Vision-Guided Robotics Excel in Machine Tending Operations
Machine tending robot automation has increased the efficiency of tasks involved in this repetitive operation. However, there can be some significant challenges associated with alignment and calibration of machine tending robots due to the complex workflows and precision requirements of many of these processes. Fortunately, the introduction of stand-alone vision-guided robotics has made machine tending automation simpler and more efficient than ever before.
This blog will showcase the benefits of using stand-alone VGR-enabled tending stations in repetitive, high-volume loading and unloading operations.
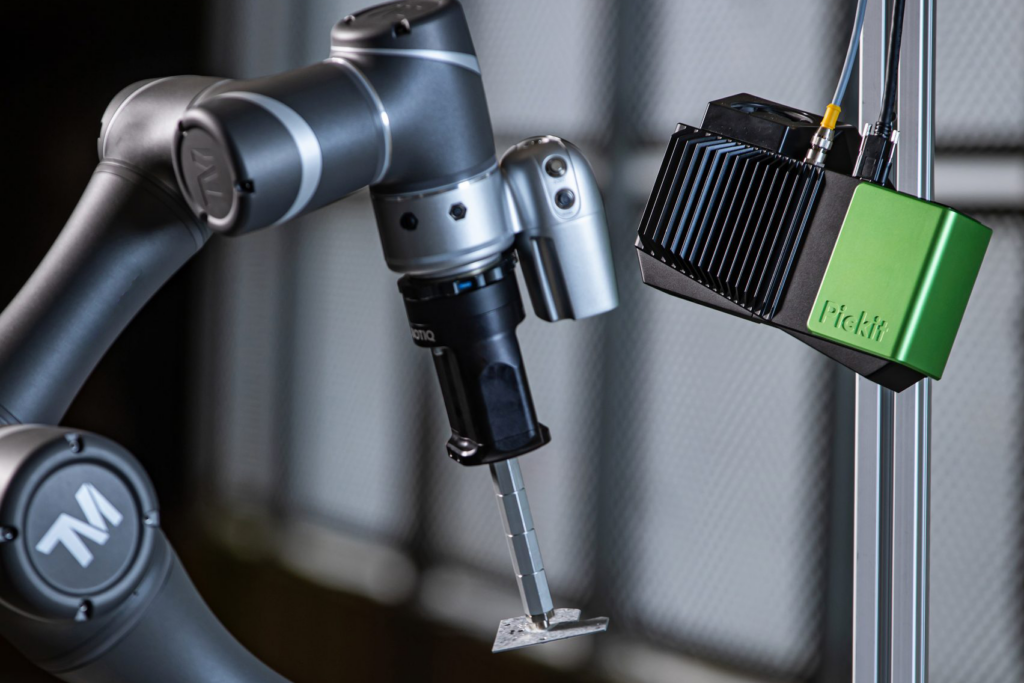
What is Machine Tending Automation?
Let’s begin from the beginning with an explanation of machine tending and how machine tending robots have improved the efficiency of these repetitive, but necessary, operations.
Machine tending involves loading raw materials or parts to a machine, unloading the finished product upon completion of the cycle and then restarting the process over again. While the work was traditionally performed via manual labor, human workers often found the job boring and repetitive and it was a safety risk because repetitive motion injuries can be caused by the bending, lifting and twisting actions the task demands. In addition, employees were often too slow to keep pace with these high-volume processes, causing bottlenecks and inefficiencies.
To solve these problems, robotic machine tending solutions were developed to more efficiently load and unload parts. Traditional machine tending robots can communicate with process machinery and perform several functions in a single application. Machine tending automation is capable of changing from one step to the next in the machine tending process and can provide the speed and precision necessary for managing even complex operations.
In these roles, traditional machine tending robot can operate with little to no human intervention and can be programmed for manipulation and transport of materials. This allows them to efficiently and precisely pick up products from a supply location, take it to the machine, place and orient it, operate the machine and remove the product when the cycle is finished and start the process again.
The high speeds associated with traditional machine tending robot automation help to increase facility throughput and reduce bottlenecks, while the accuracy of robots improves the quality and consistency of products, reducing errors, material waste and re-work. Robotic machine tending can also minimize safety issues associated with manual labor.
The Challenges of Traditional Machine Tending Automation
However, in complex, high-volume machine tending workflows, it can be challenging to guide a robot’s end-of-arm tooling based on the way an object is positioned on a tray. Directing the robot arm to the proper pick up location is often difficult to calibrate, as is achieving proper alignment between the gripper and the object. Accurate placement of the object on a tray can be problematic, as well.
These challenges can result in a loss of efficiency and precision, which can slow down the process and produce lower quality products.
Vision-Guided Robotics Provide an Advanced Machine Tending Solution
Vision-guided robotics (VGRs) can help overcome these obstacles to further increase the efficiency and accuracy of robotic machine tending. VGRs are essentially robotic arms with an integrated machine vision system, which helps the robot discern the location of the object and more accurately guide the robot to the desired location.
With stand-alone VGR-enabled tending stations, a camera captures and analyzes an image of the object and then sends precise coordinates to the robotic arm so that it can move to the desired location with higher levels of accuracy. This type of VGR technology allows the robot to become an autonomous solution that can precisely locate a part moving on a conveyor or a stationary part on a supply table, accurately pick it up and place it in the proper position/place.
Stand-alone VGRs offer single-camera solutions with automatic hand-eye calibration, allowing them to extract feature locations for the supply of parts and the final nest, permitting accurate and efficient loading and unloading of parts for complex, high-volume machine tending applications.
The Advantages of Using Stand-Alone VGRs for Machine Tending
The enhanced efficiency and accuracy introduced by stand-alone VGR-enabled tending stations allows them to provide a host of benefits in complex, high-volume and highly repetitive machine tending applications.
The advantages of stand-alone VGRs as robotic machine tending solutions include:
Increased productivity | Stand-alone vision-guided robotics can work autonomously at high speeds, increasing production rates and throughput. |
Enhanced quality | The vision system and automatic calibration associated with stand-alone VGRs enables precise gripping, handling and placement of objects, minimizing errors and defects and enhancing product quality. |
Improved safety | Because stand-alone VGR-enabled tending stations remove the need for human workers on machine tending lines, safety risks associated with repetitive motion injuries are minimized, improving the safety record of the facility. |
Reduced costs | By eliminating the need for manual labor in machine tending operations, VGRs can help reduce labor costs and costs associated with injuries. Minimizing errors also reduces the costs associated with scrap and rework. And reducing bottlenecks will curtail costly downtime on the production line. |
Flexibility | With the ability to easily calibrate and guide stand-alone VGRs, they are adaptable to a variety of parts, positions, orientations and locations, which allows vision-guided robotics to handle a variety of machine tending tasks. |
For more information on how a VGR can enhance your repetitive, high-volume machine tending operation with higher levels of accuracy, speed and efficiency, please contact the automation experts at JHFOSTER today.