Top 5 Considerations for Proper Compressed Air System Installation
A well-designed compressed air system will provide many years of reliable service…as long as it has been installed in accordance with industry best practices. To ensure smooth, trouble-free operation for years to come, be sure to pay as much attention to the details of how the system is installed as you did to selecting a properly sized air compressor and accessories. This blog will highlight the top five considerations for a successful compressed air system installation.
While it does require some effort to plan for proper installation, taking the time to consider all the important factors will help prevent issues that could lead to unscheduled downtime and/or premature equipment failure. In addition, correct installation provides several benefits, including:
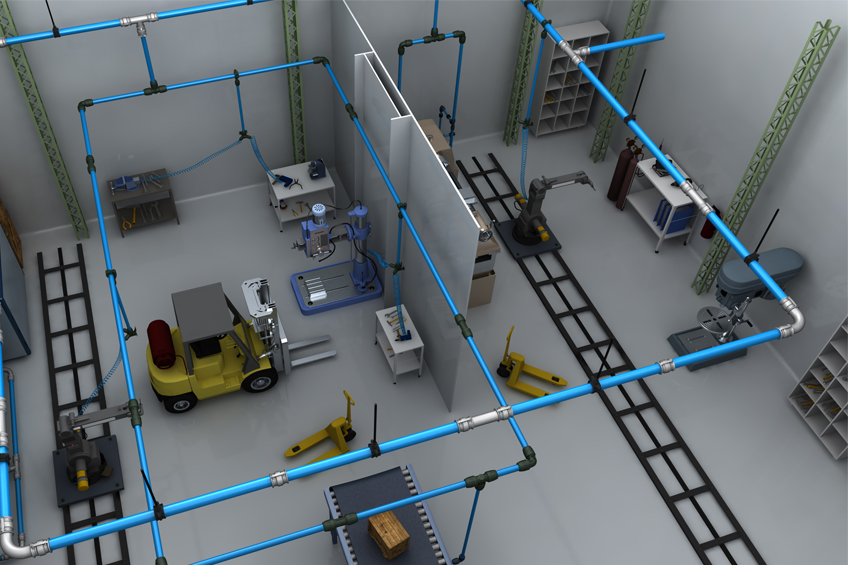
- More energy efficient operation
- Optimized performance
- Reduced maintenance and downtime
- Lower total cost of operation
- Longer service life
- Warranty compliance
- Compliance with safety and local planning codes
- Improved quality of compressed air
Because these are all valid reasons for thoughtful planning, here are the top 5 installation factors to consider:
1. Location
When possible, compressed air systems should be installed indoors in a dedicated room located close to the end user. Ensuring that the environment around the compressors is clean, dust free and dry will help maintain optimal temperature of intake air, provide a higher quality of produced air as there will be fewer contaminants drawn into the system and prolong the life of the equipment as it will not be exposed to outdoor elements. In addition, compressed air equipment should have at least 3 feet of clearance on each side to permit adequate air cooling and heat exchange and allow for future maintenance access. The foundation where the air compressor is placed should be level and stable to prevent the compressor from shifting and vibrating during operation. Creating a suitable location for the air compressor will ensure that the system provides a consistent level of performance many years into its operation.
2. Ventilation
As mentioned above, the best location for an air compressor is indoors, but that space must be well ventilated. A lack of ventilation is the leading cause of performance and maintenance issues in compressed air systems, so proper ventilation will help ensure good performance of the system and prevent overheating that will undoubtedly lead to costly repairs and downtime. Natural ventilation will occur if ample room surrounds the compressor on all sides, as mentioned above. Forced ventilation can also be provided through air ducts that help control the flow of hot air exhaust from the compressor or by exhaust fans that draw warm air out of the room.
3. Power Requirements
It is crucial that the electrical service voltage matches the voltage requirements of the compressor. Equipment must be grounded and equipped with appropriately sized fuses or circuit breakers installed between the compressor and the main power service. All electrical work should be conducted by qualified electrical contractors and electrical work must comply with local and national codes and regulations.
4. System Configuration
Many components make up a compressed air system and these should be arranged in a way that permits optimal performance. To provide ample airflow and steady pressure to all points in the system, pipes from the compressor to the components of the system should be carefully sized to limit pressure drops and laid out so that there are no complex twists or turns. Braces should be used to secure pipes to floors, walls or ceilings to avoid movement or stress on the pipes and joints. Flexible connections are sometimes necessary to isolate vibrations and compensate for expansion and contraction caused by temperature variations. Additionally, an air treatment system including filters, dryers and drains suitable to the operation should be installed to provide clean, dry compressed air to the plant, preventing air quality and maintenance issues down the road. Dry receiver tanks are also recommended as they serve as a reservoir of compressed air during times of peak demand, which will help increase system efficiency and prevent pressure drops. A wet receiver tank can also improve compressor performance while allowing the air to cool before entering the air treatment equipment, reducing the load on the air dryer and filtration. Plant flow controllers can also be utilized to maintain useful receiver tank storage while providing consistent pressure for production. All components should be properly sized for the system and the air requirements of the facility.
5. Plan for Maintenance
In addition to proper sizing of the air compressor and components and securing a proper installation, creating and following a preventive maintenance plan early on will prove to be the most effective way to avoid unplanned downtime and to ensure optimal performance in the years after installation. Routine tasks should include regular cleaning and inspection of the air compressor and components as system efficiency can be adversely impacted by the sludge, dust and dirt that can accumulate. In addition, routine inspection of coolers, pipes, hoses, connections, traps, drains, motor fans, drip trays, belts and lubricant levels can help keep the system running as efficiently as possible. These inspections ought to detect air leaks, which should be addressed to prevent losses of efficiency and energy. Filters should also be checked and changed on a regular basis as dirty filters can impact energy efficiency and the performance of the system. Contracted service providers are available to perform routine maintenance, as well as any necessary repairs, and should be considered in facilities where air compressor maintenance is neglected due to time constraints or lack of a skilled workforce.
Being aware of the importance of proper compressed air system installation will not only speed up the process, but also will prevent maintenance and performance issues later on and may help extend the service of the equipment and keep the warranty current, making planning for and carrying out a proper compressed air system installation a worthwhile effort.
For more information or assistance with planning, installing or maintaining your air compression system, please reach out to JHFOSTER.