5 Trends to Watch in Electric Actuators
Actuators play an important role in motion control systems, robotics, industrial equipment and a myriad of other applications. Although traditionally considered to be the more complex choice, there has recently been an uptick in the use of electric actuators because they provide a host of worthwhile advantages over pneumatic and hydraulic models. This increased interest has driven innovation aimed at further improving the performance, efficiency and reliability of electric actuators and expanding their use into new applications. Here we’ll take a look at five important trends in the technology.
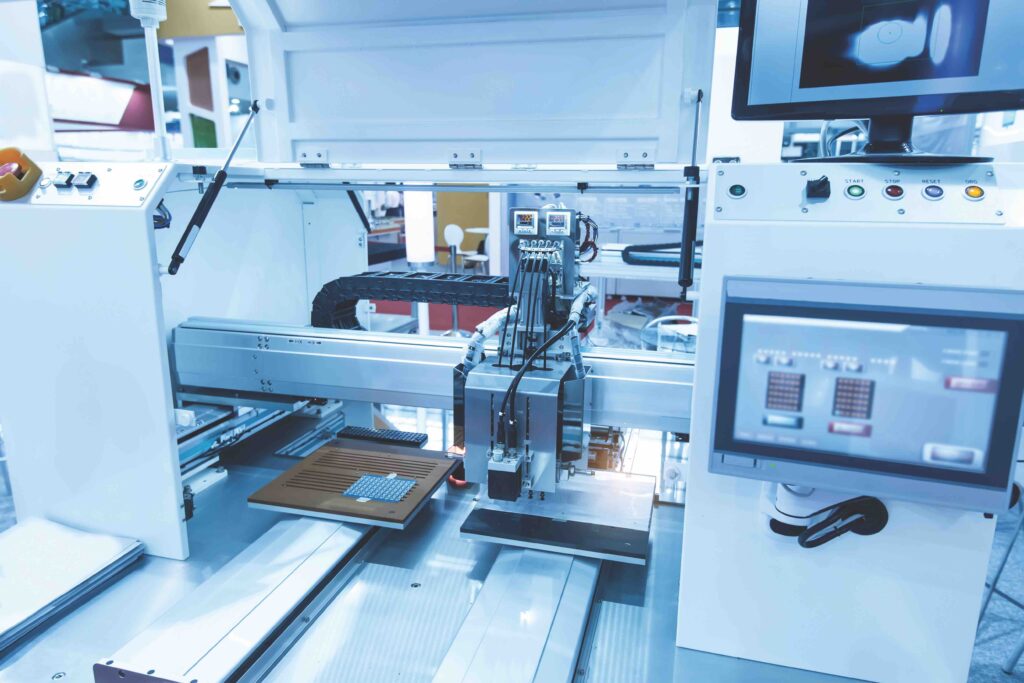
The Benefits of Electric Actuators
Before discussing the latest innovations in electric actuation technologies, it’s important to understand the difference between pneumatic, hydraulic and electric actuators, as well as the advantages provided by electric actuators that support their growing popularity.
Actuators serve as the muscle in many applications as their job is to create motion that moves machinery, robotics and the like. Actuators are available as pneumatically, hydraulically and electrically driven, so the main difference between actuator types lies in how they are powered; pneumatic actuators are driven by compressed air, hydraulic actuators are powered viapressurized fluid and electric actuators rely on electricity.
Both pneumatic and hydraulic actuators offer lower initial cost than electric actuators and provide ease of use. They also have significant advantages and disadvantages. For example, hydraulic actuators can provide high forces, but they are subject to fluid leaks, which can create costly environmental or product contamination issues. And, while pneumatic actuators are simple to use and less expensive, they are air powered, which is not energy efficient and sometimes difficult to control.
Electric actuators can be more expensive and are more complex than air- and fluid-powered actuators because they use voltage and current to convert the rotational force of an electric motor into motion. However, electric actuators can perform at higher speeds, provide greater precision and better efficiency than other types of actuators.
Additionally, because voltage and current are easier to control than fluid or air, electric actuators provide more precise control of speed and force and higher levels of accuracy than pneumatic and hydraulic models. Because of the enhanced precision and accuracy, electric actuators are also more capable of repeating specific motion profiles and are less likely to experience drift. And, thanks to data feedback capabilities, electric actuators can handle more complex motions, offer multi-point positioning and are easier to adjust than other types of actuators.
5 New Trends in Electric Actuators
As electric actuators continue to earn their moment in the spotlight, manufacturers are enhancing their electric actuator technologies to boost performance and efficiency and further expand their applications. Take note of the 5 latest trends in electric actuators:
- Replacing Pneumatic & Hydraulic Actuators with Electric: Advances in electric actuator technologies have improved the permanent magnet materials, resulting in more robust and efficient actuators with higher levels of power density, better control and higher speeds than previously possible. As a result, there has been a shift to the use of electric actuators in applications that previously embraced traditional pneumatic and hydraulic technologies. Sustainability goals are also supporting electric actuators in applications as they offer higher levels of efficiency, are leak free, lighter weight and more environmentally friendly than air- and fluid-powered actuators. This trend can be seen across multiple industries, such as industrial applications where manufacturers need to eek out as much speed and efficiency as possible and gain better control in order to get the most throughput from their equipment. Automotive and aerospace are also shifting toward the use of electric actuators in an effort to increase efficiency, gain better performance and reduce weight resulting in less fuel and energy usage.
- Smart Electric Actuators: Actuator manufacturers are beginning to include onboard controls, communication and feedback capabilities, position control and fault detection into some of their more advanced electric actuator models to provide additional benefits. Because control and feedback mechanisms are integrated, it makes it easier to program and monitor the device without the use of external controls. Smart actuators may also achieve higher duty cycles, which helps increase reliability and increases productivity in the application. Many smart actuators employ controls to permit soft starts and allow more precise motor movements. In addition, because smart electric actuators can perform many operational and control functions via onboard controls, it helps reduce the footprint, allowing them to be used in applications with limited space and permitting simplified installation and set up.
- Integrated Actuators: Integrated electric actuators combine the mechanical actuator and servo motor into one device so that the screw assembly is coupled with and driven by a servo or stepper motor. This piece is then integrated with a motion controller to provide several advantages, including a reduced footprint, lower weight and improved force repeatability and acceleration. In addition, the connection helps facilitate a stiff torque transmission, contributing to faster responses, positional accuracy and bi-directional repeatability. Fewer moving components should also provide robustness and reliability in tough applications.
- Higher Force Electric Actuators: For years hydraulic actuators were the choice when the highest levels of force were required in an application, but recent developments related to the force capabilities of electric actuators are making them more suitable in these applications and allow both force and precise control in one unit. This is often achieved by switching out traditional ball screw technology for something that is more robust, such as planetary roller screws, which provides the necessary force and allows use in heavy duty applications that require reliability, as well.
- The Use of Piezoelectric Actuators in Nanoscale Applications: The need for nanoscale positioning systems is growing in both industrial and scientific applications and traditional electric actuators cannot achieve the necessary positioning resolution at the nanoscale. Manufacturers are working to develop piezoelectric actuators for these types of applications as it is easier to control motion in them based on the amount of voltage applied.
For more information on the latest developments in electric actuators and how they can improve your application, please contact JHFOSTER.