5 Ways Automated Feeding Systems Support Smart Factories
Automated feeder systems are an integral part of manufacturing as they make the task of getting components onto the assembly line or into the process more efficient than manual parts feeding, which is incredibly time consuming.
However, today’s automated feeding systems not only speed up the process of placing components into the manufacturing process, but they support the digital transformation of the manufacturing industry thanks to the inclusion of robotics and machine vision. The addition of these modern technologies helps to streamline operations and increase throughput while cutting costs associated with human error, waste, bottlenecks and downtime, which are the major goals of today’s Industrial Internet of Things (IIoT) Industry 4.0 efforts.
This blog aims to provide information on modern automated feeding systems and how they maximize productivity and minimize costs to align with smart factory initiatives.
What is an Automated Feeding System?
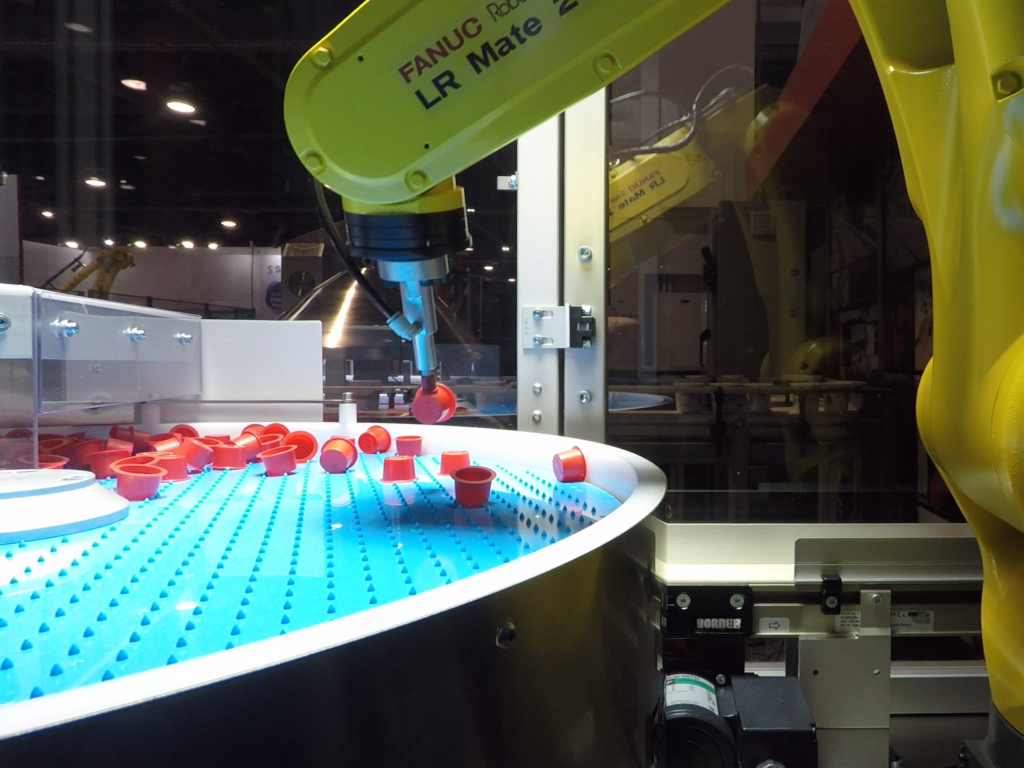
Today’s automated feeding systems consist of a flex feeder, an integrated vision system and a robot that seamlessly work together to align and feed parts, regardless of their shape, in manufacturing operations.
Using automated feeder systems, components are dropped onto a feeder surface where a robot equipped with machine vision accurately identifies properly oriented parts and, using pick-and-place functionality, quickly and consistently picks them up and places them on the production line.
Thanks to the ability to program automated feeding systems for multiple parts, many different components can be run on the same feeder with minimal effort. In addition, today’s automated feeder systems are compatible with most parts, including silicone, and multiple programs can be loaded into the system to permit efficient and effective switching between parts and production runs.
Integral Components of Automated Feeding Systems
The addition of robotics and machine vision to traditional bowl feeders and other feeder systems created automated feeding systems that provide the agility to keep pace with today’s more flexible manufacturing dynamics that require the handling of multiple components to accommodate the trend toward variable production runs and to support smart factory initiatives.
The following components can be integrated with flex feeders to create an automated feeding system that meets the needs of today’s digital transformation in the manufacturing industry:
Machine vision
Machine vision systems can be integrated with flex feeders and robots to oversee part selection, proper orientation and inspection of placed components. Within an automated part feeder system, machine vision analyzes visual data to ensure selection and orientation of the parts, as well as movement of the robotic arm and its grippers. The addition of machine vision allows the automated part feeder to accurately select only parts that are properly aligned and ensure that they are oriented on the feeder platform. Machine vision systems may also be programmed to inspect each part so that faulty components are not included in the assembly process, which helps minimize defective products.
Robots
Typically, robots are integrated with the flex feeder and machine vision. Robots with specialized end of arm tooling or grippers pick up and manipulate the parts as directed by the machine vision and automation programs and place them onto the feeding platform. Not only can robots increase the efficiency and accuracy of part feeding operations, but they also provide great flexibility to the process as they can be programmed and re-programmed to manage a variety of tasks, making them suitable for batch production or for facilities with frequent changeovers.
Modern Feeder Systems Support Smart Factories
Since the goals of Industry 4.0 and the digital transformation of the manufacturing industry are to increase efficiency, become more agile and improve quality, while cutting costs, modern automated feeding systems that feature machine vision and robots are essential to smart factory efforts.
Automated feeding systems provide the following five smart factory advantages:
- Increased efficiency and speed: Automated flex feeders can handle high volumes of parts quickly and with high levels of precision, supporting the desire to increase efficiency and throughput.
- Flexibility: The ability to program and reprogram the robot, machine vision system and the automated feeding system to manage a variety of parts allows the flexibility and agility needed to support batch production and the trends toward smaller runs and customization in manufacturing. Traditional part feeders were limited in that they could only handle one type of part.
- Minimize manual labor: Manual part feeding was very hands on and time consuming and required constant human intervention. The next generation of feeder systems often required human intervention if bottlenecks occurred, faulty parts were being selected or parts were not being properly oriented. The addition of smart technologies such as machine vision and robots significantly reduces the need for human intervention, reducing the risk of introducing errors while increasing throughput. Removing the need for manual labor also decreases costs and introduces the possibility of 24/7 operations, which are major goals of the digital factory.
- Maximized quality: By including machine vision for inspection and analysis of selected parts and collaborative robots for fast precision, today’s automated feeding systems offer precise, consistent, efficient and reliable feeding of parts onto assembly lines, while also eliminating human error. The ability to precisely and accurately feed only “good” parts onto the assembly line means that quality control efforts will be maximized and scrap and waste will be minimized, improving product quality and reducing costs.
- Minimizing costs: By automating part feeding and ensuring higher levels of accuracy, consistency and precision with the addition of robots and machine vision, operational costs such as labor, waste and downtime can be significantly reduced, while throughput and quality control are increased, improving the bottom line.
The addition of smart technologies such as robots, machine vision and automated flex feeders to parts feeding operations supports IIoT Industry 4.0 initiatives in smart factories where efficiency, quality and cost-effectiveness are major manufacturing goals. To learn how today’s automated feeding systems can best support your smart factory efforts, please contact DevLinks, a Tavoron company, today.