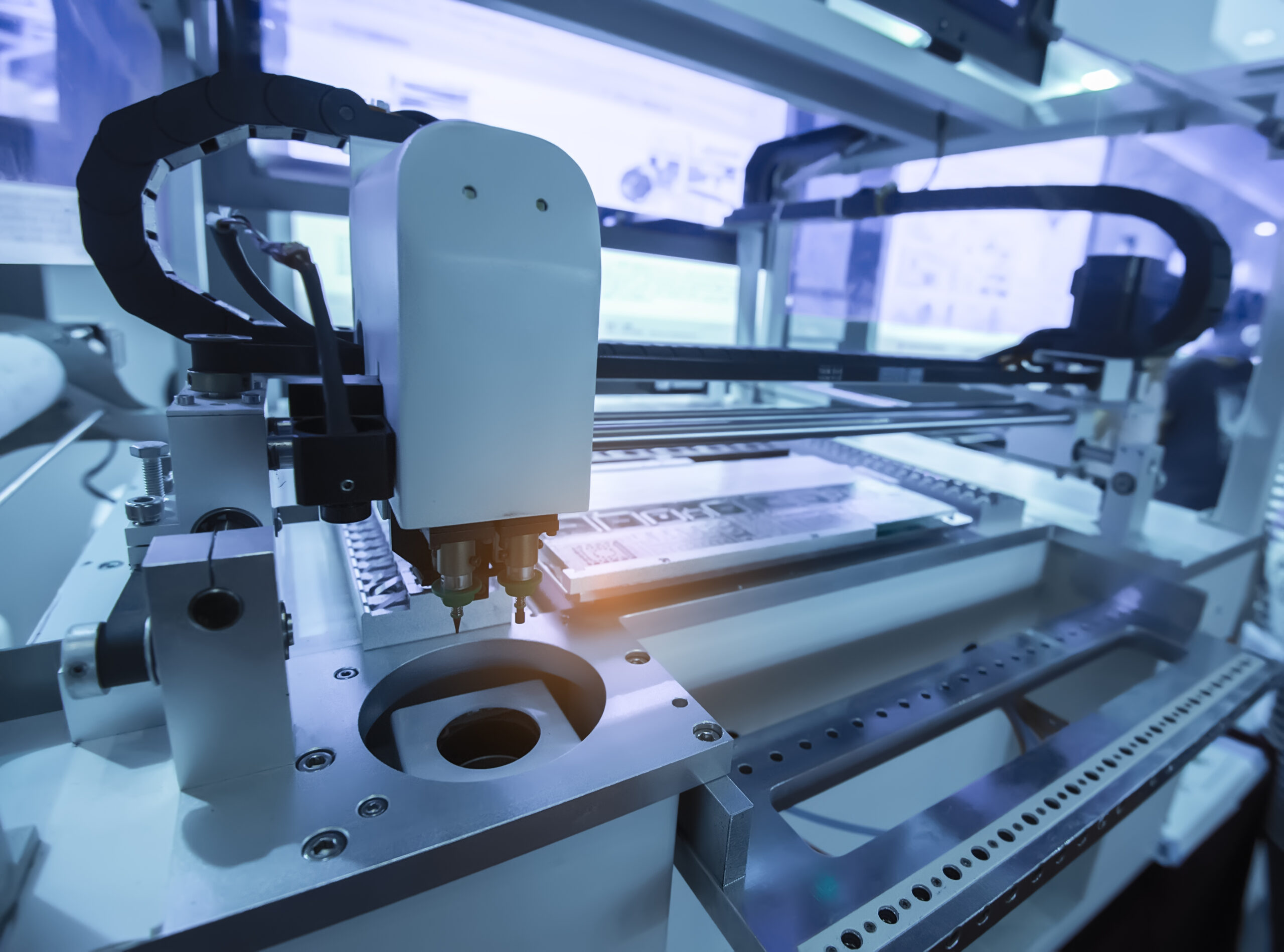
Electric Actuator Basics
Before discussing how to select an electric actuator, it’s important to understand how they work, as well as the various types of electric actuators and the available motion profiles.
Electric actuators rely on electricity to power a motor, which triggers internal components to move, providing mechanical energy and motion to the application. They are commonly available in three basic types: rod-style, rodless and rotary.
Rod-style actuators produce motion by retracting and extending a rod from the housing. As a result, loads are pushed or pulled by the rod.
As the name implies, rodless actuators do not have a rod. Instead, they transport the load via a guided carriage attached to a belt or screw, which provides support for heavy loads and offers a smaller footprint while providing a similar stroke length. They may be selected for heavy-duty or critical applications because there is no risk of a breaking or bending a rod and their compact construction makes them a good option when space is limited.
Further, electric actuators can provide two types of motion: linear and rotary.
Linear actuators convert electrical energy into linear – or straight line – motion. They are simple to install and the rodless types are suitable for operation in small spaces. They are well suited to applications that require precise control of acceleration and deceleration.
Electric rotary actuators offer a greater range of motion and the ability to stop the motion at multiple points. They are also well suited to applications that require precise control of acceleration and deceleration, as well as dynamic motion.
7 Questions to Ask when Choosing an Electric Actuator
Keep in mind that while there is an electric actuator to meet the needs of just about any motion control application, an actuator will provide optimal performance when it meets the specific requirements of the operation. Answering these six questions should direct you to the most suitable electric actuator.
- What Type of Movement is Needed? Does the application require simple straight-line motion or is a greater range of motion needed? If straight-line motion is needed, an electric linear actuator is the right call. If a more dynamic motion is specified, then an electric rotary actuator may be necessary.
- What is the Expected Load? Since the goal of actuation is to move a load, the weight of the load is one of the biggest considerations in the selection process as the actuator must be equipped to manage the load it is expected to push, pull or lift. Heavier loads will require more force and a more robust actuator.
- What is the Motion Profile? Next, it’s important to establish the necessary speed and force for the application. Keep in mind that the desired speed is a fundamental selection criterion as not all actuators provide high speeds. Moving heavy loads at fast speeds may result in premature wear and tear on the actuator, so each device has a speed and a load limit that should not be exceeded. The maximum stroke, or travel distance, should also be noted.
- How Accurate Does it Need to Be? Knowing the positional accuracy and precision demanded by an application is important to ensure that the electric actuator provides adequate accuracy for the job, but also so that the actuator isn’t more precise than it needs to be, which will unnecessarily increase the cost of the device. Typically, smaller and more complex applications require more accuracy, while heavy-duty jobs require less precision (but likely more force).
- What is the Anticipated Duty Cycle? Usually expressed as a percentage, the duty cycle of the electric actuator is the ratio of operating time to resting time of the device. The cycling rate may be expressed in seconds, minutes, hours, days or as operating hours per day. It is crucial information because it allows selection of an actuator that will provide the longest lifespan in the application.
- What are the Installation Requirements? First and foremost, if there is a risk of fire or explosion in the work environment, an electric actuator is NOT the proper choice. It is also important to know the temperature requirements, as well as any contaminants that may be present, so the proper sealing mechanisms are provided. Available installation space is another important consideration as integrating a large electric actuator into a small space will be a problem. Mounting of the motor and orientation of the actuator requirements should also be considered. Motor mounting configuration options are typically in-line, L-shaped or parallel. Actuator orientation can be horizontal, vertical or somewhere in-between and is a very important consideration for correct actuator sizing and safe operation. Selection of the right mounting configuration will impact installation, space requirements and performance as an electric actuator that is kept securely in position will operate better and with greater efficiency and reliability.
- Safety. Safety also plays a critical role when choosing which electric actuator to use. Brakes and other options may be required to meet safety standards and requirements.
While electric actuators provide many advantages in motion control applications, proper selection will ensure optimal performance, as well as reliability and longevity in the application. Representatives at JHFOSTER can help you answer the six questions above and provide additional guidance when selecting an electric actuator.