Pneumatic Systems: 101
Chances are if you work in an industrial facility, you’ve handled tools and equipment that are powered by a pneumatic system. These simple, yet powerful systems use clean, dry compressed air to create mechanical motion that powers tools, machinery and industrial automation systems. Learning about the components involved in a pneumatic system and how they work together can be helpful to those operating the pneumatically driven equipment or those charged with designing a pneumatic system.
Pneumatic System Components
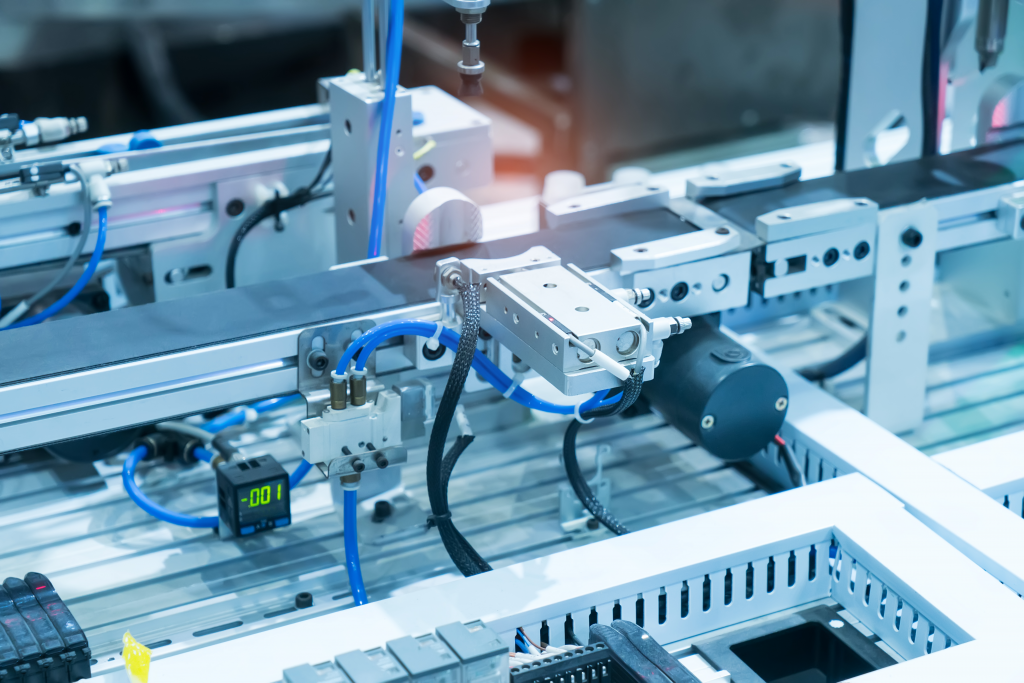
Pneumatic systems are composed of several components, with the heart of the system being an air compressor. The air compressor, driven by an electric motor, takes in ambient air and compresses, or reduces, the volume of the air within an enclosed chamber, which increases the pressure. Typically, there is also an intake filter, which serves to remove large-sized particles, such as dust and dirt, from the air being drawn into the air compressor.
Other components include aftercoolers that decrease the temperature of the compressed air, separators that remove condensation, additional filtration and air dryers that remove particulate, moisture, oil and water vapor from the compressed air. Many pneumatic systems, especially those with varying flow requirements also include an air receiver with flow/pressure regulator which is used to store the compressed air. These air treatment components are essential to the pneumatic system as they allow the air compressor to supply the cool, clean, and dry air that is needed for reliable and consistent operation of pneumatically operated tools and equipment.
Pressure switches that detect an increase or decrease in the air pressure and/or control valves may also be part of the system. Control valves regulate, control and monitor the downstream pressure of the produced air and change the direction of the airflow.
The final part of the pneumatic system is the distribution system, which is also essential for achieving top-notch performance. The distribution system includes the piping that leads to the end point or points of use. There should also be drains included in the distribution system so that any accumulated moisture can leave the system to prevent contaminated air and corrosion within the system. Distribution piping and tubes should always be sized properly and as straight and simple as possible to minimize pressure drops.
How Does a Basic Pneumatic System Work?
Together all of the above-mentioned components work to supply the air that powers everything from tools, presses, spray painting equipment, process equipment, and factory automation. Here’s how it happens:
Air is taken directly from the surrounding atmosphere and cleaned of dirt and debris via the intake filter. Next, the air enters the compressor, which is driven by an electric motor, and does its job of compressing the air by increasing the air pressure and decreasing the air volume within its chamber. The compressed air is then passed along to the aftercooler and/or wet receiver tank which reduces the air temperature and removes condensation through a water separator while keeping the pressure steady. The air is then sent through a filter to remove particulates and dried via an air dryer to remove moisture and humidity then goes to a final filter to remove any remaining small particulates or oils. Following these air treatment steps, the processed air is sent to the dry air receiver where it is stored for use. When needed, the air travels through the flow/pressure control valve which sends the clean, dry, compressed air to the end point destination via the distribution system of pipes and/or tubes. Finally, an air actuator is likely used to convert the energy of the compressed air into mechanical energy, which allows it to power and create motion in the tools or equipment at the point of use.
The Advantages of Pneumatic Systems
Pneumatic systems are widely used in industrial facilities because they provide a reliable source of power to a multitude of tools and automated machinery. Other advantages of pneumatic systems include:
- Simple design: The simplicity of pneumatic systems makes them ideal for use in manufacturing, packaging, and air-operated tool applications.
- Durability and reliability: Pneumatic system components tend to be resistant to damage, making them suitable for use in industrial facilities where they may be subjected to rough handling or dirty, harsh environments.
- Effectiveness: Because of their ability to produce high speeds and forces from a small actuator, pneumatic systems can be a very effective solution for many industrial processes.
- Safety: Pneumatic systems can be an excellent choice where using electrical power could cause a fire or explosion hazard. Pneumatic systems are also more environmentally friendly than hydraulic systems as they do not mandate the need for hydraulic fluids that can leak and require proper disposal. Further, after use, compressed air can be released back to the atmosphere without the need for cleaning or other processing.
- Accommodate varying demands: Pneumatic systems can be easily adjusted to accommodate the air/power requirements, multiple users and varying demands within an industrial facility.
For assistance selecting components for a pneumatic system for your application, please contact a representative at JHFOSTER.