Flexible Feeders Optimize Life Sciences Manufacturing Processes
Life sciences manufacturing is a complex business as the products, including medical devices, pharmaceuticals, biologics and other essentials for human life and patient care, are often delicate and require careful handling and precise production with little room for error. In the last 5 years, life sciences manufacturers realized they needed to optimize production time and reduce costs, so they began to adopt automation into their manufacturing processes.
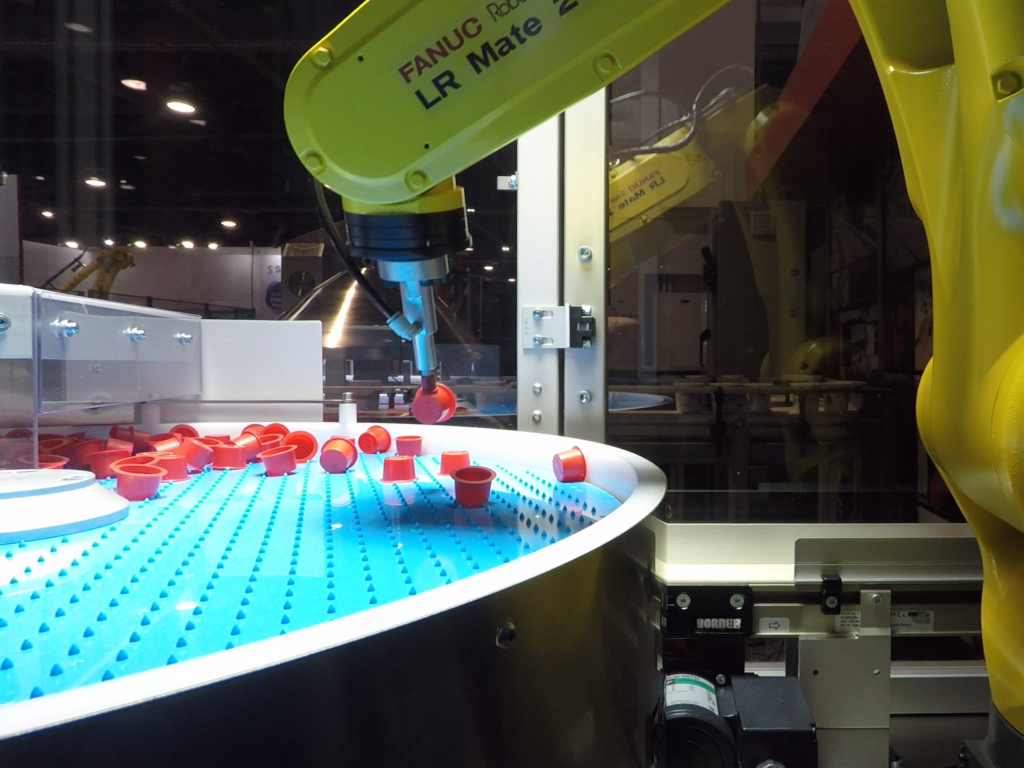
Flexible feeding systems, used for component feeding, are one of the technologies that can help life science manufacturers step up their game and meet the multifaceted demands placed on the life sciences industry. This blog will explore the challenges of parts feeding in the life sciences manufacturing sector and how flexible feeding systems with their versatility, speed and precision can help overcome these obstacles and optimize the manufacturing process.
Life Sciences Manufacturing Feeding Challenges
Life sciences products often feature delicate materials, are highly diversified and must be produced in a short time frame in a way that is cost effective.
Many of the products manufactured in this sector contain fragile components, which can be difficult for traditional parts feeders to separate, arrange and handle without causing damage in an industry that has zero tolerance for faulty products. Components may include anything from pharmaceuticals to plastic caps to silicone seals or rings to vials, bottles and jars to plungers and syringes, as well as other items that require gentle handling
Not only are life sciences and pharmaceutical products often sensitive, but the components may feature complex geometries and small sizes, which are difficult for traditional parts feeding systems to properly process.
Further, life sciences manufacturing and pharmaceutical manufacturing are often diversified businesses that demand the agility and flexibility to quickly change production from one item to the next. This means that parts feeders must be able to manage a variety of different part sizes, shapes and materials to provide efficient, cost-effective handling.
5 Advantages of Flex Feeders in Life Sciences Manufacturing
Flexible feeders, such as DevLink’s Automated Flexible Feeder System (AFFS), include a flexible feeder bowl, an integrated vision system and a robot, which work together to feed parts, regardless of their size or shape, in assembly and packaging applications.
With this automated system, parts are dropped onto a rotating disc where they are oriented and aligned for robotic pick and place. The robot is programmed to pick from different orientations, but always place on the same orientation. The system is compatible with most parts, including silicone, and multiple programs can be loaded to the system to permit simplified switching between parts. Automated flexible feeders can feed multiple types of components on the same feeder, providing efficiency and flexibility to handle a variety of parts and frequent product changeovers.
Flexible feeder characteristics provide five significant advantages when feeding components in the life sciences manufacturing industry, including:
- Gentle handling: Flexible feeding systems, such as DevLink’s AFFS, can handle and feed delicate life science, medical device and pharmaceutical components without damage thanks to the combination of a feeder bowl and orientation platform that are integrated with a vision system and robot equipped with proper end-of-arm tooling. In comparison, traditional feeders are rougher in material handling operations and increase the risk of damaging these sensitive parts.
- Versatility: As the name implies, flex feeders are designed to be flexible and versatile. The ability to process more than one type of part on the same feeder makes them suitable for mixed production, a necessity in the life sciences industry, which produces a variety of products. Flexible feeders are also able to handle silicone components, which is a difficult material for traditional feeders to process and one that is frequently used in life sciences manufacturing. Further, pre-programming for multiple parts simplifies product changeovers as it is accomplished with just the touch of a button.
- Improved product quality: The vision system provides flexible feeders with the ability to guide the robot on where and how to pick the product, increasing accuracy and consistency in life sciences manufacturing processes.
- Cost effectiveness: Because the same flexible feeder can be programmed to handle a variety of components, life sciences manufacturers do not need to purchase and store different feeders for each product they produce. This also reduces footprint and saves space on the manufacturing floor.
- Increased efficiency: Due to the fast pace and high demand for life sciences products, life sciences manufacturing processes must be highly efficient. Flexible feeders optimize efficiency as the arrangement of the system prevents jams, which are common with traditional bowl feeders, helping to decrease downtime and improve throughput. Additionally, the integrated vision system and robotic arm enable the system to orient the product. With an optional automatic tool change system, where the robot will go and pick the best end-of-arm tooling based on the product selection, the system can be pre-programmed for multiple parts. Retooling or changing out of traditional feeders for product changeovers is eliminated, reducing downtime and increasing throughput and efficiency.
With their delicate materials and complex and variable shapes, life sciences products necessitate component feeders that can gently, accurately and efficiently feed products into the manufacturing process. Flexible feeders, such as DevLink’s AFFS, provide a solution that overcomes the challenging requirements of the life sciences industry in an efficient and cost-effective way. To learn more about the role an automated flexible feeder can play in your life sciences manufacturing process, please contact DevLinks, a Tavoron company.