Compressor Controls Increase Efficiency and Cut Costs
Industrial facility owners must balance skyrocketing energy costs, aggressive sustainability goals and stiffening environmental regulations with cost reductions and increased demand for productivity. And, it is likely that the vast majority of these industrial facilities employ an air compression system to power equipment and processes. While air compressors do provide a convenient and clean supply of energy, they are not known for their energy efficiency.
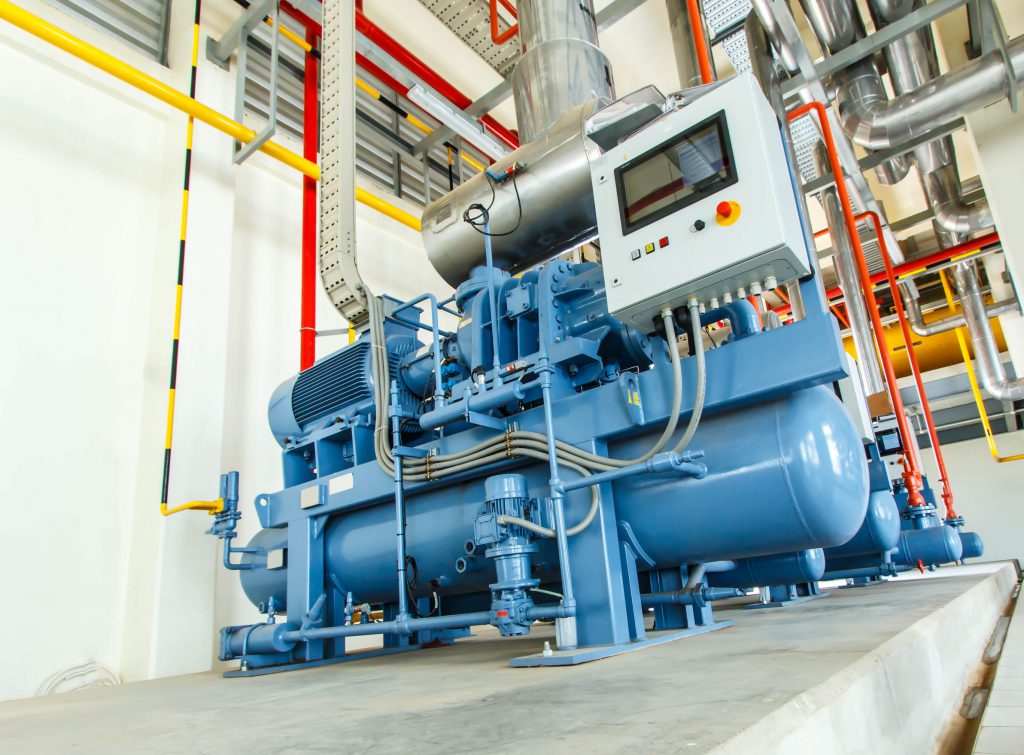
As a matter of fact, the U.S. Department of Energy estimates that up to 50% of compressed air power is lost during normal operating conditions, which is directly at odds with cutting costs and becoming more sustainable.
However, compressor controls – especially modern, intelligent control systems – can boost energy efficiency and optimize performance of air compression systems, resulting in significant reductions to the electric bill and making it easier to achieve sustainability goals and regulatory compliance and improve production performance.
Compressor Control Options
The complexity of a control scheme will depend on the compressor system. For example, an air compression system with a single air compressor and a steady demand can get by with a simple compressor control system, while a complex system with multiple compressors, variable demands and a variety of end-use equipment will require a more advanced control method. Either way, compressor controls will contribute to the bottom line by ensuring that the air compression system is running as efficiently as possible while also providing enhanced performance. Control systems are composed of sensors and electrical components that determine the running conditions of the compressor and allow operators to make necessary adjustments, while innovations in sensors and microprocessors have markedly increased controller functionality. Below are the types of controls that are available:
Start/Stop | Load/Unload | Modulating |
A simple control strategy, start/stop type controls turn the motor driving the air compressor on or off based on the pressure signal. | Load/unload controls permit the motor to run continuously but unload the compressor when the setpoint for the pressure limit is reached. The air compressor will be commanded to reload based upon a predetermined lower discharge pressure setting. | Also known as throttling or capacity control, modulating control restricts inlet air to the compressor to gradually reduce air compressor output to a specified minimum, at which point the compressor is unloaded. |
Variable Displacement | Dual/Auto-Dual | Variable Speed Drives |
Variable displacement control authorizes progressive reduction of the air compressor displacement efficiently maintaining consistent compressor output pressure while compressed air flow demand fluctuates. | When used on small reciprocating compressors, dual/auto-dual control allows the selection of either start/stop or load/unload. In lubricant-injected rotary screw compressors, this control strategy provides modulation to a pre-set reduced capacity followed by unloading with the addition of an overrun timer to stop the compressor after running unloaded for a pre-set time. | Variable speed drives adjust air compressor capacity by varying the speed of the electric motor driving the compressor in response to system signals efficiently maintaining consistent compressor output pressure while compressed air flow demand fluctuates. |
Many of today’s compressor controls are intelligent controls that are capable of providing advanced functionality that further boosts energy efficiency. Advanced controls often offer remote monitoring, allowing users to adjust compressor settings according to specific events in real time, allowing informed decisions to be made on the fly from anywhere using current data to minimize downtime and energy consumption and improve performance. Intelligent, adaptive controls can also continuously monitor key performance parameters, such as airflow, pressure, operating cycle and energy consumption, and encourage the compressor to automatically react to changes and then alert the operator.
Depending on the set up, advanced, intelligent control can also be used to determine the health status of the compressor and alert maintenance departments to issues such as low oil levels or high temperatures, so that they may be addressed before reducing system performance or causing unplanned downtime.
Control Functions for Increased Efficiency
Monitoring and controlling different aspects of the compressed air system helps compressed air users run a more energy efficient operation by keeping compressor operation stable and running at optimal performance conditions. It does this by:
- Ensuring that the compressor is running at optimum RPM
swith appropriate air inputs and expected outputs, allowing stable operation of the air compression system and optimized energy consumption. - Allowing the compressor to make adjustments to the system based on preset pressure limits, so the system remains within optimal performance ranges, according to its pre-programmed settings.
- Automatically shutting down the compressor as needed to conserve energy and then restarting it automatically when pressure decreases.
- Ensuring that the compressor starts and stops safely.
- Allowing users to predetermine loading and unloading times, which keeps the unit running when needed to reduce motor starts and short idle periods.
- Variable drive and speed controls allow compressors to adjust the speed of the motor as needed to balance performance with efficiency. This will also reduce wear and tear on the compressor’s motor and airend.
- Providing system information that can determine the health status of the compressor, as well as environmental variables outside the compressor that are critical to its operation. This information can be used to ensure that the compressor is not having any maintenance problems or to alert techs to issues that may soon require maintenance.
- Automatically shutting down the system during unsafe conditions to prevent catastrophic failure of components or hazards to the facility and employees.
The ability to monitor and control an air compression system can make a significant difference in the performance, reliability and efficiency of the system, which has a direct and positive impact on the facility’s daily operations, its sustainability and its electric bill.
For more information on choosing compressor controls, please contact JHFOSTER.