Preventing Contamination in Industrial Compressed Air Systems
Industrial air compressors keep manufacturing operations in business, so contamination in the system is unacceptable. Compressed air contaminants, such as water, oil, particulates and microorganisms, can degrade compressed air quality and lead to decreased system efficiency, operational safety hazards and contaminated end products – all of which are bad for the bottom line, making contamination prevention a priority.
This blog will look at potential sources of contamination and the havoc it can wreak on productivity, as well as solutions to help mitigate impurities.
Causes of Contamination in Compressors
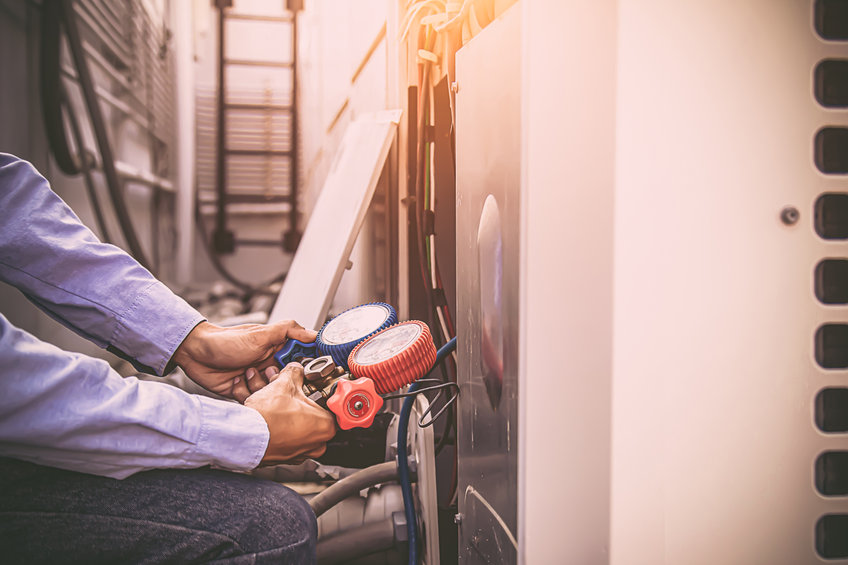
In a perfect world, industrial air compressors would always produce high-quality treated air that meets ISO 8573.1 standards for compressed air quality. For reference, the ISO standard categorizes compressed air quality into classes that specify the maximum allowable limits for particulate matter, moisture and oil.
For example, Class 0 air quality ensures the highest air purity levels for sensitive industries such as medical, food, pharmaceutical and electronics production, while Class 1 might be suitable for general manufacturing applications. More detailed information on achieving ISO 8573.1 can be found here.
Unfortunately, most industrial facilities do not operate under “perfect world” conditions and contamination can be introduced in several ways.
In operation, industrial air compressors draw in ambient air, which may contain water vapor, oil vapor, dirt and microorganisms that can enter the air compression system along with the intake air. Additionally, water vapor concentration will be increased during the air compression process and can cause rust and corrosion or contribute to microbial growth within the system, further jeopardizing air quality.
Common contamination culprits include:
Water | Water may be present as a liquid or vapor due to humidity from ambient air being concentrated during the compression process. |
Oil | Oil contamination is typically a liquid or aerosol and may enter the system with the ambient air or through the compressor’s lubrication system. |
Solid particulates | These can range from dirt and dust in the industrial environment to flakes of rust and pipe scale that result from corrosion within the system. |
Microorganisms | Mold, yeast, fungi, viruses and bacteria can enter the system with the ambient air or can result from water within the system. |
5 Consequences of Industrial Air Compressor Contamination
Compressed air that is contaminated with any of these impurities can have detrimental effects on a manufacturing operation, impacting everything from equipment performance to efficiency to product quality. Here are five consequences of dirty air:
- Reduced equipment lifespan: Contamination can decrease the performance of and reduce the lifespan of equipment that operates with compressed air. Solid particulates such as dirt and rust can enter the air-operated equipment, causing damage and reducing the performance of the tool or machine. Additionally, clogs caused by solid particulates or oil contamination can block filters and reduce airflow from the air compressor, forcing it to work harder, causing wear and tear on the compressor and auxiliary equipment, shortening its lifespan.
- Safety risks: Poor quality air can also result in safety risks as excessive moisture can lead to bacterial and mold growth that can make operators sick. And, if contaminated compressed air is used in the manufacture of finished products that will be consumed, it can result in health problems for customers and necessitate costly product recalls. Additionally, particulate matter can clog tools and machinery, leading to equipment malfunctions that may put operators at risk for injury.
- Decreased efficiency: Any type of debris – whether it’s rust, dirt or oil contamination – can clog air compressor filters, which will force the air compression system to work harder to deliver air to the end use points. This creates a situation in which the system consumes more power to operate, decreasing energy efficiency and system effectiveness.
- Poor product quality: Contaminated air can negatively impact product quality, which is especially dangerous in food, pharmaceutical and medical applications, and very costly in electronics and semiconductor manufacturing. It can also decrease the quality of spray painting and coating operations that require high-quality, clean, dry air to achieve a smooth finish.
- Increased costs: Contaminated compressed air that slows down productivity, degrades equipment or products, decreases energy efficiency or, in the worst-case scenario, results in a product recall will undoubtedly increase costs and have a negative impact on the bottom line.
Industrial Air Compressor Components Mitigate Contamination
Fortunately, there are methods for reducing the effects of contamination in industrial air compressor systems. One of the most effective ways is to ensure that the ambient air drawn into the system has as few contaminants as possible, which requires placing the compressor in a location with low levels of dirt, dust and humidity.
Installing a high-quality air compressor filter at the intake will capture contaminants before they enter the air compressor. However, filters must be inspected, cleaned and replaced on a regular basis as clogged filters will decrease airflow and efficiency of the system.
To minimize water in the system, the use of a refrigerated air dryer, which cools compressed air and extracts water vapor that is generated during the compression process before it enters the system is recommended for most applications. Additionally, water in liquid form can be eliminated with an air compressor water separator, which removes water droplets and other contaminants from compressed air. Automatic drains on water separators, dryers, and filters are required to prevent liquid contamination.
Another option for removing water contamination from compressed air is an air compressor filter dryer. This device should be installed after the air compressor tank and before the air tools or machinery. Air compressor filter dryers remove water by passing the compressed air through a water absorbing desiccant. When it comes to removing oil contamination, air compressor filters designed to capture oil vapors may be sufficient.
Producing high-quality, clean compressed air will ensure that your business runs efficiently, reliably and safely. To learn more about strategies for keeping industrial air compressors contaminant free, please contact the compressed air experts at JHFOSTER, a Tavoron company today.