The Evolution of Automated Bowl Feeders
As trends in the consumer market have changed, so have the automated technologies used in manufacturing facilities. Due to current preferences in the consumer market, which demand high-quality, customized products available at a low cost and in the shortest time possible, manufacturers are using smart and flexible automated production equipment to produce their goods. However, advances in part feeding systems initially did not keep pace with other automated industrial technology developments and have only recently caught up thanks to the integration of robotics and machine vision. This blog aims to discuss the evolution – as well as the significant benefits – of today’s automated bowl feeders.
The History of Automation in Part Feeding Systems
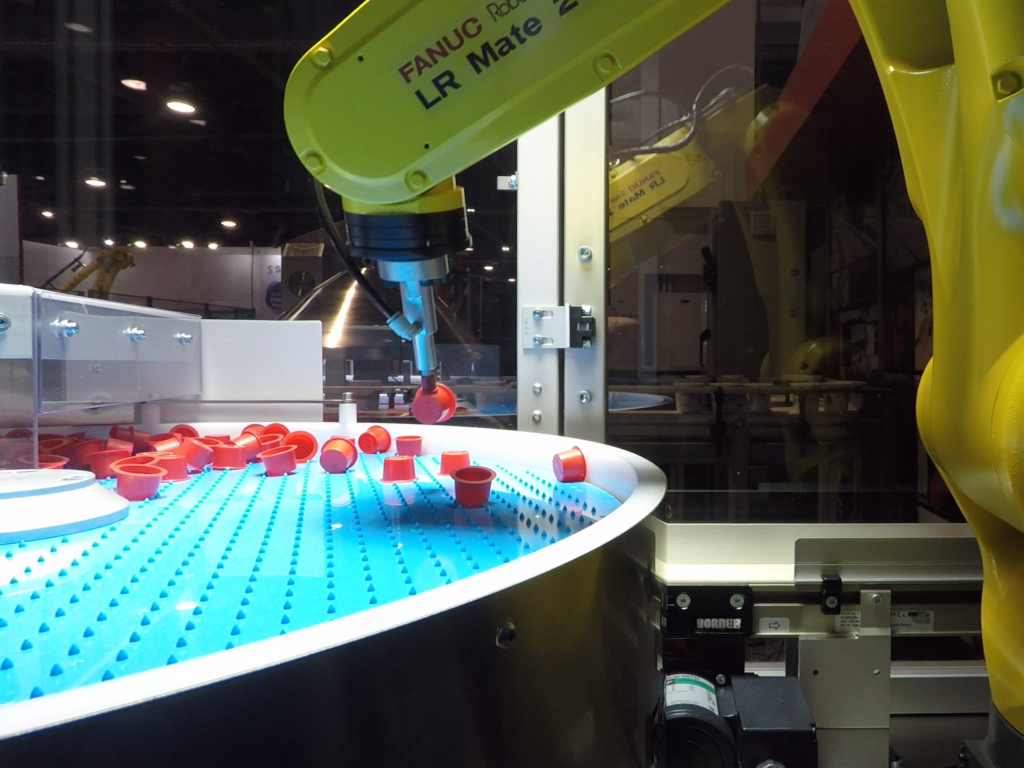
While part feeding was accomplished by hand in the earliest days of the manufacturing industry, this was too time consuming and inefficient to satisfy the needs of mass production, which led to the development of automated part feeders, such as bowl feeders.
Traditional bowl feeders relied on mechanical vibration or centrifugal force to sort and distribute parts to a production line.
These feeders, which were typically dedicated to a single production line, were successful in applications that manufacture large volumes of a single part; however, traditional bowl feeders tend to be part specific and are difficult to convert for use with a different product or production line. Because of this, manufacturers that run mixed or variable production must purchase several bowl feeders to accommodate their production requirements.
To eliminate the purchase of multiple part feeders and satisfy the current trend toward smaller, batch-like production processes, there was a growing need to develop an automated flexible feeder system. This was accomplished by integrating traditional bowl feeders with robotics and machine vision to create a feeding system that could successfully adapt to smaller production runs and variable parts to handle the demands of frequent batch changes.
What we have available today are automated flexible feeder systems that consist of a flexible feeder bowl, an integrated vision system and a robot that seamlessly work together to align and feed parts, regardless of their shape, in assembly and packaging operations.
In today’s flexible part feeding systems, components are dropped onto a feeder surface where a robot equipped with machine vision accurately identifies properly oriented parts, and using pick-and-place functionality, quickly and consistently picks them up and places them on the production line. Thanks to the ability to program modern feeding systems for multiple parts, many different components can be run on the same feeder with minimal effort. In addition, today’s flexible feeders are compatible with most parts, including silicone, and multiple programs can be loaded into the system to permit efficient and effective switching between parts and production runs.
These developments encourage the agility to keep pace with today’s manufacturing dynamic that requires handling multiple components to accommodate the trend toward variable production runs.
The Advantages of Modern, Automated Bowl Feeder Systems
Thanks to the seamless integration of advanced robotics and vision systems, today’s automated bowl feeder systems offer significant advantages over traditional bowl feeders, including:
- The ability to preprogram the feeding system for multiple components and parts, allowing manufacturers to efficiently accommodate variable production batches with the touch of a button versus purchasing several traditional bowl feeders.
- The accommodation of silicone parts or those with complex geometries using the same automated bowl feeder system, as well as the ability to pick parts without a specific orientation on the feeder surface increases the accuracy, efficiency and flexibility of the feeding system.
- A reduction in capital costs, floorspace and inventory can be achieved because modern flexible feeders can handle a variety of different parts in mixed and variable production facilities, so these manufacturers do not have to purchase and store additional part feeders to satisfy changing production lines.
- The incorporation of robotics and machine vision provides higher levels of overall efficiency as machine vision reduces the chances of errors and the use of robotics increases the speed. This combination of speed and accuracy maximizes the efficiency of part feeding and facility throughput.
- The use of machine vision in automated part feeding systems is also likely to lead to higher product quality. Not only does machine vision enhance accuracy and allow part feeders to select only properly oriented parts, but the system can be programmed to inspect parts at the same time to avoid the use of defective components, increasing the quality of the finished product.
Today’s automated and flexible bowl feeders have evolved into smarter technologies that enhance modern production lines, allowing manufacturers to keep up with quality and throughput goals and accommodate frequently changing or variable production batches to meet consumer demand for high-quality, customized products. To learn more about the benefits of modern flexible feeding systems, please contact DevLinks or JHFOSTER today.