What Should I Expect During an Air Energy Audit?
Compressed air systems are a necessity in most industrial facilities as they power many machines, tools and processes; however, they are notorious for consuming significant amounts of energy.
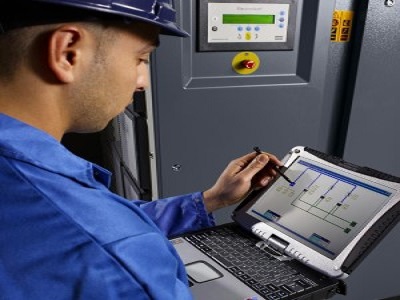
As a matter of fact, the U.S. Department of Energy says that as much as 10% of all electricity generated in the United States is used by air compressors and HALF of that energy is wasted! In the current climate of reducing operational costs and going green, facility managers may be asking themselves how they can rectify the inefficiencies within their air compression system. The answer: An air energy audit.
The Benefits of an Air Energy Audit
An air energy audit is used to determine whether the existing compressed air system is performing efficiently or not. Auditors will uncover areas of loss and make recommendations for correcting inefficiencies. In almost all cases, the audit will help reduce energy usage and costs and may also improve compressed air quality, uncover minor system issues before they interfere with operation and increase the availability of the system and its operating lifetime.
- Reduced energy usage: The majority of the total cost associated with a compressed air system comes from operating it, with about one-third of the expense being electricity. Since the main goal of the air energy audit is to find inefficiencies, making the auditor’s recommended adjustments to the system should help increase the efficiency and reduce the facility’s electric bill, which can provide a significant savings.
- Improved air quality: Malfunctions with the filtration and drying systems and other components can introduce corrosion, contaminants and moisture into the system, which will reduce the quality of the generated air. Making recommended adjustments to these components will result in better functionality of the system and improve the quality of the produced air, which will likely have a positive impact on your operations and finished products.
- Increased uptime and system lifecycle: Since corrosion, broken and improperly sized parts can reduce the operating life of the air compression system, discovering and rectifying these issues before they cause an outage will increase system availability and may also lengthen the lifecycle of the air compressor and its components.
What to Expect During an Air Energy Audit
Compressed air energy audits can usually be conducted on almost any budget and without disrupting production. There are various levels from a basic, walk-through audit performed by in-house staff to a full-system audit led by professionals that include leak detection, data logging, power and flow rate measurements, and recommendations for improving efficiency and preventive maintenance activities. A full-system audit conducted by a professional take about one to two weeks and can cost thousands of dollars but is likely to drive efficiency and functionality improvements that can reduce the facility’s current electric bill by 10% to 50%. Utility providers may offer rebates and incentive programs to help offset the cost of professionally performed audits.
There are several steps involved in an in-depth, professional air energy audit, as follows:
- Site Survey: The first step in an air energy audit is the site survey in which the auditor conducts a walk through of the facility to create a list of the compressed air system components and layout, including the make and model of the compressor, storage system and piping or delivery system. The auditor will determine how the components currently interact with each other and may identify obvious system flaws.
- Air Study: During the site survey, data logging equipment will be placed throughout the system to measure energy usage and air pressure. The measurement period should be at least one week and should include periods of normal operation, downtime and peak and non-peak usage.
- Data Analysis: After collecting the air study data, the information is analyzed using a software that builds a profile which tells the air auditor the flow range and power range of the system. Reports are created that detail system efficiency, compressed air system costs, air flow demand and inappropriate usage. This report should also uncover areas of inefficiency and loss, incorrectly sized or damaged equipment and other maintenance issues and include recommendations for improving system issues, such as fixing leaks, curbing over-pressurization, installing flow control valves and/or upgrading components.
- System Verification: While it is up to the system owner to take action to correct identified inefficiencies and system malfunctions, in order to reap the benefits of the audit, it is important to prioritize and accomplish suggested tasks. After the recommended improvements have been made, the owner can schedule a follow-up visit from the auditor who will measure system performance and identify the achieved reductions in energy usage and improvements in efficiency and functionality.
Although there are costs associated with auditing a compressed air system, the increased efficiency and improved reliability often make the investment worthwhile, as statistics show that significant reductions in compressor maintenance and energy costs are likely to be achieved in a year or less.
Please reach out to an expert at JHFOSTER for more information or to schedule an air energy audit for your facility.