Troubleshooting Motion Control Malfunctions
Motion control is a critical part of automated equipment and machinery found at industrial facilities. Malfunctions can result in downtime, wasted material, and safety issues. Quickly finding and fixing root causes will eliminate these losses and lead to reduced production delays. This blog will provide information on how to troubleshoot your motion control system so you can discover the root cause of the problem, fix it, and get back on track.
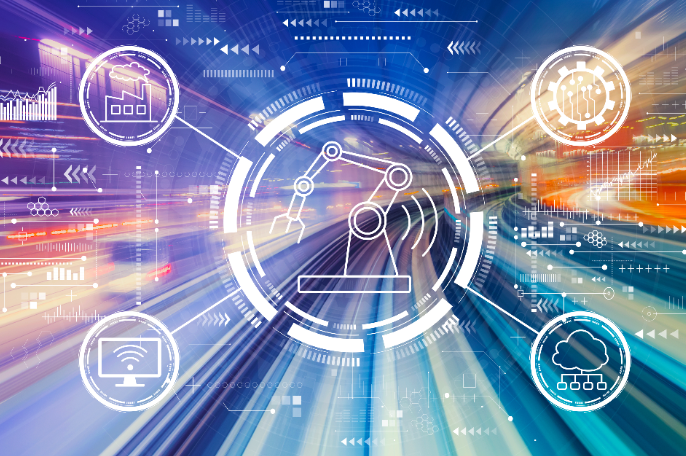
Troubleshooting
Issues with motion control systems can range from complete stoppages to intermittent occurrences. The troubleshooting process begins with the intended operation and behavior of the machine and the contrasting symptoms of the issue. This will help determine which component is responsible or what outside influence may be triggering the issue.
If production cannot be stopped to allow for troubleshooting the problem, then operators should be asked to document and record the details of the malfunction, such as the exact time and location of the occurrence and any other variables of importance.
Many of today’s motion control systems include data historians, event logs, and performance trends to help diagnose malfunctions by narrowing down their timing and preceding events. If the malfunction occurs intermittently or data from the motion control system is not available or obtainable, it may be beneficial to set up a data logger and video/audio recording equipment.
Precise Diagnosis
Once you fully understand the intended behavior versus the actual behavior, you can conduct a much more focused troubleshooting. If the end-effectors, manipulators, pneumatics, hydraulics, rails, bearings, shaft keys, shear pins, and other mechanical hardware are undamaged and behaving normally, then that narrows it down to the motion control system. It’s important to note that motion control is a system of multiple components that work together to provide powerful, efficient, and accurate movement of the machine axes. Each part of the motion controller, the drive, the motor, and the feedback device play a role in achieving precise control and performance.
If we rationalize the situation, the programming and firmware of the motion control system could not have suddenly changed on its own. The controller’s memory is very stable and redundant for safety. The most likely culprits are the moving parts; especially any of the electrical cables that are vibrating or frequently flexing.
Just like a paper clip, copper wires can only bend so many times before they break. This is a common cause of intermittent issues because the broken copper strands intermittently disconnect and reconnect while the cable flexes. The most expedient approach is replacing the cable/s that connect the motion controller to the motor that is misbehaving. If the issue persists, then the next most likely culprit is the feedback device. It is fragile, so it may have been damaged if the machine crashed. If it was without power for a long period of time, it may have forgotten where it’s zero position is. Start by checking the zero position of the axis and recalibrate it if necessary. If the issue persists, try replacing the feedback device. If the issue persists, then investigate the motor which might be wearing out and overheating, assuming it was correctly sized in the first place. The last thing to check is the motion controller because it experiences the least wear and exposure. During this period of troubleshooting, it is recommended that you document and track the components that have been replaced and the results.
If testing or replacing multiple components at once, try to keep it to two or three changes at a time as any more than that can complicate the troubleshooting process.
While it can be time-consuming to go through data files and set up data loggers to troubleshoot a motion control system, investing the time will help you find the root cause of the problems now and in the future. Being methodical and documenting the troubleshooting process will likely help resolve future problems faster as well.
For assistance troubleshooting your motion control system, please contact a representative at JHFOSTER.