The Rise of Electric Actuators
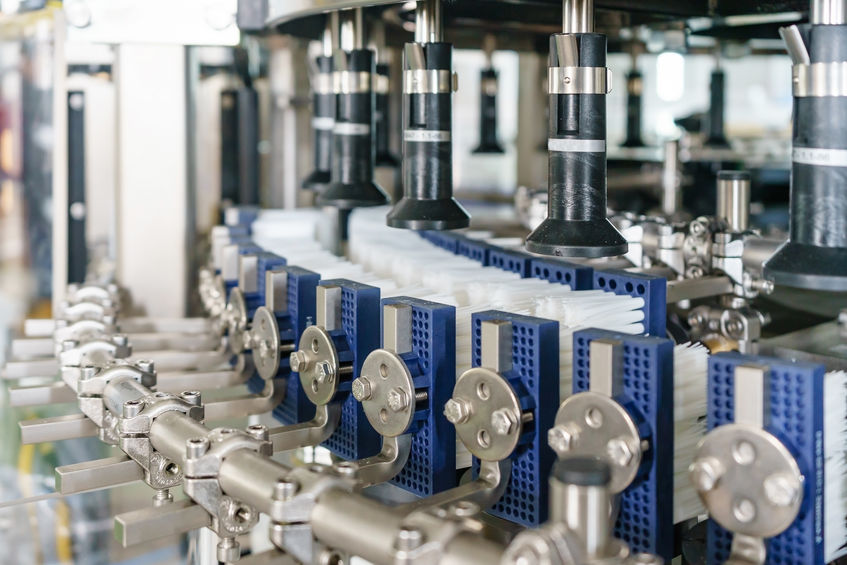
Traditionally electric actuators were not the device of choice for heavy-duty machinery, industrial equipment and other systems that demanded motion profiles with high forces and extreme robustness. However, reduced costs for these electric devices combined with recent technological advances are making designers reconsider electric actuators for use in these and other applications, giving rise to electric actuators.
Advantages of Electric Actuators
Although some drawbacks, such as lower force capabilities and more complex and less durable designs, previously prevented the use of electric actuators in heavy-duty and industrial applications, the devices are not without significant advantages. For example, they offer high positional accuracy because they are digitally controlled and, therefore, are capable of extremely accurate control of speed, position and acceleration. In addition, electric actuators provide great stability at slow speeds due to a smooth motion profile and the ability to easily program and adjust them. Further, electric actuators are more energy efficient and environmentally friendly as they require neither compressed air nor hydraulic fluids and only draw electricity when in motion, not when resting. And while electric actuators are more complex due to their feedback devices and other components, many are self-contained, which makes them easier to install and set up and provides a lighter, more compact footprint.
Advances in Electric Actuation Technology
Historically, these advantages have made electric actuators stellar candidates for use in applications such as medical devices, lab equipment, electronics and other applications where cleanliness, compact size, precise control and slower speeds were required. However, because motion control designers wished to take advantage of the benefits of electric actuation in more challenging applications, new electric actuators, capable of providing higher forces, greater robustness and more intelligence, have been developed. A few of the most noteworthy advances include:
Higher Force and More Robust Electric Actuators | While hydraulic actuators were typically the go-to technology for applications where high force and high durability were requirements, stronger, more robust electric actuators are now available. Developers are switching out traditional ball screw technology for planetary roller screws, more advanced precision ball screws or other mechanisms and using new and improved component materials to provide significantly higher forces, allowing electric actuators to easily compete with hydraulic devices in operations that require heavy load handling, improved durability and longer life in challenging applications. |
Different Motor Technologies | The inclusion of brushless motors in some electric actuators allows for devices with high power densities, as well as increased maintenance intervals and significantly extended duty cycles, making them more suitable for use in equipment that is expected to run 24/7 in harsh conditions. |
Longer Stroke Length | Among other advances, electric actuators are now available with extended stroke lengths. Traditional electric actuation devices were capable of maximum stroke lengths of less than 500 millimeters per stroke. Some of today’s electric actuators can achieve lengths of approximately 1 meter or longer. |
Smarter Electric Actuation for Better Control | Onboard controls, communication and feedback capabilities, position control and fault detection are now offered in more advanced electric actuator devices, further enhancing control and accuracy. Integrated control and feedback mechanisms simplify programming and allow monitoring of the device without external controls. The use of VFD controls permits soft starts and more precise motor movements. With all operational and control functions performed via onboard controls, electric actuators offer smaller footprints and lighter weights than ever before. As an added bonus, this also simplifies installation. |
Boldly Going Where No Electric Actuator Has Gone Before
As the technology behind electric actuators continues to advance, it is opening the door for the use of electric actuators in applications where they were not previously suitable, including:
- Heavy-Duty Machinery: Traditionally powered by hydraulic actuators, electric actuators are now being used to create lifting, pushing and pulling motions in heavy-duty construction and agricultural machinery thanks to longer stroke lengths, greater durability and higher force capabilities. These applications can now take advantage of the greater precision, accuracy and slower, more controlled stops provided by electric actuation technologies.
- Aviation and Aerospace Equipment: While the industry has always relied on hydraulic actuation, the demand for lighter weight and more environmentally friendly components had designers yearning to employ electric actuators. Thanks to the increased robustness and reliability of today’s electric actuators, aerospace and aviation systems can take advantage of the superior performance, compact size and lightweight of electric actuators.
- Material Handling Systems: Like heavy-duty machinery, material handling systems often required the use of hydraulic or pneumatic actuation due to the challenging loads, operating conditions and 24/7 duty cycles. However, thanks to new developments that provide electric actuators with greater force capabilities and more robustness, material handling equipment, such as conveyors and packaging equipment, can take advantage of the longer duty cycles and operating life, as well as the traditional benefits of cleanliness and better energy efficiency.
- Solar Panels: Thanks to developments that increase reliability, stroke length and force capabilities, solar panels, which must reliably change position to directly face the sun throughout the day, can take advantage of the enhanced control, smooth operation, slower motion profile, compactness and energy efficiency provided by electric actuators.
- Industrial Equipment: Industrial cutting equipment, lifts, presses, robots and other machinery used in manufacturing facilities that were previously powered by hydraulic or pneumatic actuators can now employ today’s electric actuators. The higher forces, enhanced control, longer strokes and greater durability make today’s electric actuators suitable for these demanding applications. Industrial equipment will benefit from the greater energy efficiency and environmentally friendliness provided by electric actuators, as well as the extended maintenance intervals and reliability, which are key in an industry where increasing sustainability and reducing costs are always corporate goals.
These and other technological improvements are giving rise to the use of electric actuators in many applications where they were traditionally not considered. For more information on how today’s more advanced electric actuators can enhance your motion project, please contact JHFOSTER.