4 Automation Trends Food Packagers Should Consider for 2023
As the food and beverage consumption rate continues to grow – with total revenues in the food and beverage industry expected to grow from $1.95 billion in 2022 to $3.69 billion by 2027 in the U.S. – the food packaging industry will have to hustle to keep up with rising demand. But amidst labor shortages and reduced budgets, keeping up with this kind of growth can be challenging.
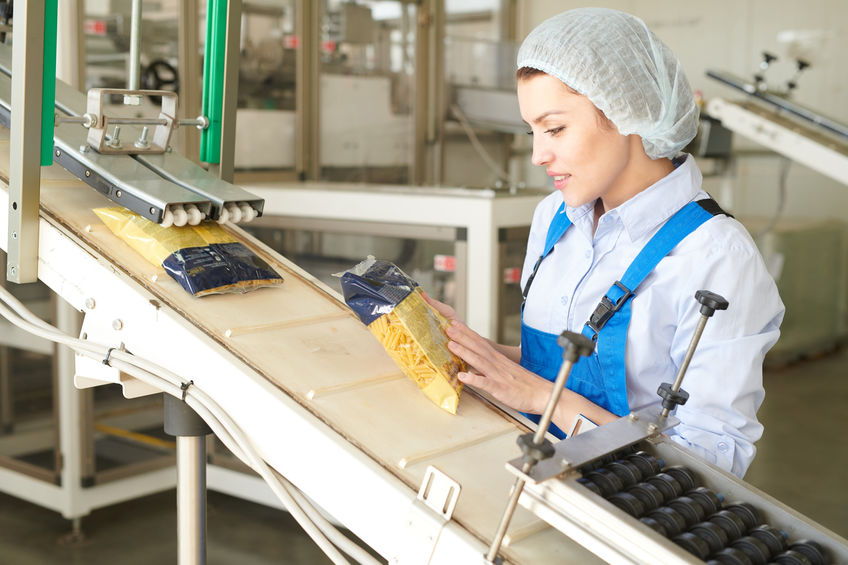
While many food packagers have already implemented automation in their processes to boost throughput, recent trends and advances in automation technology can help bring food packaging operations to the next level. The growing use of smarter equipment, robotics, advanced motion control technologies and machine vision will allow food packagers to not only meet production quotas, but to do so with improved efficiency, sustainability, uptime, finished product quality and food safety.
The Benefits of Automation in Food Packaging Operations
Realizing that there were several benefits to be gained by automating food packaging operations, companies in this segment of the food industry were early adopters of automated equipment. The advantages of automating food packaging applications include:
- Increased efficiency: Despite labor shortages, food packagers must swiftly move product out the door and automation alleviates bottlenecks by completing work faster and with more reliability than human workers performing the same function. Automation can also run 24/7 if needed during times of peak demand.
- Improved quality: Quality control is essential during food packaging processes. Automation standardizes quality control because every product goes through the same process from beginning to end, which results in consistency and accuracy. Additionally, automation technologies for inspection can be programmed to detect quality issues that human workers may overlook.
- More flexibility: Easy-to-program automated equipment allows food packagers to keep up with variable product lines. In addition, automation can easily be scaled up or down to meet seasonal demands and customer preferences.
- Improved sanitation: The more human workers interact with food, the greater the likelihood of introducing contamination. Automated equipment limits human contact with food items during the packaging process, thus reducing the chances of contamination.
- Lower operating costs: The cost of running automated packaging machinery is often lower than hiring and training employees. Because automated food packaging equipment runs faster and more consistently than human operators, throughput will increase while scrap and waste will be reduced, further enhancing cost effectiveness.
- Improved safety: Food packaging involves high-speed machinery, repetitive tasks and heavy lifting. Automating these processes may eliminate potential injuries to employees and the costs associated with worker’s comp claims and lost labor due to injury.
Food Packaging Automation Trends in 2023
While the general benefits of automating food packing processes are motivating, the addition of newer technologies can provide even more advantages for the food packaging industry. Here’s a look at four trends we can expect to see more of this year.
1. More Digitalization and Smart Equipment
Smart automated packaging equipment that is enhanced with digitalization and Internet of Things (Industry 4.0) connectivity provides a wealth of benefits for food packagers. First, it may help enhance uptime if collected machine data is analyzed and used for maintenance purposes. By detecting potential machine issues before they cause breakdown and alerting maintenance techs to potential problems, they can be attended to prior to a total shutdown of the packaging operation. In a similar vein, smart machines and Industry 4.0 connectivity allow the use of remote and mobile access, which provide new ways to oversee operations, perform real-time machine diagnostics and troubleshoot problems from any location.
Smart technologies also enable intelligent packaging that boosts quality and food safety. Connected sensors and other technologies can help monitor and improve the packaging process using real-time monitoring of product or packaging quality, real-time monitoring of temperature for perishable products and tracking and traceability for regulatory requirements.
2. Increasing Use of Robots and Cobots
While robots and collaborative robots, or cobots, have always been reputed to increase efficiency and speed in food packaging and palletizing operations, technological advances in grippers and end of arm tooling are permitting the use of robots in food packaging applications where it was previously not possible. Gentler grippers allow robots and cobots to pick up and place delicate items such as baked goods and fruits and vegetables into packages, increasing efficiency in what were previously manual packaging operations. In addition, robots and cobots are becoming easier to reprogram and reconfigure, which allows them to quickly accommodate changing packaging lines, increasing flexibility. Further, the ability of robots and cobots to accurately and consistently perform a task makes them capable of placing grains, nuts, ready-made meals and just about any food product into pouches or packages while achieving the same weight or fill rate every time, increasing quality and reducing waste.
3. Advanced Motion Control for Flexibility
Food packaging is always changing due to consumer demand for the same product in various sizes or types of packages, seasonal preferences and other variables. To enable this type of flexibility on a food packaging line, automated equipment is being enhanced with advanced motion control technologies that provide flexible programming methods, allowing food packagers to easily switch from one operation to another. Modern automated equipment with advanced motion control allows food packaging operations to program one machine with a variety of set points for different product runs, speeds or packages. The ability to quickly change from one packing process to another further enhances productivity and efficiency because it reduces downtime associated with changeovers.
4. The Addition of Machine Vision
A machine vision system comprised of specialized sensors and cameras can be incorporated into automated equipment and robots to provide a host of benefits for food packagers, with quality improvements being the greatest advantage. Automated equipment equipped with machine vision can be used to inspect product as it is packaged, ensuring the food itself meets quality standards. It may also be used to ensure that the package itself is in good shape and that labels are aligned correctly and applied to the proper package, boosting product quality, consumer satisfaction and compliance. Using machine vision-enhanced packaging equipment to ensure quality also helps reduce waste and scrap, helping to cut associated costs.
Automated food packaging equipment that includes one or more of these trending technologies will help food packagers increase production efficiency and flexibility, while also improving product quality and consistency, enhancing food safety and assisting with regulatory compliance. To learn more about these and other food packaging automation trends, please contact JHFOSTER.