How to Select the Best Industrial Robot for Manufacturing Applications
As robotic technology continues to develop, more manufacturers are applying industrial robots to automate tasks that are repetitive or dangerous for human workers or those that create bottlenecks within the facility.
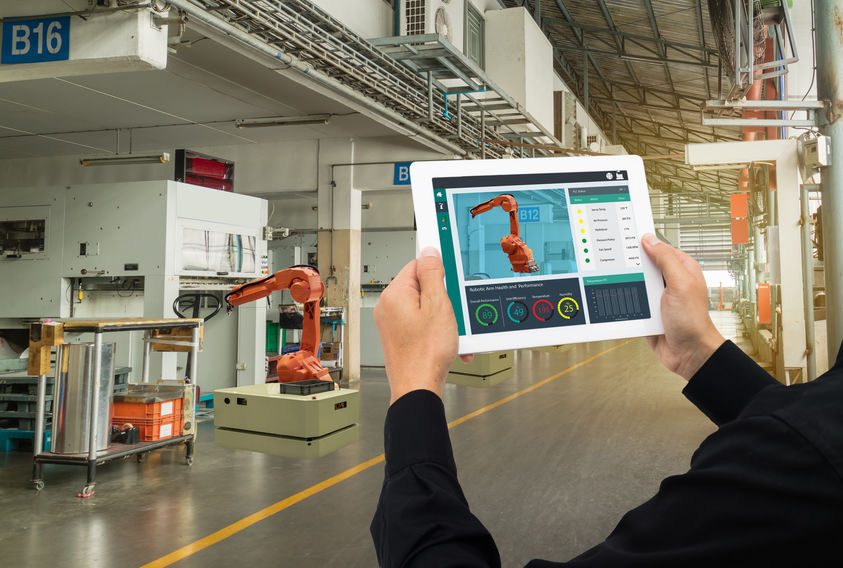
In these situations, robotic automation can increase productivity and efficiency, boost product quality and improve safety in a variety of manufacturing sectors. While the advantages of robotic automation are plentiful, so too are the available choices, making robot selection a bit challenging. This blog will explore the various types of robots commonly used in manufacturing facilities, as well as some criteria that will help you choose the best robot for your manufacturing application.
Common Industrial Robots and Applications
While the term “robot” makes many of us think of Rosie from the Jetsons, today’s industrial robots are not only less sassy than Rosie, but they are also designed with specific features and attributes that make them suitable for efficiently accomplishing heavy-duty, swift-moving, manufacturing applications rather than household chores. Here are the five most common types of industrial robots used in manufacturing:
- Cartesian Robots: Cartesian robots feature three prismatic joints that deliver linear motion by sliding along the three perpendicular axes (X, Y and Z). Some Cartesian robots have an attached wrist that allows rotational movement. This configuration provides positional accuracy and handles heavy loads. Usually positioned above a workspace, Cartesian robots can maximize floor space and accommodate a range of part sizes. Simple to operate and easy to customize, Cartesian robots are widely used in pick-and-place, loading and unloading, material handling and assembly applications, as well as CNC machines and 3D printing; however, they are not able to reach into or around obstacles and an exposed sliding mechanism makes them a poor choice for very dirty or dusty work sites.
- SCARA (Selective Compliance Assembly Robot Arm): SCARA robots feature two parallel joints, allowing lateral motion in one selected plane. The rotary shafts are positioned vertically and an end attachment on the arm moves horizontally. SCARA robots offer high speeds and excellent repeatability, making them good choices for assembly, packaging, palletizing and machine loading applications. They are also found in semiconductor wafer handling and biomed applications. SCARA robots are a good choice when vertical assembly tasks are required. They are also lightweight and offer a small footprint. Their fixed, swing-arm design can create limitations when they need to work around or reach inside objects within a work cell.
- Delta Robots: Consisting of parallel joint linkages connected on a common base that is mounted above the workspace, Delta robots are capable of performing delicate and precise motion at high speeds. Delta robots are suitable for rapid pick-and-place applications in the food, pharmaceutical and electronic industries. Because the actuators are typically mounted on the stationary base instead of at each joint, the robot’s arm can be very lightweight, allowing rapid movement in high speed applications involving light loads.
- Articulated Robots: The mechanical movement and configuration of an articulated robot resembles that of a human arm. The arm is mounted to a base with a twisting joint and has anywhere from two to ten multiple rotary joints, which serve as axes. Each additional joint provides another degree of motion. Offering superior flexibility, reach and dexterity in a small footprint, articulated robots are often found in food packaging, welding, material handling, automotive assembly, steel cutting, machine tending and foundry and forging applications. They can also reach into a machine and under obstructions when needed. Sealed joints and protective sleeves allow use in harsh manufacturing environments; however, they are not ideal when high speeds are required.
- Collaborative Robots: Collaborative robots, or cobots, are specifically designed for integration into workspaces that are shared with human co-workers. Close proximity to operators necessitates that they are built in a way that allows them to be safe, even if they cross paths with or bump into their human counterparts. They find use in pick-and-place, palletizing, quality inspection and machine tending applications.
Selection Criteria
While the abundance of robotic technologies enables even small- and medium-sized manufacturers to take advantage of the increased efficiency, product quality and safety benefits offered by automation, it can make selecting an appropriate robot confusing and tricky. The best robot for the job is usually the one that not only provides productivity gains, fits the budget and satisfies the needs of the application, but also suits the space and safety requirements of the manufacturing facility. Below are the most important selection criteria:
- Application Details: Knowing what you want the robot to do and where it will be placed are critical when selecting an industrial robot. For instance, if the robot will work in a cell with human workers, a collaborative robot will likely be your best option, while SCARA robots are well suited to pick-and-place activities in small spaces and Delta robots are skilled at handling small items at high speeds. In order to be sure, you’re picking the right robot, it’s important to really clarify the task, which means itemizing and considering each step, along with factors such as the distance the robot will need to move or reach and the weight of any objects the robot will have to manipulate.
- Required Reach: It is essential to know the maximum distance the robot will need to reach in order to efficiently accomplish the task. Consider the maximum vertical reach (measured from the lowest point that the robot can reach to the maximum height), as well as the maximum horizontal reach (the distance from the center of the base to the furthest point it can reach horizontally). Range of motion, expressed in degrees, should also be considered. Robot providers should offer this information. Often, the application specifications will dictate which robot can be used.
- Robot Payload: This is the maximum load that the robot can handle, including the part the robot will handle, as well as any end effectors or grippers that will be added to the robot to accomplish the task.
- Number of Axes: The number of axes directly relates to the flexibility of the robot. While selecting a robot with the necessary number of axes needed for a task will satisfy the application, choosing a robot with additional axes means it may be moved to a more complex application down the road. However, additional, unused axes will still have to be programmed. Typically in simple applications, such as pick and place, a 4-axis robot will satisfy most requirements; however, more axes will be required in confined spaces where the robot arm needs to twist or move in reverse.
- Running Speed and Travel: The robot’s speed over the required distance is a major factor in how quickly the robot can accomplish the task. If the robot needs to complete a high pick rate, a Delta robot may be the best choice, while a Cartesian or SCARA robot will be suitable for lower pick rates.
- Repeatability: Repeatability is the ability of the robot to reach the same position each time it completes a routine, so in applications where high accuracy is required (such as assembling electronics), the better the repeatability needs to be. Applications with high repeatability criteria may also want to consider how many brakes the robot features since brakes directly relate to achieving repeatable positions.
- Space and Footprint: The available size of the area in which the robot will be expected to perform is important during the selection process. Confined areas and obstacles will impact this, as well. If space is very limited, vertically oriented robots like Cartesian and Delta robots, will be most suitable.
- Robot Body Weight: The total weight of the robot is important information as it is crucial to designing the cell and for proper mounting of the robot so that it may be properly supported during motion in order to avoid safety issues.
- Protection Class: If the robot will be used in applications where food, medical instruments, laboratory equipment or flammable products are manufactured, it may require a certain level of protection. Some automation providers offer different levels of protection for the same type of robot depending upon the environment or application in which the robot will be applied.
- Risk Assessment: To fully ensure the safety of the robot in a specific scenario, it is necessary to provide a risk assessment for each robot before placing it on the facility floor. If the assessment reveals that there are hazards despite any built-in safety features, action must be taken to provide any necessary protective measures, especially to fully ensure the safety of human operators around collaborative robots.
The above-mentioned selection criteria will get you off to a good start when researching robots as the most suitable industrial robot for a manufacturing application is the one that not only provides the speed, payload and reach necessary for the task, but also meets the spatial and safety requirements of the application and facility.
For assistance selecting the most appropriate robot technology for your application, please contact JHFOSTER.