Troubleshooting Common Pneumatic Control Valve Issues
As part of a pneumatic system, pneumatic control valves play the important role of controlling the flow of compressed air within the system; therefore, minor issues with control valves can have a significant impact on the operation of the overall system. When pneumatic control valves malfunction it can cause upsets that slow down or stop the manufacturing process or, worse, create a dangerous situation within the equipment or facility. For that reason, it’s important to recognize common issues and troubleshoot potential causes so problems can be fixed as soon as possible to avoid costly downtime or potentially catastrophic events.
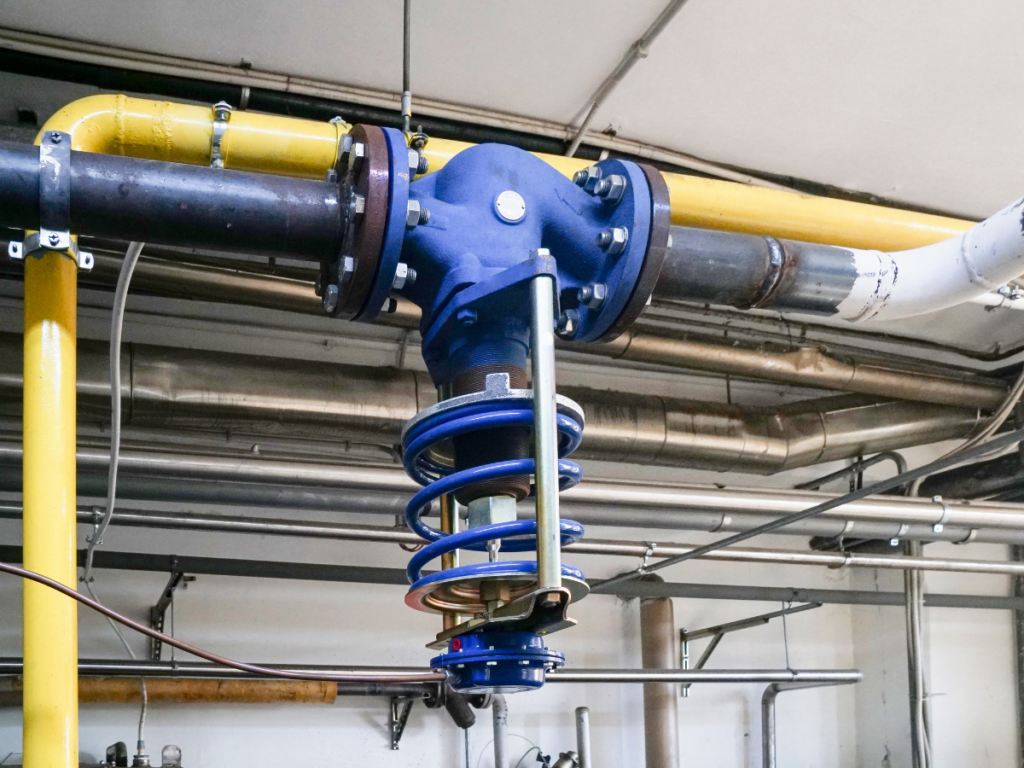
Common Problems and Potential Causes
As mechanical devices, when operated by a PLC pneumatic control valves direct and control the flow of air or gas in the system, so as they deteriorate so too will the performance of the equipment or process they serve. Although some issues can be detected visually, many cannot. Here we will discuss common problems, such as leaks, the inability to close, stiction, hysteresis, crawling and total loss of operation, as well as potential causes.
Control Valve Leaks
Pneumatic control valves may leak externally or internally, but either way, it will cause a drop in pressure, which can have an impact on the pneumatic system and create inefficiencies. Keep in mind that most control valves aren’t designed to shut off 100% and there typically exists a maximum allowable leakage limit; however, if the valve is leaking outside that range, there is a problem. Possible reasons for internal leakage include:
- Worn or damaged internal components
- Dust, dirt, moisture or oil in the air supply
Control valves may also leak externally and this is generally due to issues with the valve packing, such as:
- Improper maintenance
- Excessive temperatures
- Vibration
- The use of incompatible materials
The Valve Won’t Close
There are times when a control valve remains stuck in the open position, which means that air or gas will be flowing freely through the pneumatic system, which can lead to issues with the process or equipment and will certainly create inefficiencies within the system. The most common reason that a valve gets caught in the open position is due to debris being caught in the line. Clearing the debris will typically solve this issue but make sure to inspect the supply line filters and replace elements as needed.
Stiction
Stiction is a combination of the words “stick” and “friction,” so when a valve experiences stiction it means it sticks in a particular position and requires additional force to move it out of that position. This can lead to the valve overshooting its position and getting stuck in the new position or a slower than normal response time. Possible causes include:
- Sticky valve internals
- Dust, dirt, moisture or oil in the air supply
- Undersized or worn valve actuators
- Solenoid issues
Crawling
When a pneumatic pilot operated control valve is experiencing slow motion, or crawling, it can have a negative impact on the pneumatic system. Potential causes for slow movement of the control valve include:
- Pilot supply pressure that is too low
- Tight valve spool or valve assembly
- Pilot air supply passages dirty or plugged causing reduced flow
Valve Does Not Operate
There are times when a pneumatic control valve simply stops working all together and there can be several reasons. Common causes are contamination in the air lines causing the valve to stick or the valve has simply reached the end of its design life and needs to be repaired or replaced. Other causes can be application related and the valve may be employed in a service for which it was not designed, the actuator may not be correctly sized or the positioner isn’t calibrated properly. Many of these issues occur because the valve or parts of the control valve assembly were improperly sized or specified.
Avoiding Pneumatic Control Valve Issues
Hopefully identifying possible causes of common pneumatic control valve issues quickens the troubleshooting process so excessive downtime can be avoided. In a perfect world, unnecessary downtime could be avoided altogether by performing a few simple preventive maintenance tasks and ensuring the system is free of moisture.
Preventively maintaining a pneumatic control valve can help eliminate potential issues because PM programs focus on finding and repairing minor issues before they become major ones. Preventive maintenance for pneumatic control valves should include a visual inspection for wear and corrosion, ensuring there is no vibration in the mechanical assembly, calibrating the positioner, repairing any leaks, bends or discoloration in the pneumatic tubing and replacement of worn components with properly sized parts.
Because pneumatic systems run on compressed air, which can contain moisture that may come in contact with the control valve and cause corrosion or a host of other issues, it’s important to catch moisture with dryers and filters before it enters the system and the valves.
Pneumatic systems depend on many ancillary components to operate. Because pneumatic control valves are directing air or gas through the system, it’s important to identify and correct potential issues before there is a time-consuming and costly shutdown. While not an exhaustive list of everything that could be amiss with a pneumatic control valve, this blog provides troubleshooting for commonly encountered problems, as well as advice on how to prevent them in the future, so your pneumatic system runs as effectively and efficiently as possible. For more information on pneumatic control valves, please contact JHFOSTER.