What are Three Different Types of Pneumatic Valves?
Traits of Pneumatic Valve/Directional Control Valves
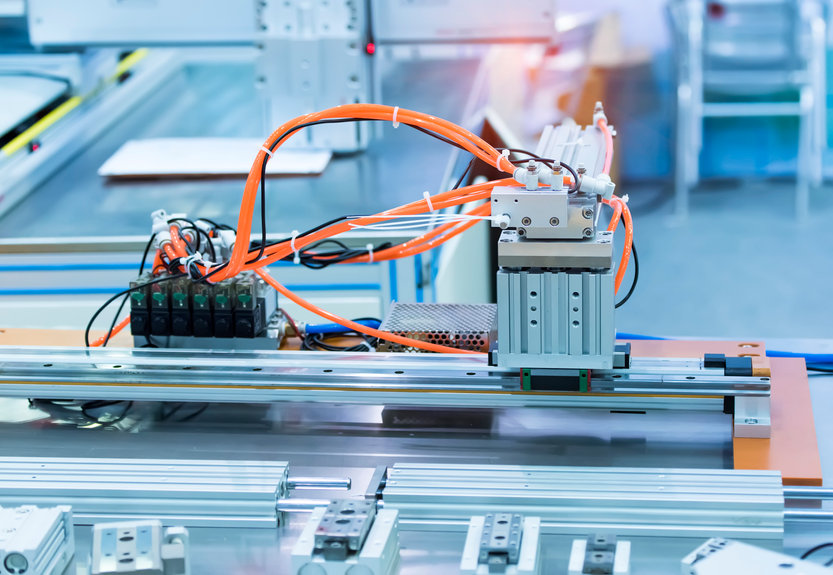
They block or divert the flow of compressed air or other gases within the system. These valves are sometimes used to pilot other valves. They all have different features designed to achieve a desired flow outcome. You can choose a valve with a spool or a poppet arrangement.
Spool arrangement
A common type of directional control valve that has a spool design. It can be shifted to two, three or more positions to route the air between inlet and outlet ports. Spool valves are used when controlling actuators. As a single valve, spool valves can control extension, retraction and neutrality in a pneumatic actuator.
Poppet arrangement
Poppet style valves have a simple design. It uses a face seal that opens and closes (often with a spring return) against a valve seat. These valves offer a higher flow. They are often used in harsh environments.
What are some of the most common types of directional control valves?
Solenoid Operated Valves | Air Operated Valves | Mechanical Valves |
Solenoid valves are designed to open and close in response to an electric signal. They control airflow in a pneumatic system and liquid in a hydraulic one. Solenoid Valves are used for their versatility and durability. | Instead of receiving an electric signal, they respond to air pressure that applies force to a piston or diaphragm. You will see air-operated valves in environments that demand a pneumatic output but don’t want to rely on electricity. They are commonly used in chemical factories and fertilizer manufacturing facilities. | Mechanical valves can use manual or mechanical contact within the machine for operation. They can be used in systems where electricity would be dangerous or impractical for the tasks required and can be used for air or liquid flow. Typically energy is applied to a manually operated valve using hands or feet on a lever, button or pedal. Or, mechanical contact within the machine mechanism on a ball, plunger or cam operator provides the energy for operation. |
Applications for Solenoid Valves | Applications for Air Operated Valves | Applications for Mechanical Valves |
Solenoid valves are commonly used in industrial workplaces, for manufacturing processes. Robotic end of arm tooling, automated actuators, and end effectors often depend on pneumatic solenoid valves for actuation. | When located in hazardous areas where electricity isn’t available or desired. Simple automated manufacturing fixtures using air logic for control vs electronics can provide a low cost, reliable solution. | They can be used for many applications within industrial manufacturing, such as manually operated gates, clamps and presses or as limit switches used on a machine or fixture. They are also commonly used as manual shut-off isolation valves and two hand anti-tie down devices for safety. |
What are the seven basic requirements of valves to consider when choosing one?
Media
Type and properties of liquid or gas that will be controlled by the control valve. Temperature and pressure? Is it negative pressure? Be sure that the valve is compatible with the media, temperature and pressure passing through.
Flow Capacity (valve size)
Determine the maximum flow capacity that your application requires. Choose the valve size with the right capacity. Valve suppliers will provide the flow capacity for each valve. Your valve will need to fill a specific downstream volume within your required time period.
Pneumatic Valve Configuration
Most pneumatic directional control valves are 2-Way, 3-Way, or 4-Way. The specified number (2, 3, or 4 in this case) is a count of their active media ports.
2-Way Valves
They have one inlet and one outlet port. Upon actuation, media is allowed to pass through or to stop flow.
3-Way Valves
These valves add a third port to allow for venting of pressure at the outlet port, when the inlet port is blocked.
4-Way Valves
These valves add a second outlet and corresponding second exhaust port to the 3-Way function. They are commonly used for control of double-acting pneumatic cylinders and actuators.
Method of Valve Actuation
There are a variety of methods that can be used to close or open a pneumatic control valve. The four most common methods of valve actuation are as follows:
- Manually operated (via a pushbutton, foot pedal, lever etc.)
- Mechanically operated (via work pieces or tooling in contact with a ball, cam or plunger)
- Remote air pilot operated (via an output signal of another valve)
- Solenoid operated (via electric current)
Environment
Make sure your valve is compatible with the environment it will be in, standard industrial production area, wet, sanitary washdown or hazardous are a few examples.
Safety
Make sure the valve chosen will operate safely and have the correct function when the E-Stop is actuated.
Spring-Return
This is a common return method used to take the pneumatic valve “home” to its original, unactuated state. Typically, valve return is either a mechanical spring or a separate form of the same actuation method as described above. In essence, you need to determine if you are looking for a “momentary contact, momentary output” or “momentary contact, maintained output.” Determine if you want your valve to return to its initial position or stay in its last position after actuation.
For additional information on Pneumatic Valves, please refer to this JHFOSTER blog: What are the Different Types of Pneumatic Valves?
What if I have questions about Pneumatic Valves?
At JHFOSTER, one of our technicians would be happy to speak with you about choosing the right Pneumatic Valve for your process. We work with our clients to help them achieve optimal efficiency in their facilities. JHFOSTER is a leading distributor of automated systems and robotics. A JHFOSTER representative is available at 651.998.7294 or 855.688.0043