Best Practices for an Efficient Compressed Air Distribution System
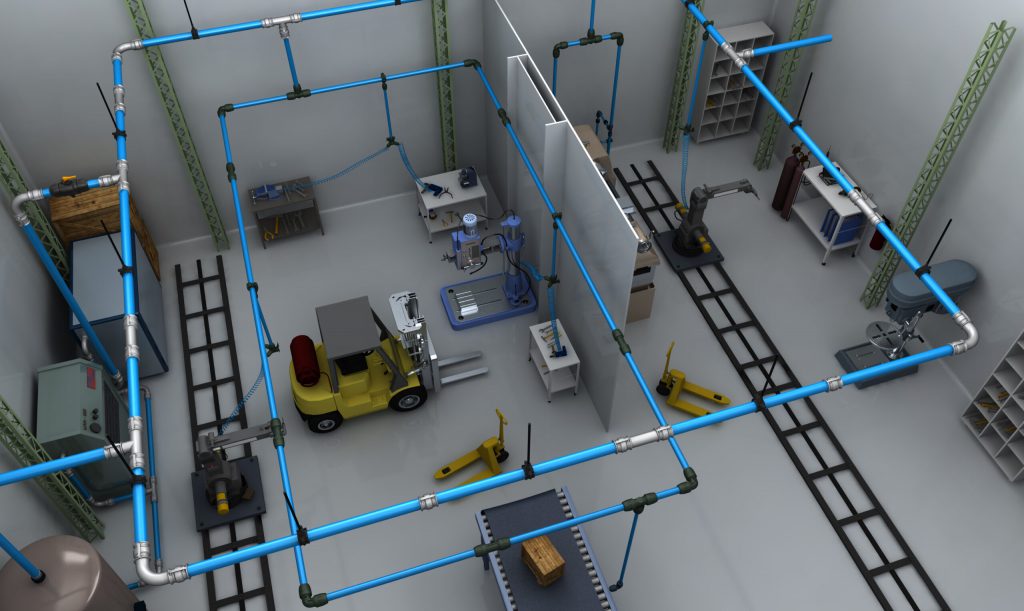
If your facility has been experiencing pressure drops in the compressed air supply and higher than normal electric bills, the culprit may be the compressed air piping system. In fact, issues within the distribution system can greatly influence system performance and efficiency.
Applying best practices to the compressed air piping system will ensure that sufficient air volume and pressure are delivered to the equipment and tools that rely on compressed air for operation. The following six air compressor piping design tips will improve the efficiency and performance of the entire air compression system.
- Choose the Right Piping Material: There are many materials from which to choose. Plastic pipes when specifically rated for compressed air usage, made of acrylonitrile butadiene styrene (ABS), polyethylene (PE) and high-density polyethylene (HDPE) are all good piping choices as they resist corrosion, offer smooth interior surfaces to encourage air flow and are easy to cut to size and connect without the need for welding. While it may be tempting to use polyvinyl chloride (PVC) or chlorinated polyvinyl chloride (CPVC) because it is inexpensive, these plastics cannot withstand the high pressures of compressed air systems and are banned for this use by the Occupational Safety and Health Administration due to concerns that these materials will degrade and shatter under pressure. Metal pipes are another good option as they will not warp or change shape and will not degrade with the use of compressor lubricants. Metal options include black steel, galvanized steel, stainless steel, aluminum and copper. While metal pipes offer rigidity and strength, they are prone to corrosion, which can lead to rust that contaminates the delivered air or causes obstructions in the distribution system. Whatever material is selected, keep in mind that it must meet the airflow and pressure requirements of the system, as well as any specific environmental conditions such as temperature and humidity levels and hazardous materials that may be present in the facility.
- Correctly Size Piping: Piping is available in a variety of different diameters and, while piping can be cut to the necessary length, the diameter cannot be changed, so be sure that the selected diameter is suitable for the required airflow, volume and pressure of the system. If the diameter is too small, the system will be unable to deliver sufficient airflow and will be forced to work harder to deliver an adequate supply of air, leading to inefficient operation and wear and tear on the compressor, potentially reducing its operating life. Equipment and tools also will not perform optimally if piping is too restrictive to effectively deliver air.
- Properly Configure the Layout: The way the distribution system is laid out has a significant impact on the energy efficiency and overall performance of the air compression system. Piping layouts with too many twists, turns, bends and sharp directional changes will create turbulence and pressure drops within the system, forcing the air compressor to work harder to supply air, resulting in increased electric bills, premature wear and tear on the air compressor and poor operation of attached equipment. To decrease turbulence and pressure drops, avoid unnecessary use of elbows, tees, and arrange piping in a way that does not require sharp directional changes so that air may flow freely and without obstruction. Straight runs and the use of 30- to 45-degree turns, and looped systems allowing two paths for compressed air to reach its destination are your air compressor’s best friends.
- Reduce Moisture: Moisture, a byproduct of compressing the intake air, causes corrosion, which may lead to contamination and obstructions within the compressed air piping system that reduce the efficient flow of air, inflate electric bills and create maintenance issues for the entire system. The most effective way to reduce system moisture is to include air coolers, filters and air dryers in the system design, which will work together to remove contaminants, impurities and moisture, helping to extend the lifespan of the system, boost efficiency and ensure the quality of the compressed air supply.
- Install Drip Legs and Drains: Because moisture, the enemy of an efficient, corrosion-free and healthy air compression system, is inevitable due to the process of compressing ambient air, there is a need for drains and drip legs on the piping system. Drip legs should be installed in the distribution piping, even if the system includes an air dryer, to allow excess moisture and water to escape from the pipe. However, be sure there is also a drain to release any collected water. Manual drains must be opened and emptied on a regular basis, while automatic drains should be inspected to ensure that they are not stuck in the open or closed position.
- Keep Maintenance in Mind: Leaks are the leading cause of pressure drops and one of the greatest contributors to air compression system inefficiencies. Even a tiny air leak can result in the loss of thousands of dollars in electricity charges over just a few months. It’s a good idea to invest in a leak detection kit and use it on a regular basis around piping system valves, fittings and elbows, which tend to be prone to air leakage, as well as when the system is experiencing unexplained pressure drops. Any leaks in the piping system should be addressed immediately. For maintenance and safety purposes, the installation of shut-off isolation valves is recommended so that broken components can be isolated from the rest of the system during repair.
A well-designed compressed air distribution system enables efficient delivery of compressed air to air-operated equipment and tools throughout the facility. Choosing appropriate piping materials and diameter, employing the most straightforward layout, removing moisture and properly maintaining the system will go a long way toward reducing system operating costs, prolonging the life of the air compressor and ensuring an efficient and adequate supply of airflow and pressure for optimal performance. JHFOSTER representatives are standing by to assist with air compressor piping design questions.