Understanding the ISA 95 Standard for Manufacturing Automation
The International Society of Automation (ISA) develops standards that help manufacturers streamline processes and improve manufacturing safety, cybersecurity and efficiency. One of the most-often referred to standards is the ISA 95 standard for the integration of enterprise and control systems; however, it can be difficult to understand. This blog will help explain the ISA automation standard, the benefits of compliance and how to prepare for ISA Standard 95 compliance.
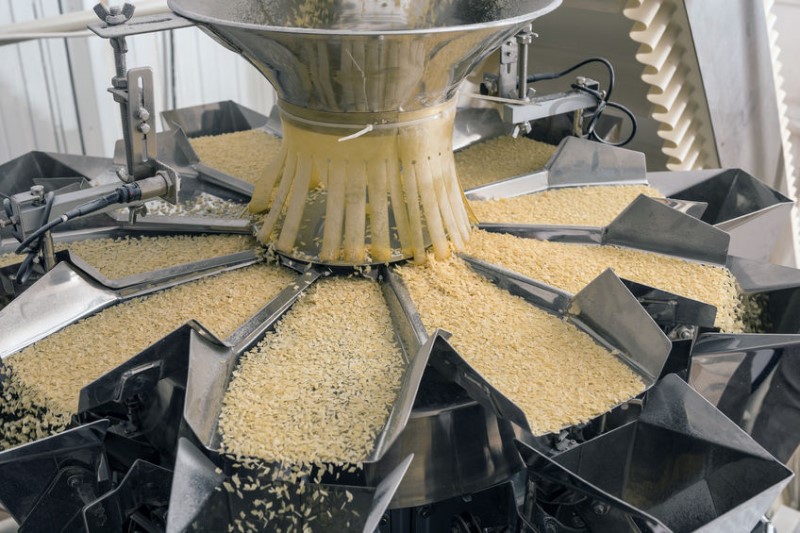
What are International Society of Automation Standards?
ISA automation standards are created by International Society of Automation committees composed of users of automation, automation manufacturing companies, integrators, suppliers and test/certification providers and government representatives. While ISA standards present requirements that a process, system, product or material must satisfy in order to be promoted as meeting that standard, ISA standards are not government regulations. Instead, they are voluntary documents that may be referenced in regulations.
ISA states that their standards help manufacturers increase manufacturing safety, improve communications, reduce manufacturing automation design and implementation costs, enable component and system interchangeability, protect the environment and reduce downtime and maintenance costs, while eliminating the need for large inventories.
What is the ISA 95 Standard?
This ISA automation standard, which focuses on manufacturing automation, covers the integration of enterprise and control systems for manufacturing processes and business processes in an effort to encourage efficient communication and coordination between all the elements of a manufacturing operation.
Specifically, the standard aims to provide a framework for communication between business systems, such as the Enterprise Resource Management (ERP) system, and manufacturing systems, such as the Manufacturing Execution Systems (MES) and Manufacturing Operations Management (MOM) systems, and encompasses plant-floor technologies at the equipment and sensor level.
The ISA 95 standard simplifies the range of technologies through the use of different levels of technology, as follows:
- Level 0 defines the physical processes.
- Level 1 defines the activities involved in sensing and manipulating the physical processes, which includes intelligent devices, such as sensors.
- Level 2 defines the activities of monitoring and controlling the physical processes, which would include control systems such as PLCs and DCSs.
- Level 3 defines the activities of workflow to produce the desired end products, such as the MES system.
- Level 4 defines the business-related activities needed to manage a manufacturing operation, which is likely the ERP system.
The benefits of compliance with ISA Standard 95 include:
- Optimization of workflows across all business levels to enable standardized processes and streamlined communication for more efficient asset utilization and increased production visibility.
- Interoperability that allows common interfaces for MES systems and databases.
- Data accuracy to minimize errors and ensure consistent exchanges of information to support better decision making and reducing operational discrepancies.
Steps Toward ISA Standard 95 Compliance
Compliance with ISA Standard 95 is becoming more important as it provides support for Industry 4.0 and the integration of technologies for Internet of Things (IoT), cloud computing and data analytics into manufacturing automation processes.
While compliance will look different for each manufacturer, there are some common steps that can be taken as manufacturers prepare to adopt the standard. It should also be noted that the International Society of Automation offers resources for ISA Standard 95 compliance, such as classroom training and purchasable texts. These resources should be the first step toward ISA 95 compliance.
In order to comply with the standard, manufacturers need to develop a standardized data model that defines and structures information across all the levels of the operation from the enterprise level down to the plant floor. On the operational side, key elements should include equipment, products, recipes and production processes.
To prepare for ISA Standard 95 compliance on the enterprise level, experts suggest the following actions:
- Train personnel on ISA Standard 95 concepts and how it applies to and improves the business.
- Identify the systems used in the manufacturing operations, such as ERP, MES and PLC systems to determine if they align with ISA-95. Areas for improvement should be noted.
- Configure data exchange protocols to allow integration between the various systems included in the ISA 95 model.
- Establish procedures to ensure accuracy and integrity of the data that will be shared across the various systems.
ISA Standard 95 compliance on the manufacturing floor involves the following:
- Identifying the equipment that falls within the ISA Standard 95 framework.
- Defining production processes as sequences of operations and identifying the needed raw materials, recipes and quality specifications.
- Defining production schedules, recipes and resource allocation.
- Integrating quality data into the system so that quality can be monitored throughout the manufacturing process.
Compliance with ISA Standard 95 ensures that the facility is Industry 4.0 ready and that information can be exchanged between business operations such as sales and logistics and manufacturing operations such as production, maintenance and quality control. This level of integration helps achieve the highest levels of efficiency of your manufacturing automation systems and equipment so that the business can produce high quality products as time and cost effectively as is possible. For more information on purchasing ISA-95 compliant equipment from trusted automation manufacturing companies, please contact JHFOSTER.