Force Torque Sensors Enhance Robotic Precision and Sensitivity
Traditional industrial robots are optimized for efficiency, speed and accuracy when performing the same movement repeatedly, but they are not able to sense and respond to physical stimuli as is required for more sensitive tasks, such as delicate assembly and surface finishing. However, the addition of force torque sensors allows a robot to “feel” its environment and adapt in real time, bringing higher levels of capability to precision applications.
What is a Force Torque Sensor?
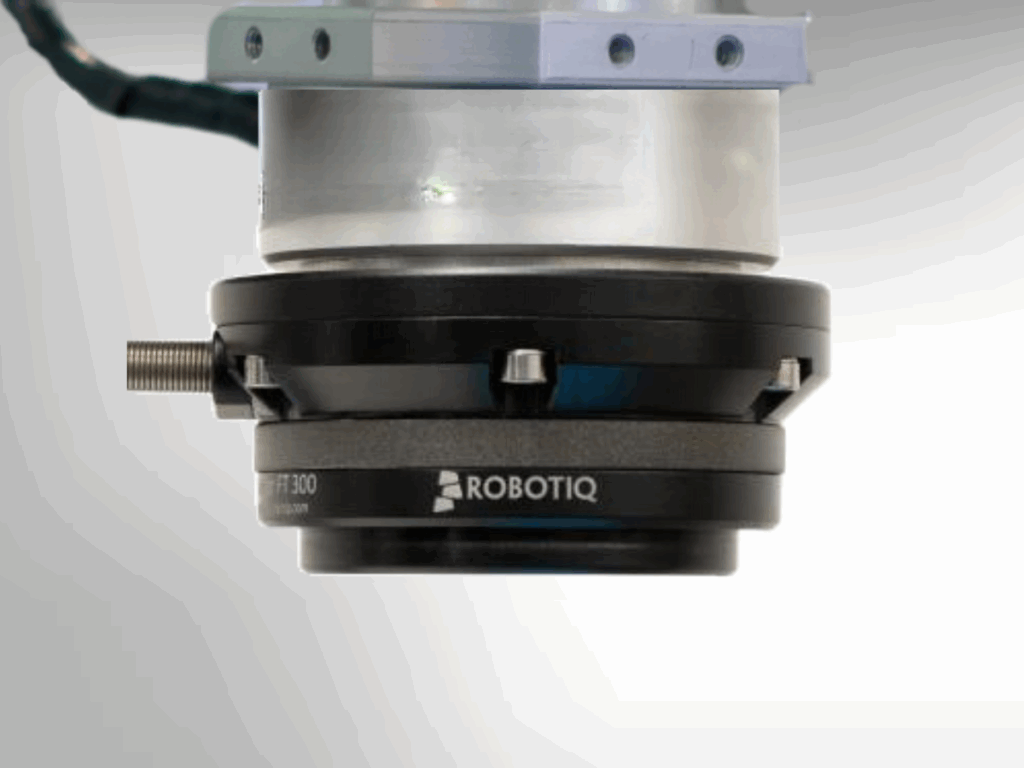
A force torque sensor is an electronic device that detects, monitors and measures force and, based on a feedback loop, adapts linear and rotational forces in response. In simpler terms, force and torque sensors are contact sensors designed to allow intelligent interaction with physical objects encountered in the environment and serve almost like the receptors in human skin that give us a sense of “touch.”
How are Force Sensors Used in Robotics?
Because robots are being applied more often in autonomous applications that demand high levels of sensitivity and frequently operate near human collaborators in work cells, force sensors in robotics act like the sense receptors in human skin, permitting robots and cobots to interact with and adapt to physical stimuli in a way that more closely resembles human interactions.
This means that rather than simply following a preprogrammed path, the addition or integration of force sensors in robotics allows a robot to dynamically adjust or regulate its behavior based on the detected forces, giving it the ability to perform delicate manipulations and activities without damaging components and to function and move about without injuring nearby human workers.
There are several types of force sensors in robotics:
- Six-axis force torque sensors: Usually mounted between the robot arm and end-of-arm tooling, this type of force torque sensor enables a robot to manage force and torque across six degrees of freedom and provides high levels of sensitivity so the robot may be used for high precision tasks such as assembly, insertion and surface finishing applications.
- Single-axis force torque sensors: As the name implies, these sensors focus on just one axis to manage simple jobs that require sensitivity, such as applying uniform pressure to a surface.
- Embedded force torque sensors: Integrated directly into the robot’s joints, this type of force torque sensor is useful in many applications.
Six-axis force and torque sensors are the most commonly used type in industrial robotic applications. In operation, internal elements sense force and torque, and convert this information into electric signals. The sensor relays the data to the control system and, based on real-time feedback, adjusts the robot’s motions, in essence allowing the robot to feel and intelligently respond to its environment.
Without the addition of force sensors in robotics, a robot would simply operate with the same level of force or pressure every time, which could result in damage to delicate components or surfaces or injuries if it collides with workers. For this reason, force and torque sensors are essential to safe, adaptable and interactive robot and cobots as industry moves toward the use of more autonomous robotic applications.
6 Applications for Robots Enhanced with Force and Torque Sensors
Thanks to the introduction of these specialized sensors for force and torque robotics, robots can effectively and safely be used in a growing number of applications that demand sensitivity and precision.
Force torque sensors enhance functionality in the following six robotic applications:
Assembly | Robots equipped with force torque sensors can adjust their force and path in real time, providing precise assembly or insertion of even the smallest and most delicate components. |
Material handling | The feedback provided by force and torque sensors enables robots to pick up and release objects using a precise amount of force to prevent damage and dropping of materials and products. |
Material removal | Force sensors in robotics allow robots to adjust pressure during subtractive tasks such as grinding and deburring, providing consistency and precision and preventing damage in these applications. |
Surface finishing | When polishing, sanding and buffing, force torque sensors allow robots to achieve even surfaces and high-quality finishes by ensuring consistent force across surfaces and contours. |
Pressing and tightening | A force and torque sensor allows a robot to maintain consistent force in these applications, preventing crushing. |
Quality control/inspection | By detecting force anomalies, force sensors in robotics help robots detect material inconsistencies and faulty products during quality testing and inspections. |
How Force and Torque Sensors Enhance Safety
In addition, the inclusion of torque and force sensors in robotics allows collaborative robots to work with human collaborators because the sensors provide precise interaction feedback, enabling cobots to detect objects or humans, sense a collision and adjust speed and force in real time, greatly enhancing safety in collaborative work cells.
Additionally, the enhanced precision and sensitivity to touch coupled with the ability to adapt their behavior based on real-time input, allows robots to be used autonomously in traditionally manual, yet hazardous activities, such as grinding, and to perform these or other activities in dangerous areas, releasing human workers from performing in restricted areas, further boosting facility safety and reducing injuries in human workers.
To learn more about how force torque sensors can enhance sensitivity and precision in your robotic applications, while contributing higher levels of safety, quality and efficiency to the operation, please contact the automation experts at JHFOSTER today.