5 Conveyor Design Considerations for Maximum Efficiency
Conveyors serve as the circulatory system of most industrial facilities as their function is to move product through the facility for processing. In the same way that circulatory system diseases can wreak havoc on the human body, poorly designed conveying systems can create bottlenecks and waste within the manufacturing plant or warehouse. And, just as investing in our health now prevents illnesses later in life, taking the time to properly design a conveyor system for maximum efficiency before it’s installed thwarts inefficiencies in the future.
To that end, this blog provides five conveyor system design considerations to help maximize material handling efficiency, boost productivity and throughput and reduce costs.
Benefits of Automated Conveying Systems
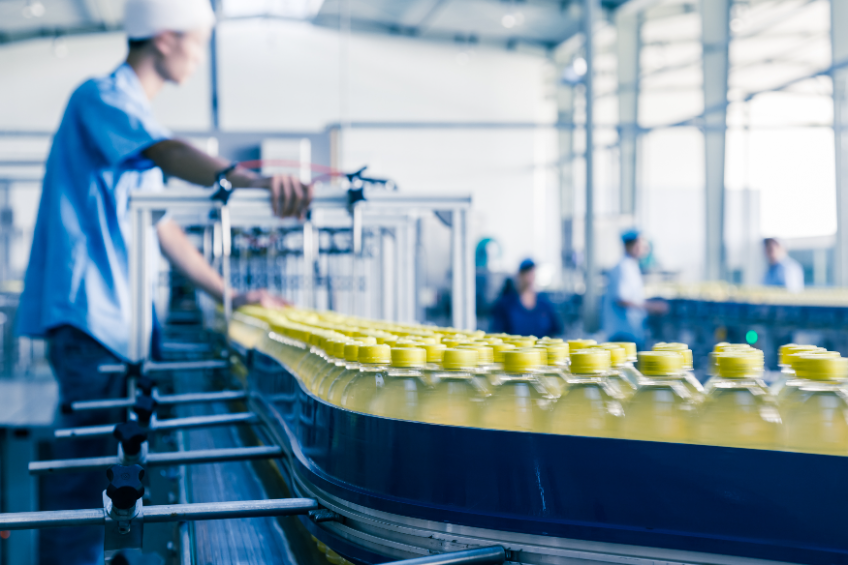
The role of an automated conveying system is to transport materials – anything from boxes to parts to powders – in a way that requires minimal manual labor. Conveyors are available in many types – belt, roller, ball transfer, chute, drag/chain, overhead, screw, vertical and vibrating, just to name a few – to suit all manner of materials. But, no matter the type, most conveyors consist of a frame that supports a mechanism, such as rollers, wheels or a belt, that moves the material from one place to another.
Automated conveyor systems are chosen over manual labor for the many advantages they provide, including:
Streamlined Productivity | By reducing manpower and increasing the speed and efficiency of moving product through the facility, automated conveyors streamline productivity and greatly increase throughput. |
Reduced Labor | Manual material handling requires a lot of manpower, but automated conveying systems reduce the need to hire and retain employees and perform the job at higher speeds and with greater efficiency. |
Improved Safety | By reducing the role of human workers in the movement of materials through the facility, safety is greatly improved. Not only do conveying systems reduce the bending, lifting and carrying motions needed to manually transport goods, but they also decrease collisions, slips and falls and other accidents that might occur as workers carry materials through an active industrial facility. |
Increased Floor Space | Space is at a premium in most facilities and properly designed automated conveying systems take up far less space than the vehicles and tools traditionally used to transport materials through a sprawling industrial facility. In addition, overhead conveyors can sometimes be mounted on the ceiling to free up floor space entirely. |
Less Damage and Fewer Errors | Automated conveying systems tend to be gentler on materials than manual laborers, ensuring higher quality products. In addition, removing the human element reduces the chances of introducing errors into the material handling process. |
5 Design Considerations for Maximum Conveyor Efficiency
Since most modern facilities employ automated conveying systems for their material handling operations, it’s obvious that there are benefits; however, if a system is not properly designed it will not operate optimally and throughput and productivity may suffer. To make certain that a conveying system will provide the most value and efficiency, consider the following at the earliest stages of conveyor system design:
- What Materials are Being Moved? Different products and materials require different conveying technologies and handling methods. Selecting the wrong type of conveyor for a product can cause damage, result in wasted material and drastically slow down productivity. For instance, belt conveyors work well for heavy boxes and parts, but small, delicate items will likely fall off during transport and become damaged or lost. Another factor to consider is whether the material requires skirts or side guards. For example, if the facility moves powders or granules, a side guard can help prevent material loss. For this reason, it’s important to understand not only the type of material the conveying system will be transporting, but also its size, weight and consistency. Additionally, make certain that the load or feed mechanism is also well suited to the material type to encourage the greatest efficiency.
- What Conveyor Speed is Needed? The speed at which the conveyor moves will have a direct impact on the efficiency and throughput of the system, as well as the facility’s overall productivity. It’s important to understand how the weight of the material will impact the speed of the conveyor. Because heavier objects or high volumes of product can potentially reduce conveying speed, it is essential to establish that the selected conveyor can handle the required weight and volume and still meet the necessary productivity levels.
- What is the Available Space? The type of conveyor selected, along with its system of supports, drives and pulleys, will have an impact on the conveyor’s length and layout. Pay close attention to how the system will be laid out within the facility and determine if any existing space constraints will impact layout and, therefore, the operation of the material handling and conveying system. Any obstacles should be removed prior to installation for maximum efficiency.
- What Safety Mechanisms are Needed? Safety features such as emergency stops, controls and guarding are crucial considerations as they prevent accidents and can reduce the severity of injuries caused by pinch points or moving parts. Safety features should be considered and implemented long before the conveyor is active.
- What are the Maintenance Requirements? In order to keep product moving, regular maintenance activities must be performed on the conveying system. Because maintenance is more likely to be carried out when system components are easily accessible, ensure that there is access to conveyor system components during the design stage. Anything that makes it easier and faster to complete maintenance tasks will reduce system downtime and increase productivity.
Taking the time to consider the size, shape, weight and consistency of the material being moved, the necessary throughput rate and the layout and space requirements of the conveyor during the design stage will assure that your conveying system provides optimal operation. Having the forethought to equip the system with necessary safety features will prevent injuries and providing access to conveyor components will promote regular maintenance, further maximizing efficiency. Contact JHFOSTER for more assistance with conveyor system selection and design.